The established three-dimensional assembly model of super reduction ratio hypoid gear is imported into the finite element software Ansys Workbench. According to the meshing transmission relationship of super reduction ratio hypoid gear, the motion of super reduction ratio hypoid gear is constrained by the rotation pair and contact pair. The rotational speed of the active super reduction ratio hypoid gear is 1000 r/min, and the reverse torque of the driven super reduction ratio hypoid gear is 500 N · m.
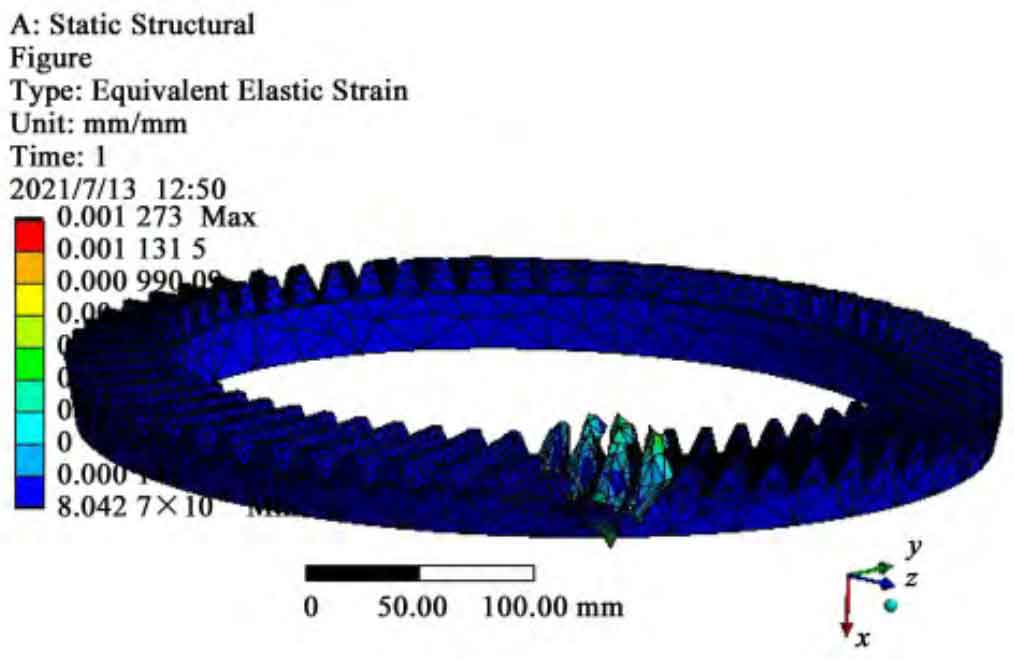
According to the established finite element simulation model of hypoid gear with super reduction ratio, the fracture diagram and equivalent stress distribution of gear teeth are simulated by using the finite element simulation software Ansys Workbench, as shown in Figure 1 and Figure 2.
