Spiral bevel gears have been at the forefront of power transmission for centuries, and they continue to be indispensable in modern machinery. These gears have evolved significantly over time, in response to changing needs and technological advancements. This article aims to track the evolution of spiral bevel gears, marking the milestones and developments that have led to their current design and application.
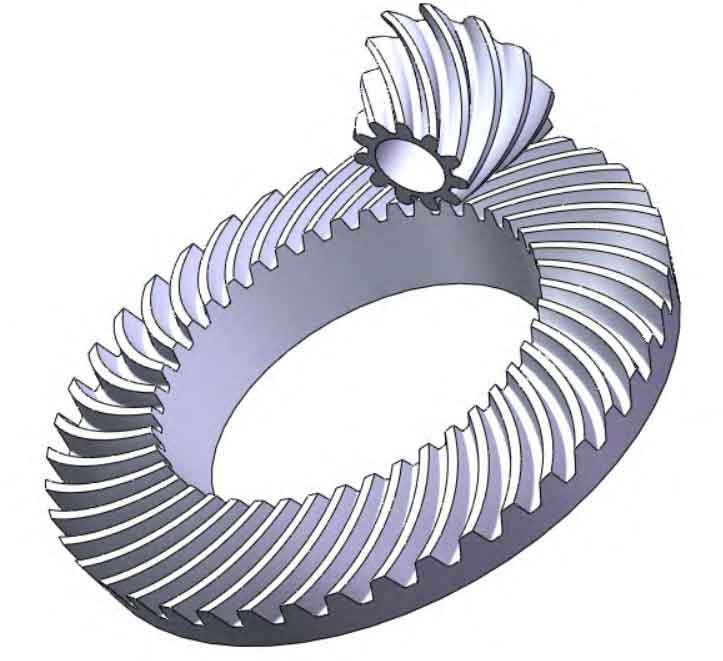
Early Beginnings:
The concept of gears dates back to ancient civilizations, with simple gear systems used in water wheels and windmills. However, the development of bevel gears, let alone their spiral variant, required more sophisticated understanding and technology. It wasn’t until the industrial revolution, with advancements in machining and material science, that the first simple bevel gears were produced.
The Advent of Spiral Bevel Gears:
While bevel gears with straight teeth were common in the early stages of the industrial revolution, their limitations soon became apparent. These gears were often noisy and had shorter lifespans due to the abrupt contact between the gear teeth. To overcome these limitations, spiral bevel gears were developed. The teeth in these gears are cut in a curved, oblique manner, allowing them to engage gradually and reduce the impact, noise, and vibration during operation.
20th Century Developments:
The 20th century brought significant developments in manufacturing technology, such as computer numerical control (CNC) and electric discharge machining (EDM). These technologies allowed for more precise and consistent manufacturing of spiral bevel gears, which improved their performance and reliability.
Furthermore, advancements in materials science led to the introduction of stronger, more durable materials for gear construction. These materials could better withstand the stresses and strains of operation, increasing the lifespan of spiral bevel gears.
Modern Spiral Bevel Gears:
Today, spiral bevel gears are sophisticated pieces of machinery. They are designed and manufactured using advanced computational techniques, such as finite element analysis (FEA), to predict and optimize their performance. These gears are often made from advanced materials, including various steel alloys, and even composite materials in some cases, for their superior strength-to-weight ratios.
Modern manufacturing techniques, such as 5-axis CNC machining and 3D printing, also allow for the production of spiral bevel gears with complex geometries and high precision. This has expanded their application in a variety of fields, from automotive and aerospace to robotics and renewable energy.
The evolution of spiral bevel gears is a testament to the progression of engineering and technology. From their early beginnings to their modern applications, these gears have constantly adapted and improved to meet the changing demands of industry and technology. As we look forward to future advancements, it is clear that spiral bevel gears will continue to play a critical role in power transmission and machinery design.