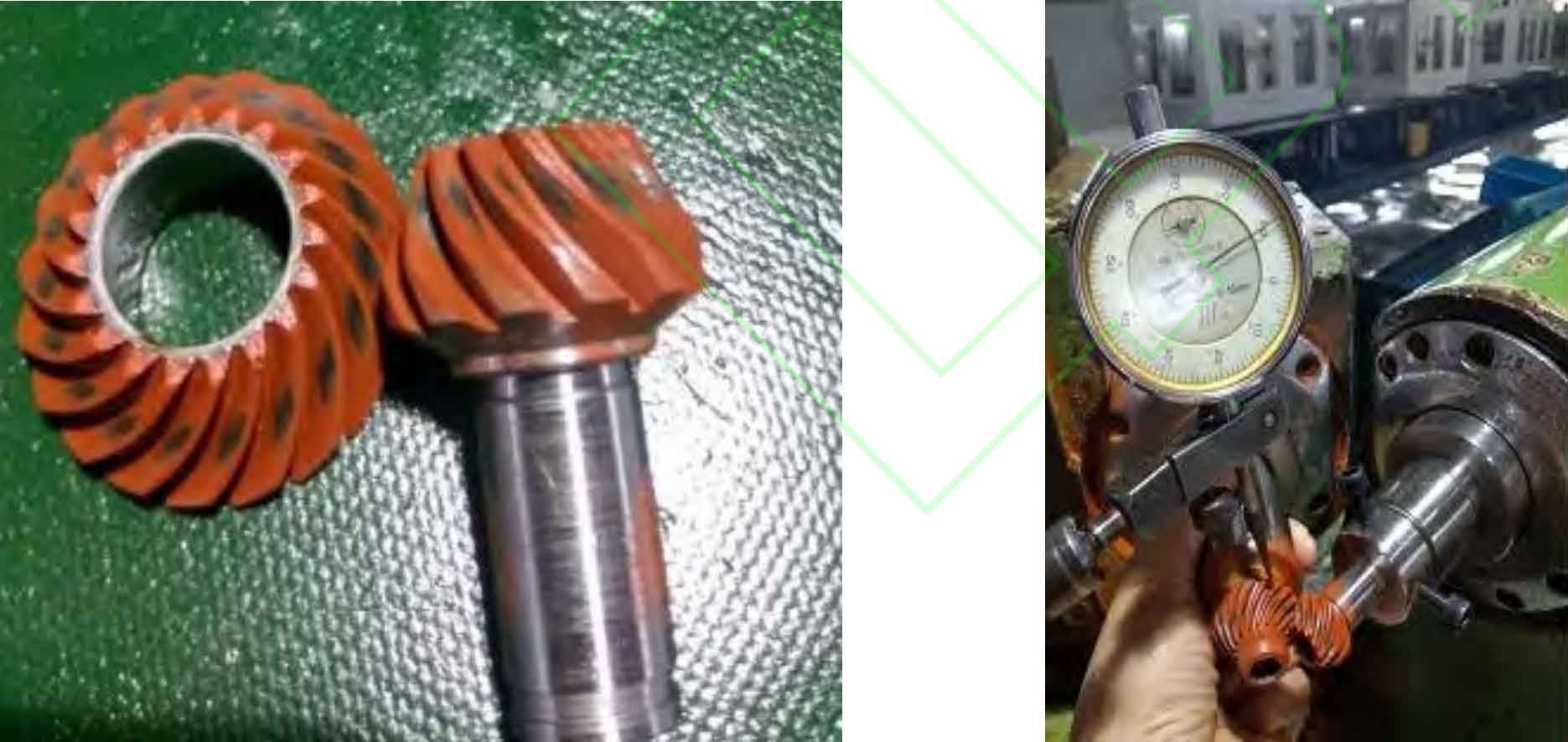
The semi hobbing method for small module spiral bevel gears is feasible. Cutting speed can be improved if coating can be applied to the tool or if the blade type tool is made of cemented carbide. Cutting time for wheel and pinion can be further reduced, and the promotion of this processing method will definitely achieve effective results. The specific conclusions are as follows:
Improvement of the hobbing method: The wheel rough machining adopts the cutting method. The wheel is fixed and the cutter is cut in. After reaching the full tooth depth, the cutter quickly exits the tooth groove. After indexing, another tooth groove is processed until all the tooth grooves are processed. The cutting is completed by a special rough cutting machine with a three-sided milling cutter. The finishing of the wheel is completed by a special round puller and a round broach disc for the wheel. The circular broach cutter head has a notch. The cutter head rotates to process a tooth groove, and is indexed at the notch of the cutter head. The cutter head rotates at a constant speed until the finish machining of all the tooth grooves is completed. The pinion rough machining adopts the hobbing method, and the double-sided cutter head completes the rough cutting of the two sides of the gear groove at one time. The finishing of the spiral bevel gear pinion is performed by using a machine tool with a 30 ° spindle tilt mechanism or a modification mechanism to process the concave and convex sides of the pinion using a hobbing method and correct the tooth surface. The cutter head is a single sided cutter head with concave and convex sides machined separately. The machine tool is equipped with a tool setting device to ensure uniform tooth cutting allowance. This machining method has been widely used at home and abroad in the production of medium modulus spiral bevel gears and hyperbolic gears, greatly reducing the cutting time of wheels.
Improvement in machining efficiency: the cutting time of the hobbing method has been reduced from the set 6 seconds/tooth to about 4.2 seconds/tooth for half hobbing, and the cutting efficiency has been improved by 30%. The semi hobbing method will help to improve the machining efficiency of small module spiral bevel gears, improve the meshing quality of the tooth surface, and reduce production energy consumption. It is of great significance for guiding practical production. The tooth measurement clearance is 0.05-0.9, meeting the standard requirements of 0.1-0.12. The runout of the two teeth is 0.01, meeting the requirements of ≤ 0.015. The runout of the gear ring is 0.034, meeting the requirements of ≤ 0.05. The contact area comparison standard and physical drawing meet the requirements. The comprehensive indicators meet the requirements.