The transplanting mechanism can be regarded as a two-bar manipulator. The positive and negative planetary gears in the eccentric gear box drive the positive and negative planting arms respectively. A seedling pushing mechanism composed of a swing cam mechanism and a sinusoidal mechanism in series is added to the planting arm, as shown in the figure. The fixed coordinate system xo1 y is established on the axis of the central wheel, and the position coordinate equation of point P on the claw tip of the forward side seedling is as follows:
Among them, φ 10 is the initial installation angle of the axis connecting line of the eccentric gear box relative to the positive direction of the x-axis, counterclockwise is positive, taken as 0 °; φ 20 is the installation angle of the connecting line from the planetary gear axis on the planting arm to the seedling claw tip relative to the connecting line of the eccentric gear box axis, with the connecting line of the planetary carrier axis as the starting edge, counterclockwise as positive, taken as 0 °. L2 is the distance from the axis of planetary gear 4 to the tip of seedling claw, set at 140 mm.
Similarly, the position coordinate equation of P ‘point on the claw tip of reverse side seedling is:
According to the formula, the trajectory of the claw tip of the positive and negative side seedlings relative to the seedling door of the seedling box under the unequal division model is obtained (as shown in the figure).
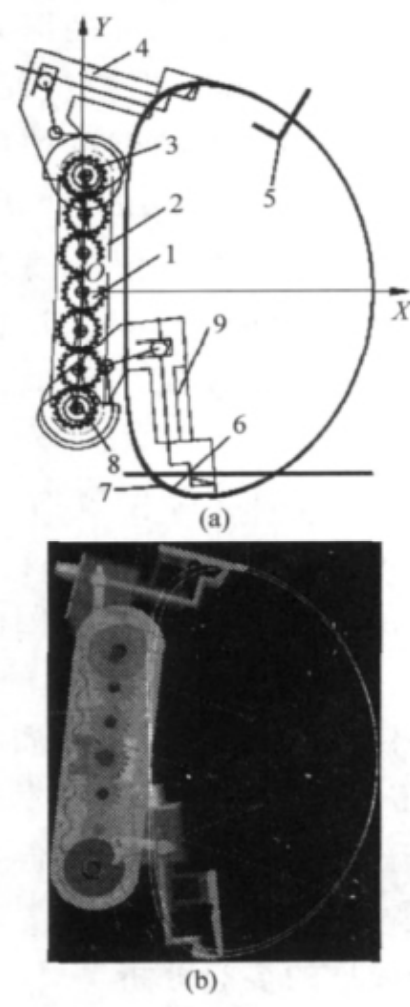
Center wheel; 2. Gear box; 3. Reverse side star wheel; 4. Reverse side planting arm; 5. Seedling box and seedling door; 6. Claw tip trajectory of reverse side seedling; 7. Claw tip trajectory of positive side seedling; 8. Forward and lateral star wheel; 9. Planting arm on the forward side.
Figure a shows the position where the transplanting mechanism of the differential eccentric gear system rotates 92 ° clockwise in the gear box, and the seedling pushing cam of the forward planting arm is about to start pushing seedlings. Because the absolute rotation angles of the positive and negative planetary gears under the unequal division model are not antisymmetric in the first and second half cycles of 180 °, the trajectory of the claw tip of the positive side seedling does not coincide with that of the reverse side seedling. The meshing of each eccentric gear is set as a contact pair by using ADAMS software. The simulation results are shown in Figure B, and the two results are very close. The track deviation is large near the highest and lowest points of the track, and the maximum deviation value is 1.01 mm.
Because the absolute rotation angle of the down star wheel of the bisection model has rotation angle error, and L2 is long, the small rotation angle error of the planet wheel causes a large change in the trajectory position, resulting in a deviation between the seedling claw at the seedling picking position and the seedling pushing mechanism at the seedling pushing position.
