Worm gears are a valuable tool in various mechanical and industrial applications due to their unique design and function. They provide a range of advantages such as high torque output, self-locking capabilities, and compactness. However, like any mechanical component, they also have their limitations, including efficiency concerns and specific material requirements. This article provides a balanced view of the advantages and limitations of worm gears.
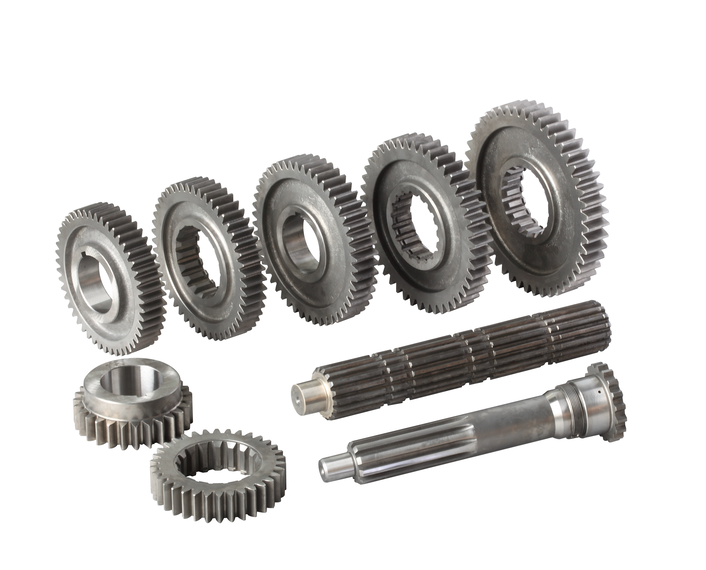
Advantages of Worm Gears
High Torque Output
Worm gears are renowned for their ability to deliver high torque output. Thanks to their high gear ratios, they can significantly reduce speed and increase torque, making them suitable for applications where heavy loads need to be handled.
Compact Design
Due to their design involving a worm (which resembles a screw) and a worm wheel (a gear), worm gears can fit into compact spaces. This design makes them an efficient choice for power transmission in small or densely packed machinery.
Self-Locking Capability
One of the most notable features of worm gears is their self-locking or non-reversible characteristic. The worm can easily turn the gear, but the gear cannot turn the worm due to the angle of contact and friction between the two components. This feature is crucial in applications where it’s necessary to prevent a system from moving or being driven backwards under load.
Quiet Operation
Worm gears are known for their quiet operation. Due to the sliding action between the worm and worm gear, they produce less noise compared to other gear types, making them suitable for applications where noise reduction is crucial.
Limitations of Worm Gears
Efficiency
One of the main drawbacks of worm gears is their relative inefficiency compared to other gear types. The sliding action between the worm and worm gear generates friction, leading to energy losses as heat. Depending on the design and materials, efficiency can range from 50% to 90%.
Material and Manufacturing Requirements
Worm gears require specific material combinations to function optimally and to prolong their lifespan. Typically, the worm is made from a hard material like hardened steel, while the worm gear is made from a softer material like bronze. These material requirements can increase the cost of worm gears. Additionally, manufacturing worm gears to precise specifications is a complex process, which may also contribute to higher costs.
Heat Dissipation
Due to the sliding contact and subsequent friction between the worm and worm gear, significant heat can be generated, especially in high-speed or high-load applications. This heat must be effectively managed and dissipated to prevent damage to the gear system, requiring additional considerations in the design and maintenance of the system.
In conclusion, while worm gears offer significant advantages like high torque output, compact design, self-locking capability, and quiet operation, they also come with limitations such as efficiency concerns, specific material and manufacturing requirements, and the need for effective heat management. As with any engineering decision, the choice to use worm gears should be based on a careful evaluation of these advantages and limitations in relation to the requirements of the specific application.