The gear rack with large module and heavy load is not suitable for the conventional hobbing and slotting processing method. For small gears, the milling process is usually designed according to the tooth profile, and for racks, CNC cutting or casting is adopted according to the tooth profile. In order to facilitate manufacturing, the tooth profile of the push gear on the large mining equipment used to be composed of three sections of circular arcs that were approximate to the involute. Below the base circle was the tooth root circular arc, between the dividing circle and the tooth root circular arc was one section of circular arc, and above the dividing circle was another section of circular arc. In the process of use, the transmission error is large, causing vibration and serious wear. Some teeth are broken due to unreasonable design of tooth root arc. How to optimize the tooth profile design, the key to solve the problem is the gear parameters.
Many people have studied how to improve the bending strength of gears and reduce the root stress. The single arc is more beneficial to reduce the tooth root stress than the double arc. However, the existing problem is that increasing the radius of tooth root arc is easy to cause meshing interference. The solution to this problem is to increase the radius of tooth root arc as much as possible while ensuring the effective involute. The tooth root arc radius is finally determined by the following factors.
1. Tooth tip thickness
For open gear, if the tooth top is too thin, it is easier to wear. It is recommended that the gear top thickness S ≥ 0.4m. It is applicable to heavy-duty gear and rack transmission under fatigue load. For heavy-duty gear and rack transmission under static load on drilling platforms, S ≥ 0.15 m. The push mechanism XP2300 and XP2800 of foreign large excavators push the pinion tooth top to 0.41m and 0.42m respectively, and the tooth top thickness of the climbing pinion of the 300 ft and 400 ft jack up drilling platforms of foreign famous NOV lifting devices is 0.14m and 0.15m respectively.
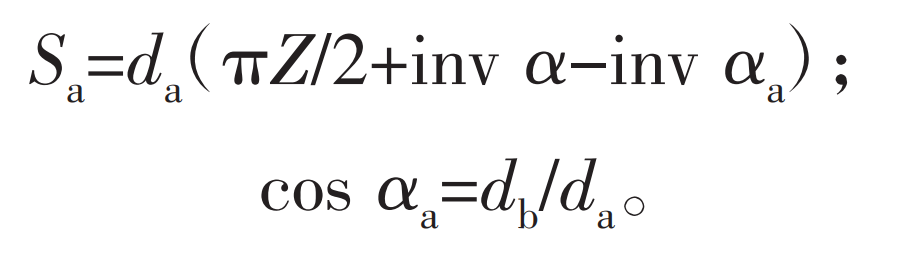
Where: da is the diameter of the addendum circle; α A is the addendum pressure angle; M is the modulus.
2. Overlap factor
For heavy-duty rack and pinion drives subject to fatigue load, the recommended overlap factor ε≥ 1.2. If the contact ratio is small, the meshing impact is large, which is unfavorable to the gear strength. For heavy load rack and pinion drive mainly bearing static load on drilling platform, ε≥ 1.05 is enough.
Because the pressure angle of heavy-duty gear rack mainly bearing static load is usually greater than 25 °, the contact ratio is large, and the tooth tip almost becomes sharp, which is easy to cause plastic deformation.

