Spiral bevel gears are integral components in many mechanical systems, facilitating smooth power transmission at varying angles. Their unique geometry, with their teeth cut into a spiral shape, helps in reducing noise and vibration, leading to efficient operation. However, understanding the dynamics of spiral bevel gears, how they operate and interact with other components, can be complex due to the intricate nature of their design. This article will explore the dynamics of spiral bevel gears, including their design, function, and application in various industries.
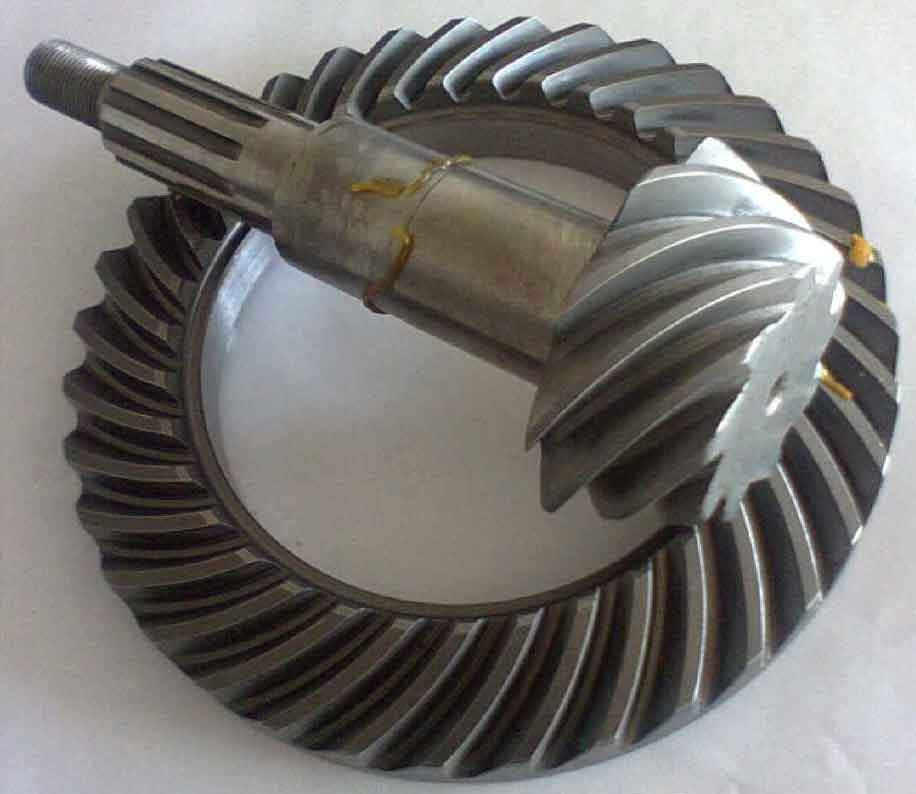
Design of Spiral Bevel Gears:
Spiral bevel gears are designed with teeth that are obliquely arranged in a spiral pattern. This unique design allows for gradual contact between the teeth of two engaging gears, which in turn results in smoother and quieter operation compared to other types of gears. The tooth contact in spiral bevel gears starts at one end of the gear and spreads across the whole tooth, creating a more efficient and effective transmission of power.
Functionality of Spiral Bevel Gears:
Spiral bevel gears are primarily used in mechanical systems to transmit power between two shafts that intersect at an angle, typically 90 degrees. These gears are usually mounted on shafts that are perpendicular to each other and are commonly found in applications that require power to be transmitted smoothly, quietly, and efficiently.
Industries Using Spiral Bevel Gears:
Spiral bevel gears are used across a wide range of industries due to their efficiency and the smooth, quiet operation they provide. Here are a few notable applications:
- Automotive: Spiral bevel gears are crucial components in vehicles, where they are commonly used in the differential, transmitting power from the engine to the wheels at different speeds while the vehicle is turning.
- Aviation: These gears are often used in helicopter rotor drives, where they help to transfer power from the engine to the rotors.
- Industrial Machinery: In machines that require power transmission at right angles, spiral bevel gears are commonly used. Examples include milling machines, printing presses, and power plants.
- Marine: In boats and ships, spiral bevel gears are used in propulsion systems to transfer power from the engine to the propellers.
Understanding Gear Dynamics:
The dynamics of spiral bevel gears are influenced by a number of factors, including load, speed, material properties, and the accuracy of their manufacturing process. Under load, the gear teeth deform slightly, which can affect the distribution of load across the teeth and influence the gear’s efficiency and lifespan. Similarly, changes in operational speed can affect the vibration characteristics and noise generation of the gear system.
In order to optimize the performance of a spiral bevel gear system, it’s necessary to understand these dynamics and how they interact. This often involves complex mathematical modelling and physical testing to accurately predict the performance of the gear under different operating conditions.
Understanding the dynamics of spiral bevel gears is key to their successful application in various industries. With their unique design and efficient operation, these gears play a crucial role in power transmission, impacting the performance and efficiency of many mechanical systems. As technology advances, further research into the dynamics of spiral bevel gears is likely to lead to improved designs and applications, further enhancing their effectiveness in power transmission.