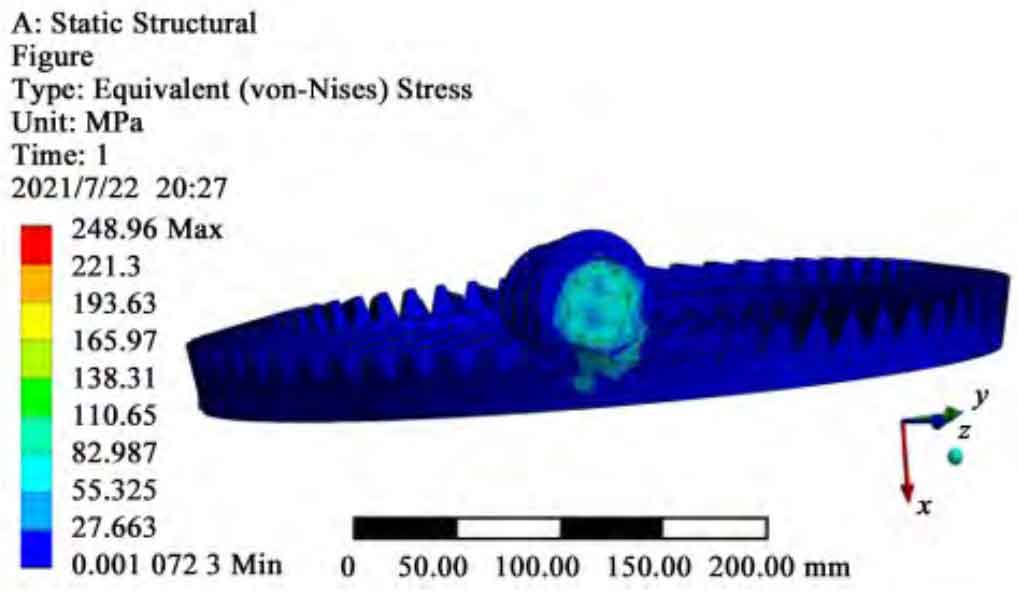
It can be seen from Figure 2 that under the condition of ensuring the safety of hypoid gears and qualified design, when the driving wheel is set at a speed of 1000 r/min and the driven wheel is set at a reverse torque of 500 N · m, the maximum equivalent stress of meshing teeth of hypoid gears with super reduction ratio is mainly distributed on and near the contact surface of big and small gears, with a safety factor of 1 292/248. 96 ≈ 5. 189>2, It can fully meet the static and dynamic requirements of the super reduction ratio hypoid gear system.
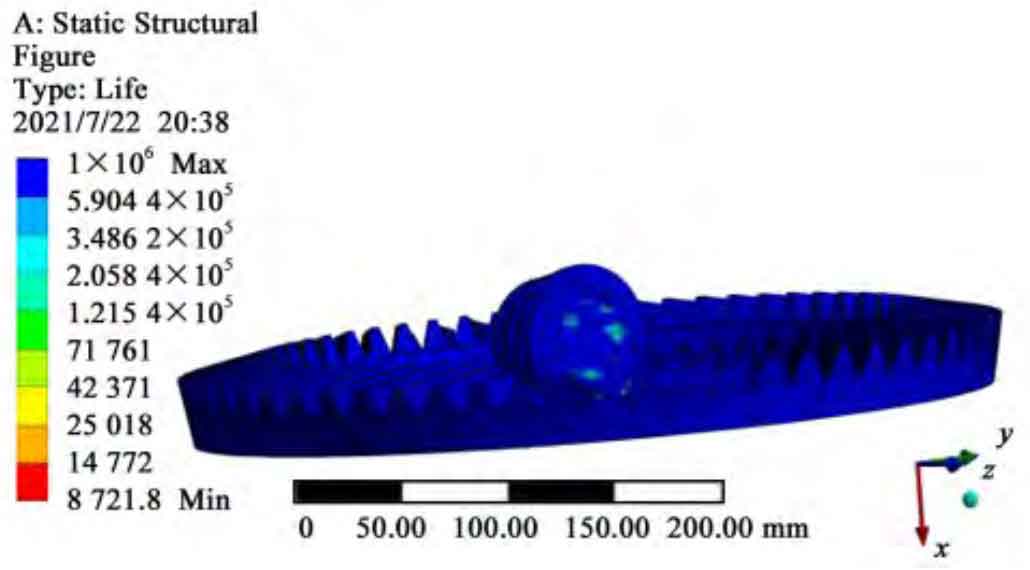
Insert the Fatigue tool through the finite element software Ansys Workbench, and then select the options of Life, Damage and Safety Factor. Figures 3 to 5 are obtained through simulation to analyze whether the hypoid gear is safe and the design is qualified.
