Taking the worn double circular arc gear shaft of the pumping unit reducer as the object, the gear design is carried out according to the GB/T 12759-1991 standard. Clean the gear shaft parts and conduct 3D reverse measurement. The 3D laser scanner used is HandySCAN 300TM 3D, as shown in Figure 1, and the performance parameters are shown in the table.
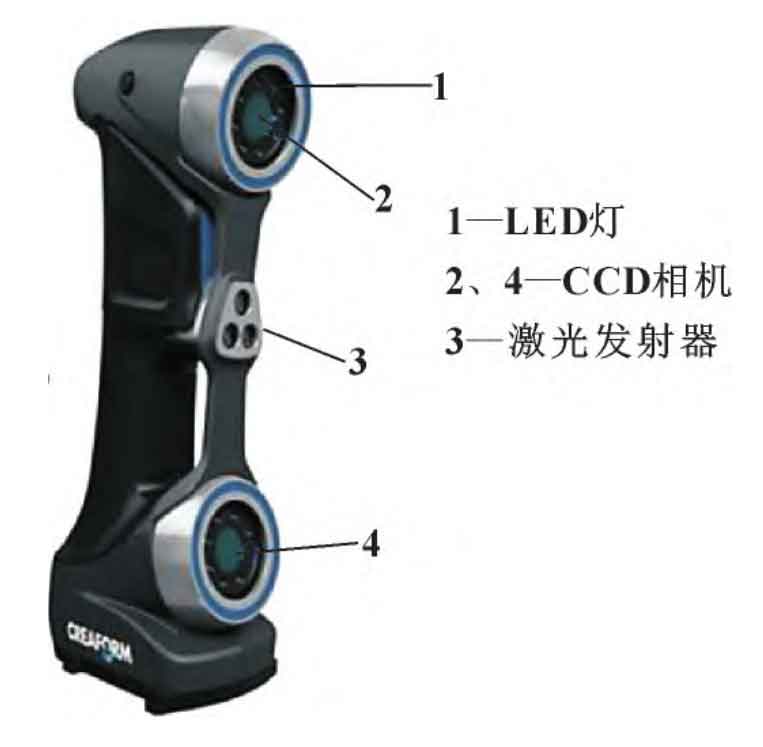
Before scanning, the workpiece to be tested shall be pasted with circular positioning marks, as shown in Fig. 2 (a). When pasting round targets on the workpiece surface, try to ensure that they are not in a straight line. After the preparation is completed, the upper computer software VXelements is used to assist data acquisition, and the 3D model of the scanned workpiece is shown in Figure 2 (b).
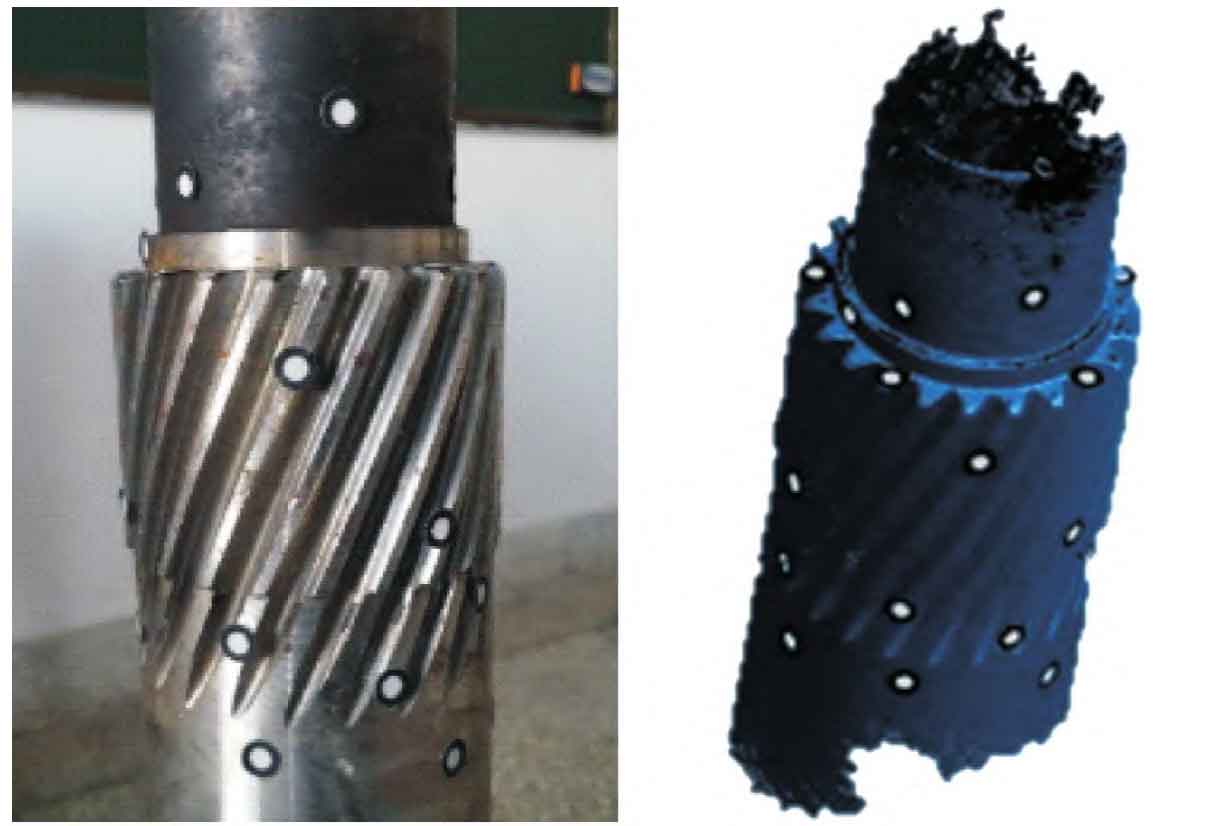
Import the triangular patch file obtained by surface scanning into reverse engineering software to complete the establishment of workpiece coordinate system. Simplify the model patch to reduce the amount of data. Use the repair wizard to repair the model, mainly to reduce voids, redundant unit faces and overlapping unit faces. The model that meets the measurement standard can be obtained after the hole filling command is used to repair the damaged cavity.
Performance index | Parameter |
Sampling rate/(times · s-1) | 205 000 |
Scanning accuracy/mm | 0.04 |
Volume accuracy/mm | 0.02 |
Component size range/m | 0.1-4 |
Laser Category | II (human eye safety) |
Upper computer software | VXelements |