Where, ha2 ‘is the effective addendum of the rack above the engagement point (as shown in Figure 1).
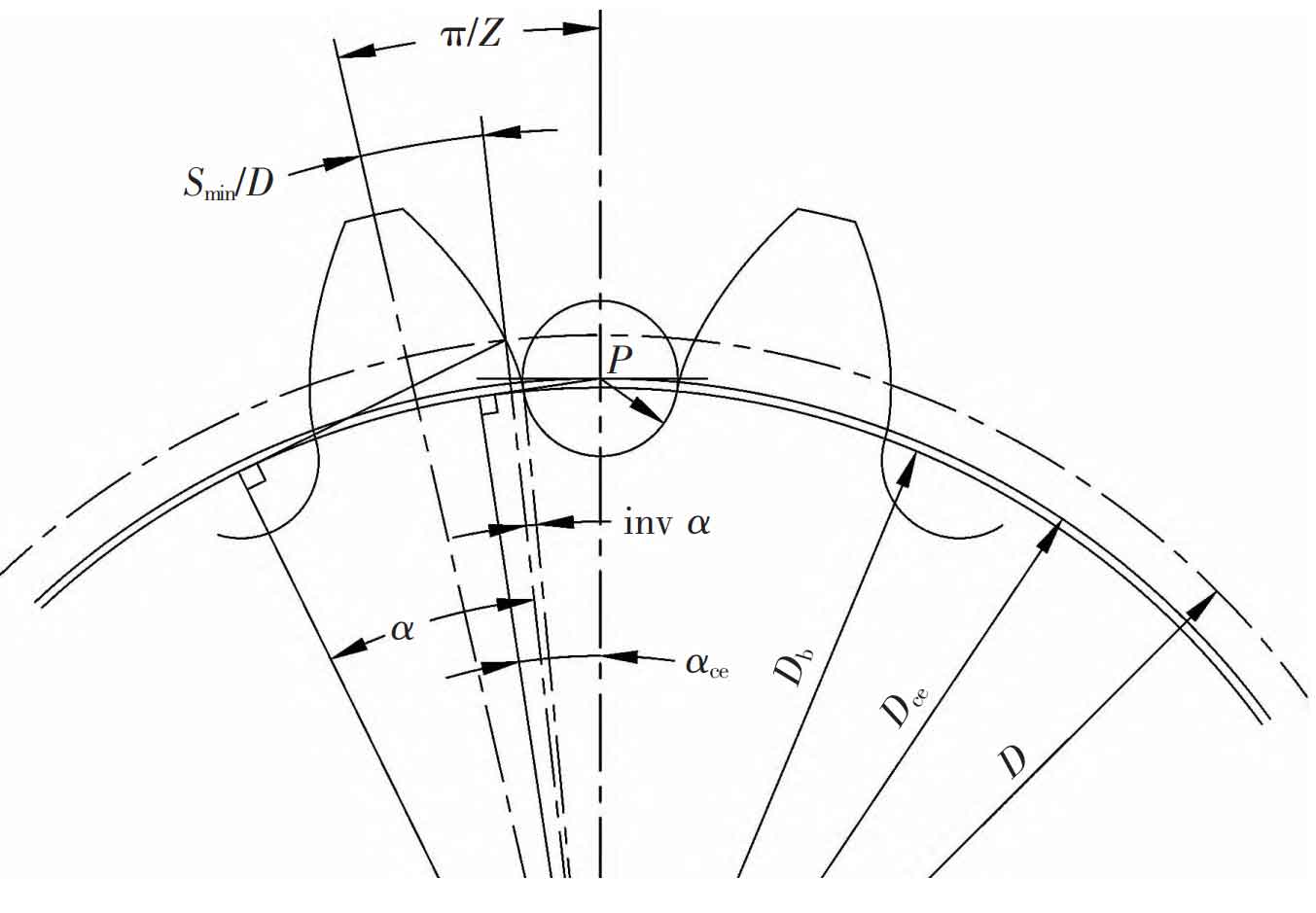
According to the working conditions, the addendum circle diameter da and the addendum pressure angle can be calculated by using the formula. At the same time, the formula is satisfied. With the addendum circle diameter, the selection of the modification coefficient and the addendum height coefficient of the gear should be considered. If the short tooth is used for large modification, the gear tooth thickness increases, which means that the mesh point rack tooth thickness decreases and the gear strength increases. The modification coefficient and the gear positive modification should be selected according to the strength principle of heavy-duty rack and gear.
3. Side clearance
In consideration of the manufacturing error of the open heavy load gear rack tooth profile, the error of the installation distance, the accumulated error of the circumferential pitch, and the friction and thermal expansion of the tooth surface during transmission, the backlash is generally 0.12~0.15 times the modulus. The tooth side clearance is reserved by reducing the tooth thickness of the heavy load gear rack. The thickness of the rack root is thick.
4. Gear root fillet
After the above parameters are determined, the root fillet radius is finally designed.
Single circular arc is adopted for the fillet of the gear root. Compared with the gear, the width of the dangerous section of the rack is larger than that of the gear, and the number of loading cycles is less. It can be calculated according to the strength. Double circular arc is adopted for the root of the rack, which can reduce the height of the root of the rack, thicken the rack base, and prevent the rack from deformation. According to the need to select the radius of the rack root arc, here is mainly for the research of the gear root fillet. For heavy load gear rack transmission, the lowest meshing point of the gear is basically on the base circle, usually 2~3 mm larger than the base circle, provided that the overlap coefficient and the tooth thickness of the tooth crest arc are guaranteed. The tangent point between the tooth root single arc and the involute is set as the lowest meshing point. Root fillet radius r ρ The calculation is as follows:

Where: r ρ Is the root fillet radius, mm; Db is the diameter of the base circle, mm; α Ce is the pressure angle of the tangent point between the tooth root arc and the involute; Smin is the actual tooth thickness of the indexing circle, mm; α Is the pressure angle of the dividing circle; Dce is the diameter of the tangent point between the tooth root arc and the involute, Dce=Db+(2~3 mm).