In the design, the position of the seedling door of the seedling box is determined according to the relative motion trajectory. If the position of the seedling gate is determined according to the trajectory under the bisection model, when the angle of the eccentric gear box is 289 ° ~ 299 °, the seedling claw of the planting arm on the forward side enters from the seedling gate to the end of seedling picking. At this point, Δφ 34 is 0.248 ° ~ 0.203 °, and the advance change of the seedling claw position determined by the bisection model from the actual position is 0.606 ~ 0.496 mm. When the angle of the eccentric gear box is 109 ° ~ 119 °, the seedling claw of the planting arm on the opposite side enters from the seedling door to the end of seedling picking. At this point, Δφ’ 34 is 0.959 ° ~ 0.903 °, and the advance change of the seedling claw position determined by the bisection model from the actual position is 2.343 ~ 2.206 mm. Although there is a deviation in the seedling taking position, the box moving mechanism continuously moves the seedling box for seedling supply, and the seedling claw can always take the seedlings. In addition, because the trajectory error of seedling picking section is very small, it has little effect on the amount of seedling picking.
In the design, the seedling pushing position is generally taken from 5 ° before the lowest point to the lowest point, so as to ensure that the planting depth is the preset value. If the seedling pushing position is determined according to the trajectory under the bisection model, when the angle of the eccentric gear box is 92 ° ~ 97 °, the seedling claw of the planting arm on the positive side enters the soil and starts to push the seedlings until the end of pushing the seedlings. At this point, Δφ The change of 34 is 0.393 ° ~ 0.404 °, and the advance of the seedling claw position determined by the bisection model from the actual position is 0.965 ~ 0.987 mm. When the rotation angle of the eccentric gear box is 272 ° ~ 277 °, the seedling claw of the planting arm on the opposite side starts to push the seedling to the end. At this point, Δφ’ The change of 34 is 1.035 ° ~ 1.037 °, and the advance of the seedling claw position determined by the bisection model from the actual position is 2.529 ~ 2.534 mm. The transplanting depth of the forward and reverse side seedling claws is less than the preset value, and the track of the reverse side seedling claw is the shallowest. Therefore, in the design, the seedling pushing position shall be determined based on the track of the reverse side seedling claw, so as to determine the installation height of the central axle relative to the ground and the gear setting of the transplanting depth adjustment mechanism. Because the rotation angle of the eccentric gear box corresponding to the lowest point of the trajectory determined by the equal division model and the unequal division model is the same, the installation phase of the seedling pushing cam determined by the seedling pushing position relative to the eccentric gear box remains unchanged.
Seedling picking angle and seedling pushing angle are important indexes to measure the performance of transplanting mechanism and the verticality of transplanting. Here, the seedling taking angle is defined as the included angle between the seedling claw and the seedling direction in the seedling taking section, and the seedling pushing angle is defined as the included angle between the seedling claw and the vertical direction in the seedling pushing section. In this way, the smaller the seedling picking angle, the seedling claw will enter the seedling along the seedling direction, reduce the damage of the seedling claw to the seedling, and the better the seedling separation performance. The smaller the seedling pushing angle, the closer the seedling clamped by the seedling claw to 90 °, and the better the verticality.
Since the positive and negative planetary gears drive the positive and negative planting arms to rotate respectively, the rotation angle error of the positive and negative planetary gears in the seedling taking section is the error of the seedling taking angle, and the rotation angle error of the positive and negative planetary gears in the seedling pushing section is the error of the seedling pushing angle. It can be seen that it is not accurate to use the planetary gear angle under the bisection model to determine the seedling claw attitude. When the inclination angle of the seedling box is adjusted to 60 °, according to the planetary gear angle output of the unequal division model, the change of seedling taking angle in the seedling taking section is 3.630 9 ° ~ 0.3621 °, and the change of seedling pushing angle in the seedling pushing section is 1.107 8 ° ~ – 0.3712 °, indicating that the selection of mechanism parameters is appropriate.