Hypoid gears and bevel gears are both types of gears commonly used in various applications. While they share some similarities, they also have distinct differences in design, functionality, and application suitability. In this comparative analysis, we will explore the key differences between hypoid gears and bevel gears.
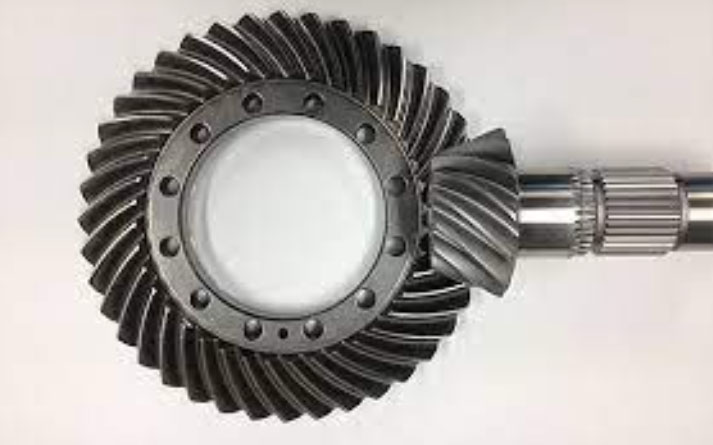
- Design and Tooth Geometry:
- Hypoid Gears: Hypoid gears have a curved tooth profile, which allows for a large contact area between the gear teeth. The tooth geometry is more complex compared to bevel gears, featuring a combination of spiral and offset tooth surfaces.
- Bevel Gears: Bevel gears have straight tooth profiles that are cut on a conical surface. The tooth geometry is relatively simpler compared to hypoid gears.
- Shaft Orientation and Torque Transmission:
- Hypoid Gears: Hypoid gears have an offset shaft alignment, meaning the input and output shafts are not collinear. This offset allows for torque transmission at an angle, making them suitable for applications requiring non-collinear shafts.
- Bevel Gears: Bevel gears have collinear shafts, meaning the input and output shafts are in line with each other. They transmit torque between shafts that intersect at a specific angle, typically 90 degrees.
- Efficiency and Power Transmission:
- Hypoid Gears: Hypoid gears offer high mechanical efficiency due to their larger contact area and optimized tooth engagement. They can transmit high torque with minimal power loss.
- Bevel Gears: Bevel gears generally have slightly lower mechanical efficiency compared to hypoid gears due to their smaller contact area. However, they are still efficient in transmitting power within their design parameters.
- Load Capacity and Applications:
- Hypoid Gears: Hypoid gears are known for their high torque capacity and ability to handle heavy loads. They find extensive applications in industries such as automotive differentials, heavy machinery, and power tools.
- Bevel Gears: Bevel gears have good load-carrying capacity but are typically used in applications with lower torque requirements. They are commonly found in applications such as gearboxes, machine tools, and rotary tables.
- Noise and Vibration:
- Hypoid Gears: Hypoid gears tend to produce less noise and vibration compared to straight bevel gears due to their curved tooth surfaces and offset shaft alignment. This makes them suitable for applications where noise reduction is a priority.
- Bevel Gears: Straight bevel gears can generate more noise and vibration due to their straight tooth surfaces. However, spiral bevel gears, which have curved tooth surfaces, offer improved noise characteristics compared to straight bevel gears.
- Manufacturing Complexity:
- Hypoid Gears: The manufacturing process for hypoid gears is more complex compared to bevel gears. Achieving the precise tooth geometry and offset shaft alignment requires specialized machining techniques and tools.
- Bevel Gears: Bevel gears have a relatively simpler manufacturing process compared to hypoid gears. The straight tooth profiles can be cut using conventional gear cutting methods.
In summary, hypoid gears and bevel gears have distinct design characteristics, functional differences, and application suitability. Hypoid gears offer advantages such as high torque capacity, efficient power transmission, and reduced noise, making them suitable for heavy-duty applications. Bevel gears, on the other hand, are commonly used in applications with collinear shafts and moderate torque requirements. Understanding the comparative analysis between hypoid gears and bevel gears is essential for selecting the most appropriate gear type for a given application.