5. Rack profile
According to the meshing characteristics of heavy-duty gear racks, no matter whether the installation distance is standard or not, the node is always on the gear reference circle. According to Figure 2, the effective addendum h a2e of the rack is calculated as follows:
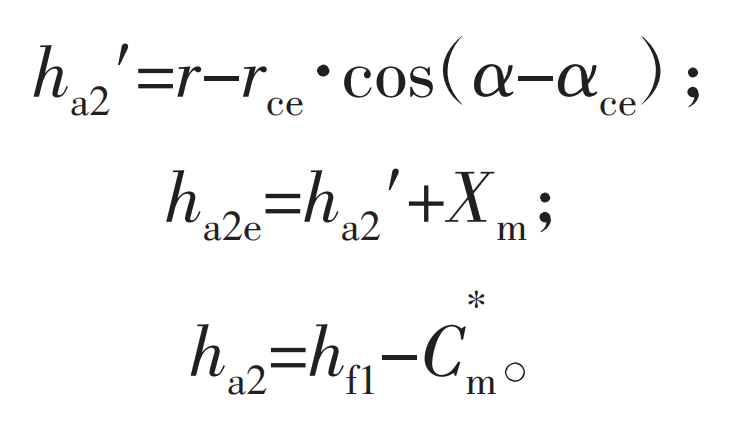
Where, ha2 is the rack tooth height, mm; Ha2e is the effective tooth height of the rack, mm; Ha2 ‘is the tooth height of the rack engagement point, mm; Cm * is the top clearance (to ensure that the open gear pair has enough lubricating oil, the top clearance is 10~12 mm, and the top clearance is used to store lubricating oil to lubricate the tooth profile).
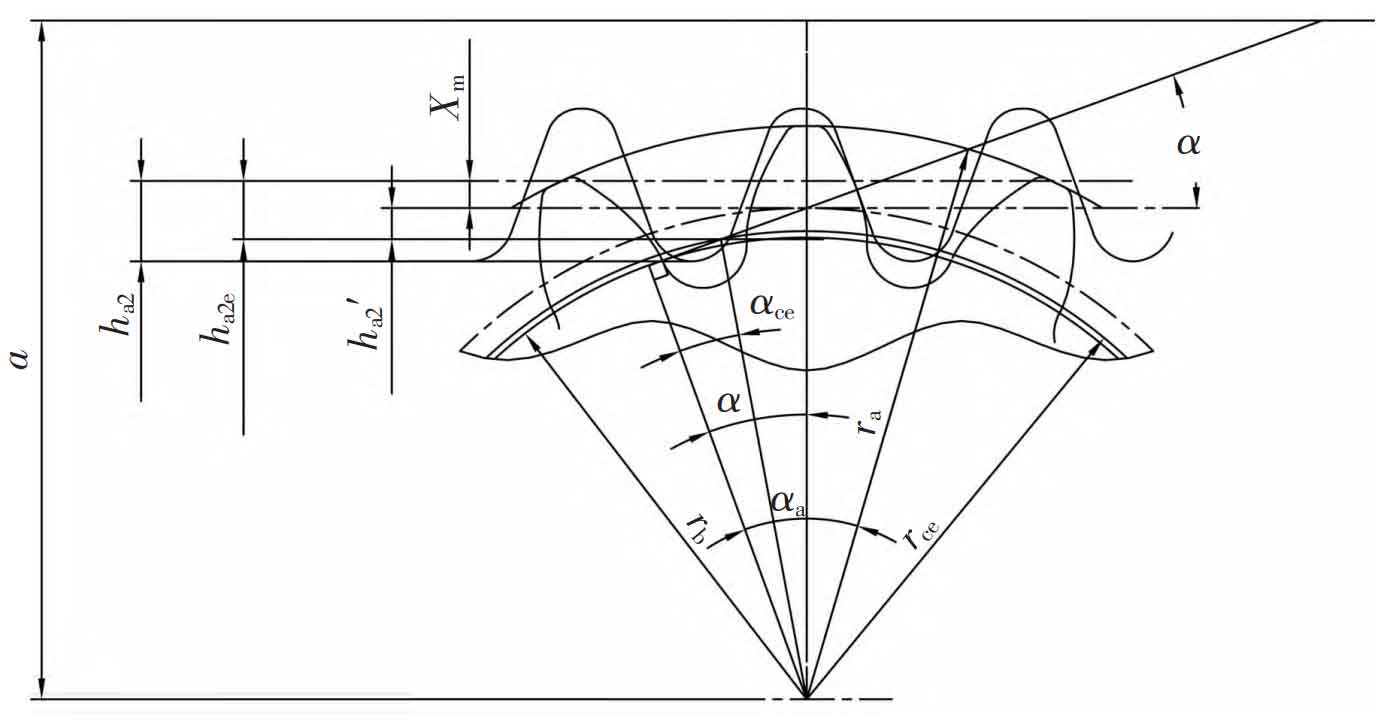