Spiral bevel gears are widely used in aviation high-speed transmission systems because of their good load capacity, smooth transmission and good lubrication. In the gear transmission system, the system power loss can be divided into load related power loss and load independent power loss. The latter is also called spin power loss. The load independent power loss is related to many factors during the system operation, including the viscous dissipation of bearings, the oil stirring loss or wind resistance loss of lubricating oil, and the loss caused by the compression/expansion of lubricating oil or oil gas two-phase flow in the meshing area, The total spin power loss of the gear pair is defined as the sum of the power losses caused by the interaction between each gear and the surrounding environment. When the linear speed of gear teeth exceeds 50 m/s, the high-speed rotating gear teeth will form a strong eddy current, high speed field and centrifugal force field in the fluid domain of the gearbox, and then generate pressure and viscous force on the gear surface, causing a certain loss of wind resistance power. Therefore, for the high-speed spiral bevel gear pair, the impact of wind resistance on the transmission system must be considered.
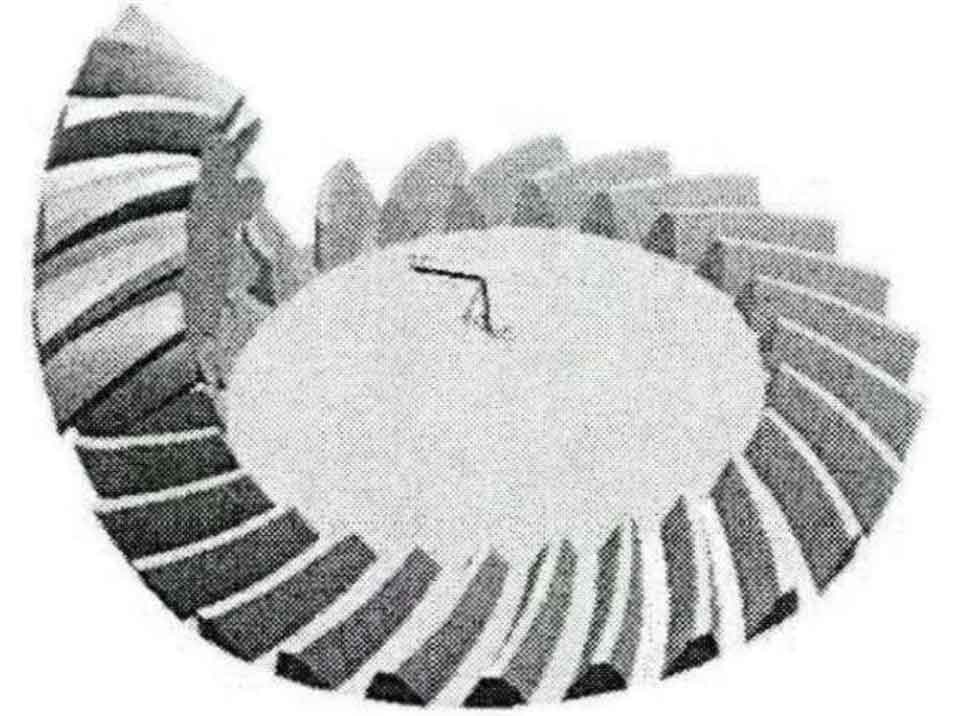
For gear windage power loss, domestic and foreign scholars have done a lot of research in experimental research, simulation analysis and theoretical analysis. Dawson conducted a large number of gear wind resistance experiments using single spur and helical gears rotating in air, and derived empirical formulas to describe the influence of gear geometry, physical properties of fluid domain and gear speed on the system wind resistance power loss; Diab and Ville conducted wind resistance experiments on discs and gears of various shapes and sizes, and then proposed a quasi analytical model prediction based on the fluid flow around the rotating gear and size analysis to describe the wind resistance power loss in the gear pair. Winfree conducted an experimental analysis on the wind resistance power loss of a single spiral bevel gear installed with a wind shield, and studied the wind resistance characteristics of a single spiral bevel gear under different wind shield configurations to optimize the effect of the wind shield on the wind resistance power loss of the gear; Michal Ruzek and Fabrice Ville built a simple test bench to measure the windage power loss of the disk, spur gear pair and helical gear pair under non meshing conditions. In order to avoid the interference of meshing loss, they only considered the influence of air pressure and viscous force on the windage of gear tooth surface and end face.