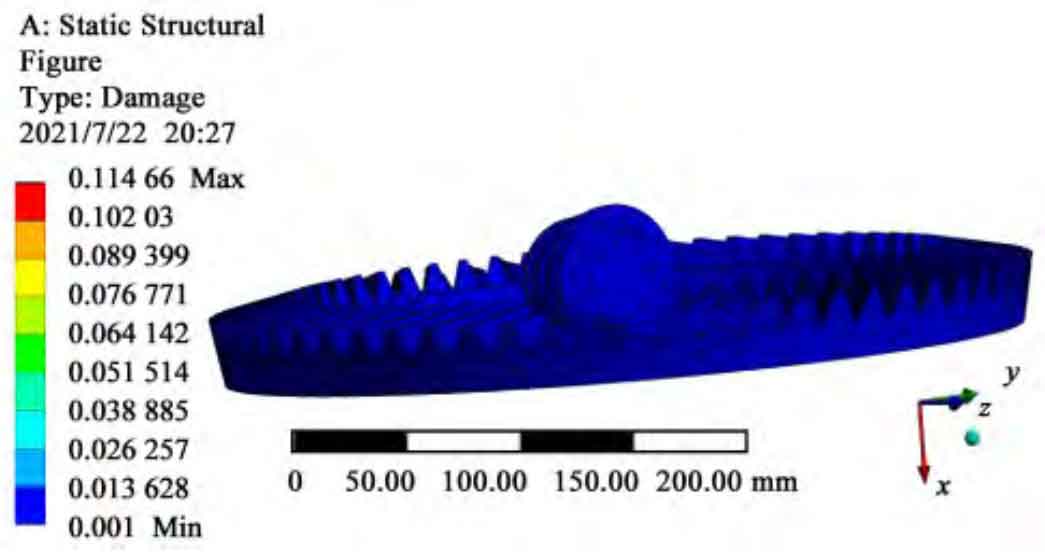
It can be seen from Figure 3 that the minimum fatigue life of hypoid gear with super reduction ratio is 8721. 8 cycles.
In Damage, you can check the cumulative fatigue damage coefficient of hypoid gears. The maximum cumulative fatigue damage coefficient is 0.11466<1 (Figure 4), which proves that the design is qualified.
It can be seen from Figure 5 that the fatigue safety factor is 2.102 2>1, which indicates that the hypoid gear is safe.
Under the condition that the hypoid gear is safe and the design is qualified, the fatigue characteristics of the hypoid gear are analyzed. When the initial reverse torque is 500 N · m (Fig. 3) and the reverse torque is increased by 50 N · m in turn, the change curve is shown in Fig. 6 after sorting out the data that the fatigue life of the hypoid gear changes with the torque.
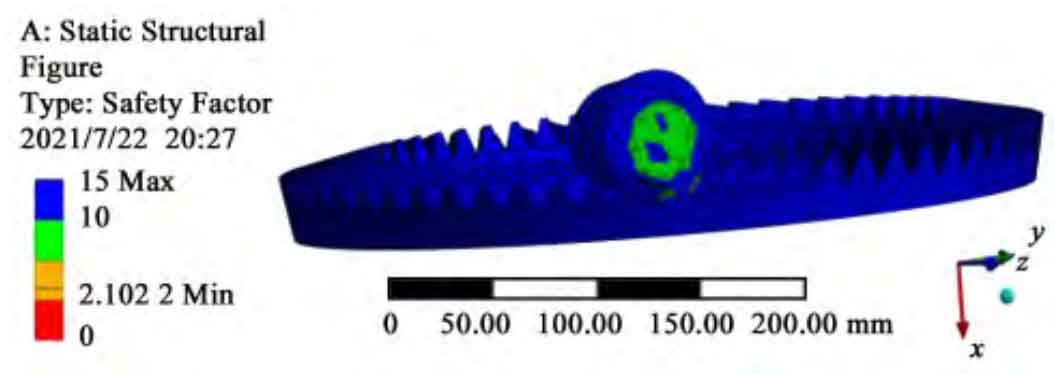
It can be seen from Figure 6 that with the increase of reverse torque, the damage of hypoid gear is greater and the minimum fatigue life is smaller.
