Hobbing method for machining spiral bevel gears: The traditional Gleason mechanical structure spiral bevel gear milling machine uses a milling cutter disc mounted on a shaking table to rotate and mill the teeth. When the workpiece and shaking table mechanism rotate around their respective axes at a certain transmission ratio, the cutter disc will cut a tooth groove on the workpiece wheel blank. The cutting process of a gear is like the meshing process of an aligned hypoid gear.
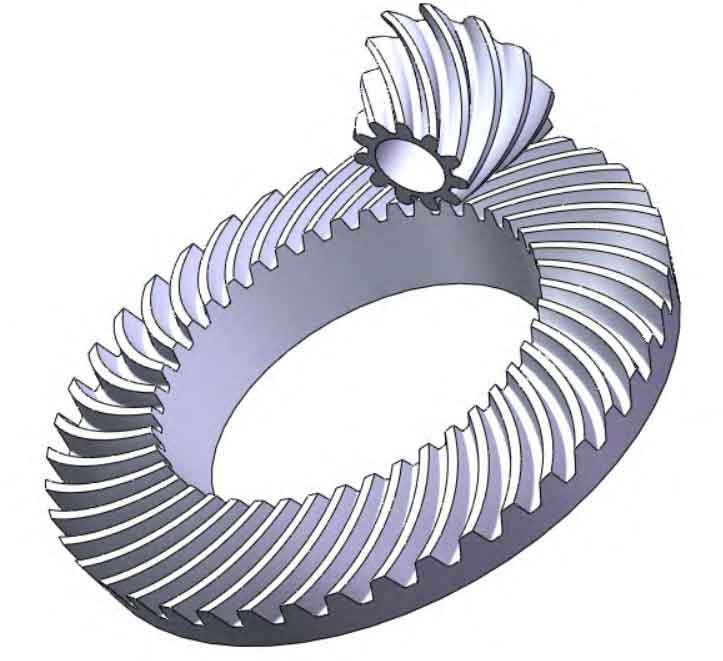
Semihobbing method for machining spiral bevel gears: Semihobbing method for machining spiral bevel gears is an effective and efficient method for mass production of spiral bevel gears with transmission ratio ≥ 3 and large pitch angle ≥ 70 °. The cutting method is adopted for rough machining of the big wheel. The big wheel is fixed, and the tool is cut in. After reaching the full tooth depth, it quickly exits the tooth slot. After indexing, another tooth slot is processed until all the tooth slots are processed. The cutting is completed by a special rough cutting machine with a three sided milling cutter. The finishing of the big wheel is completed by a special round puller and a round broach disc for the big wheel. The circular broach cutter head has a notch. The cutter head rotates to process a tooth groove, and is indexed at the notch of the cutter head. The cutter head rotates at a constant speed until the finish machining of all the tooth grooves is completed. The small wheel rough machining adopts the hobbing method, and the double-sided cutter head completes the rough cutting of the two sides of the gear groove at one time. Pinion finishing is performed by using a machine tool with a 30 ° spindle tilt mechanism or a modification mechanism to process the concave and convex sides of the pinion using a hobbing method and correct the tooth surface. The cutter head is a single sided cutter head with concave and convex sides machined separately. The machine tool is equipped with a tool setting device to ensure uniform tooth cutting allowance. This machining method has been widely used in the production of medium modulus spiral bevel gears and hyperbolic gears at home and abroad. For example, spiral bevel gears and hyperbolic gears for automobiles. This processing method greatly shortens the cutting time of the large wheel.