With the development of computer aided analysis, CFD (Computational Fluid Dynamics) has become an indispensable tool in fluid analysis. The CFD method is used to discretize the numerical solution of nonlinear partial differential equations in fluid analysis. With the powerful computing power of the computer, it can achieve rapid solution under non experimental conditions, Therefore, using CFD simulation tools to calculate gear drag has become an effective means for most scholars to study the mechanism of gear drag. Al Shibl and Simmons et al. [8] used Fluent software to study the windage power loss of a single spur gear when it rotates in air. In order to simplify the calculation, a two-dimensional plane model was established for calculation and solution. The windage power loss of the gear at different speeds was analyzed and compared with the open experimental data, and the windage power loss of the gear fitted with a windshield was analyzed; Rapley and Eastwick et al. [9] conducted CFD simulation analysis on a single spiral bevel gear. The fluid domain was pure air phase. They studied the influence of gear rotation direction and windshield configuration on the wind resistance of spiral bevel gear, and compared it with existing experimental data; Jia established a three-dimensional computational fluid dynamics model of a single straight cylindrical gear reducer, simulated the turbulence model using CFD simulation software, proposed a calculation method for the windage power loss of straight cylindrical gears, analyzed the windage power loss of gears under oil gas two-phase flow, and compared the analysis results of CFD models under different gear parameters; Liang Zuobin, Zhang Maoqiang and others in China simulated the windage loss of a single spiral bevel gear in an aeroengine, set a periodic boundary to simplify the calculation when using a three-dimensional model, studied the influence of different deflectors on the windage loss of spiral bevel gears, and obtained the optimized deflector layout; Bao Heyun and Wang Chunlei set up an analysis model for the windage loss of planetary gears in GTF engines, analyzed the influence of the internal structure of the gearbox on the windage loss, and proposed measures to optimize the windage loss; Zhao Ning and Jia Qingjian [13] used CFD technology to conduct numerical simulation analysis on the fluid domain around the spur gear and its turbulence model, and obtained the calculation method for the windage power loss of the face gear.
To sum up, no matter in terms of experimental research or CFD numerical simulation, most of the research on gear windage is focused on spur gears in a single non meshing case. For spiral bevel gears, only a few scholars have studied their single wheel windage effect, and almost no research on meshing double wheels has been involved. One of the reasons is that the experimental design of the windage loss of the meshing gear is relatively complex, and there are many factors affecting the windage loss, so it is difficult to accurately calculate the windage power loss of the gear pair; Second, in order to simplify the model and improve the calculation efficiency, scholars in the past conducted two-dimensional plane modeling of the simulation model. For the meshing spiral bevel gear pair, three-dimensional modeling must be used to accurately express the calculation domain. Moreover, the calculation of the meshing gear pair is different from the single wheel calculation. The former must use the transient analysis model, and the latter can use the mature multi reference system steady state model. At this time, the calculation amount is greatly increased, The traditional computer can hardly complete the calculation. Even the workstation with high computing performance needs a long time to complete the calculation of a model. In this paper, the CFD numerical analysis method is adopted, the Fluent solution software is used, and the powerful parallel computing ability of supercomputer is used to carry out the single-phase flow simulation calculation for the wind resistance loss of the aviation spiral bevel gear pair. The analysis model adopts UG (Unigraphics NX) software for three-dimensional modeling, and RNG (Renovation Group) k- ε Turbulence model. Because the analysis model of the meshing spiral bevel gear pair is different at each time, the transient analysis method is adopted, and the dynamic grid technology is used to simulate the problem that the flow field shape changes with time due to boundary movement. Considering the optimization of the wind shield on the wind resistance power loss of the spiral bevel gear, a spiral bevel gear wind shield structure is proposed, At the same time, study the wind resistance loss of spiral bevel gear pairs without and with wind shield, as well as the corresponding flow field pressure, velocity, turbulent kinetic energy and gear tooth surface viscosity. For spiral bevel gears with wind shield, analyze the impact of different wind shield configurations on the wind resistance loss of spiral bevel gear pairs, and finally obtain the optimal wind shield configuration.