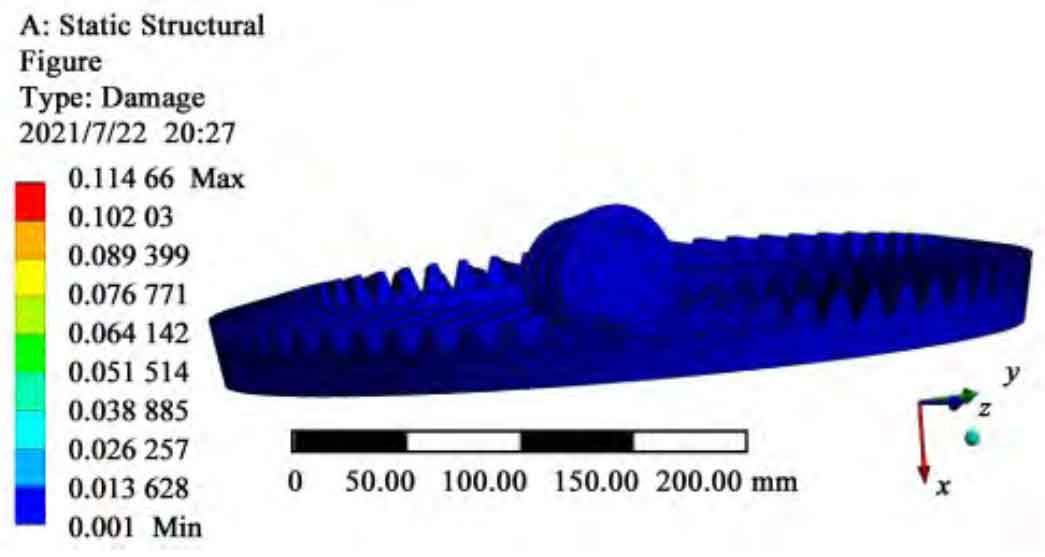
The life of hypoid gears is reduced, which may lead to load concentration due to too large reverse torque. Therefore, in practical application, it should be ensured that there is enough lubricating fluid between hypoid gears, and when the hypoid gears are damaged, it needs to be handled at the first time.
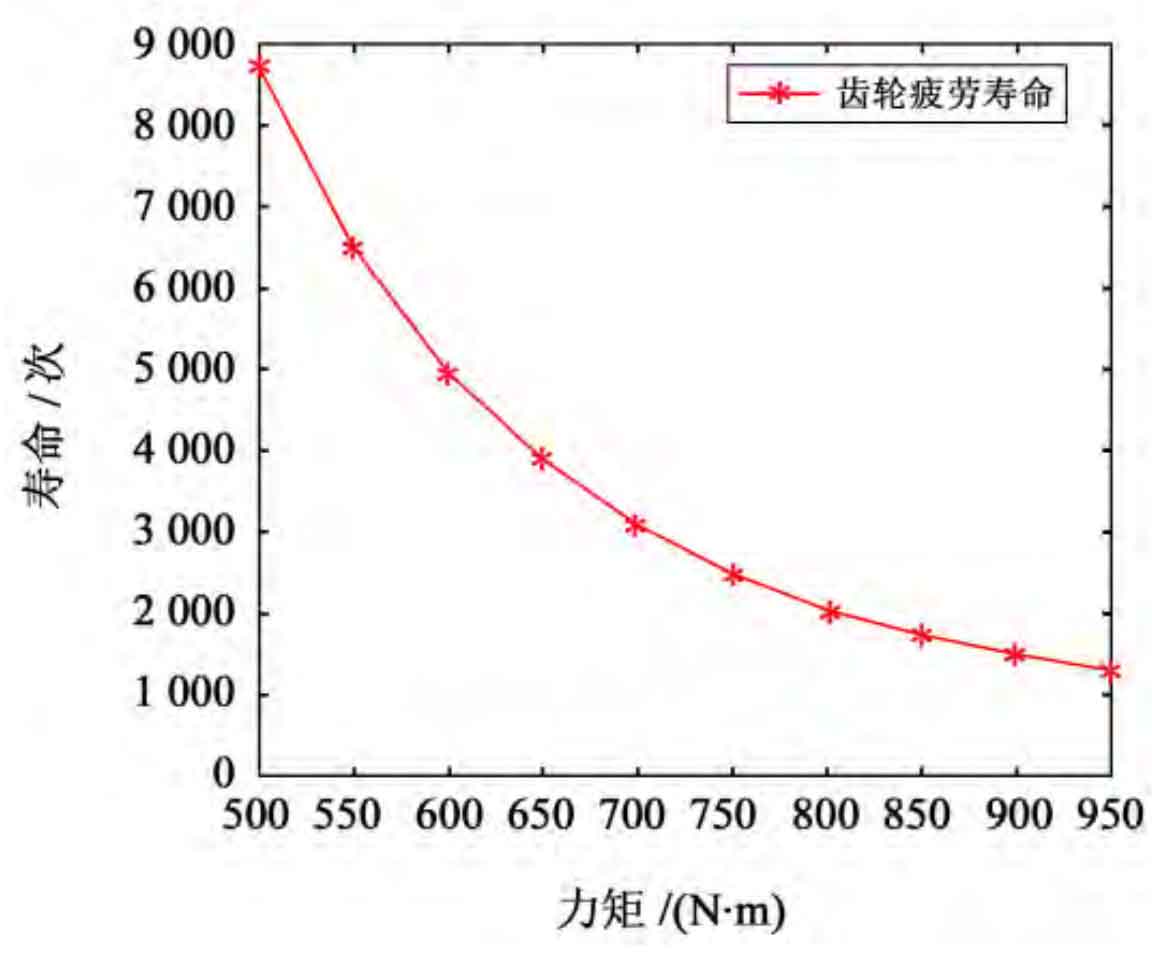
Under the condition that the hypoid gear is safe and the design is qualified, the fatigue characteristics of the hypoid gear are analyzed. When the initial speed of the hypoid gear is 1 000 r/min and the speed is increased by 100 r/min in turn, the data that the fatigue life of the hypoid gear changes with the speed of the hypoid gear are sorted out, and the change curve is shown in Figure 7.
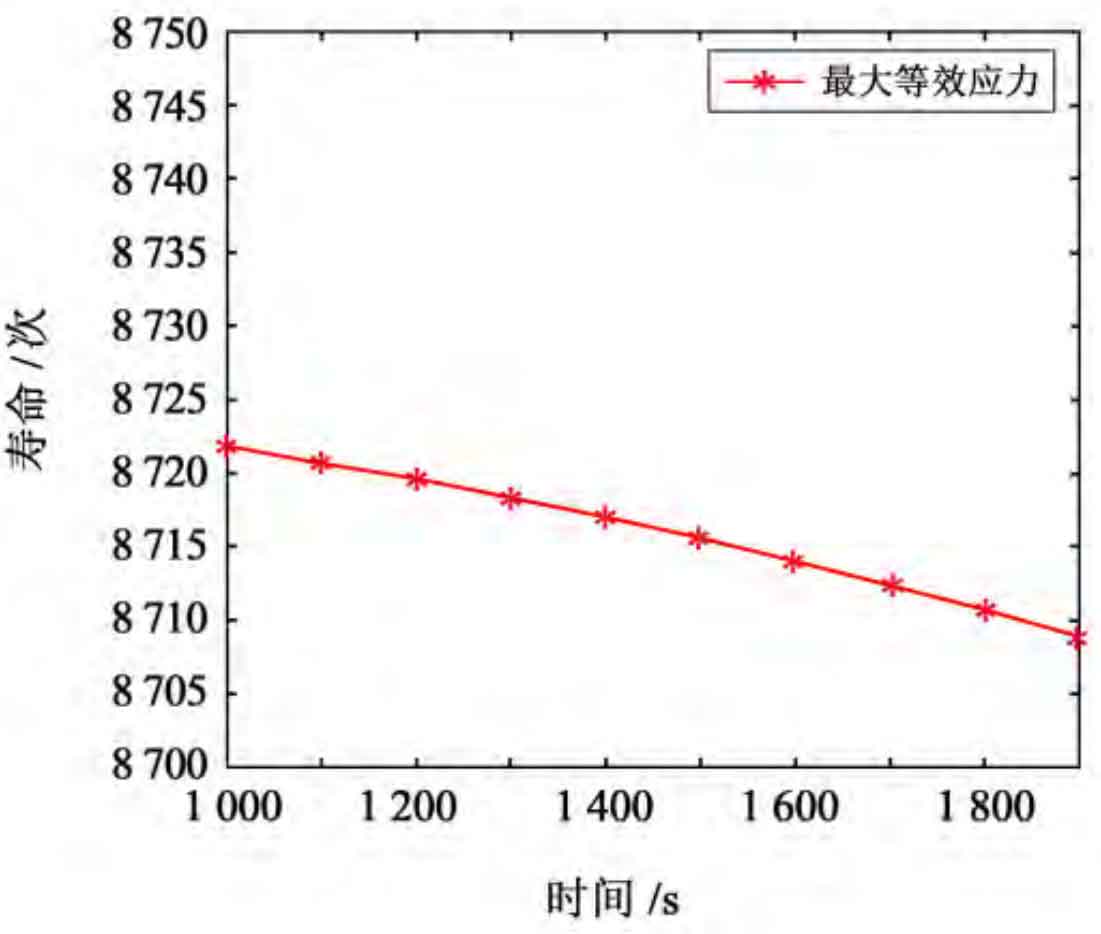
It can be seen from Figure 7 that with the increasing speed, the damage of hypoid gears will increase slightly and the minimum fatigue life will decrease slightly. From this, it can be judged that the influence of hypoid gear speed on gear life is not great.
The decrease in the service life of hypoid gears may be due to the overheating of the gear tooth surface caused by the increased speed, which leads to tooth surface scuffing.
When the other conditions remain unchanged, the tooth root of the hypoid gear shall be aligned for processing, and the fatigue life of the hypoid gear with super reduction ratio and root fillet of 2.0 mm shall be obtained, as shown in Figure 8.
It can be seen from Figure 8 that, compared with Figure 3, the minimum life of hypoid gears with super reduction ratio after the tooth root is machined with the tip fillet has been improved.
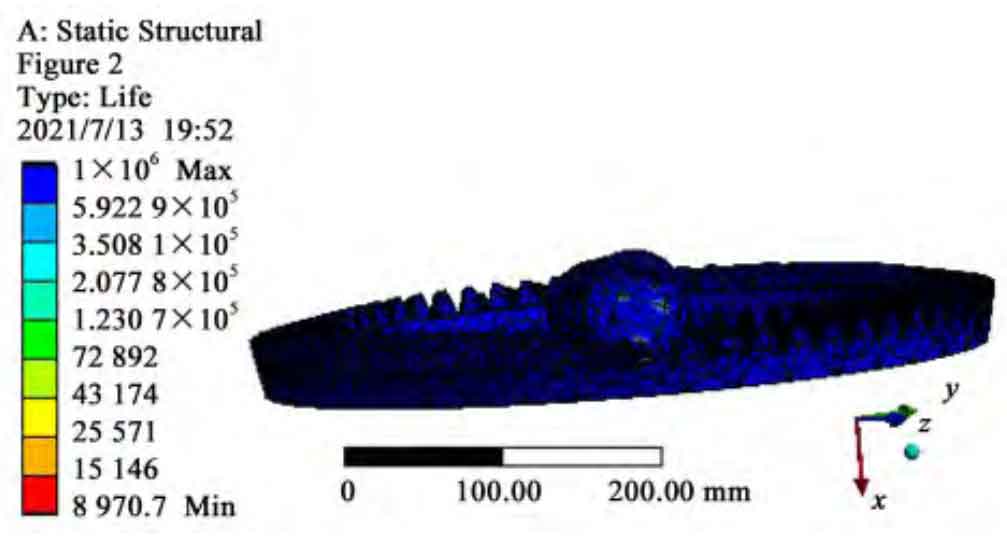
The reason why the minimum life of hypoid gears has been improved may be that the root fillets obtained by machining the root fillets at the tool tip can effectively reduce the stress concentration between gears.
Therefore, when designing, the cutter tip fillet can be properly aligned with the tooth root of the hyperboloid gear for processing to improve the strength of the big wheel.