Gear hobbing plays a vital role in the automotive industry, specifically in the manufacturing of powertrain systems. As powertrain technology advances to meet the demands of efficiency, performance, and reduced emissions, gear hobbing techniques have evolved to ensure the production of high-quality gears. This article explores the significance of gear hobbing in the automotive industry and how it helps meet the demands of modern powertrain systems.
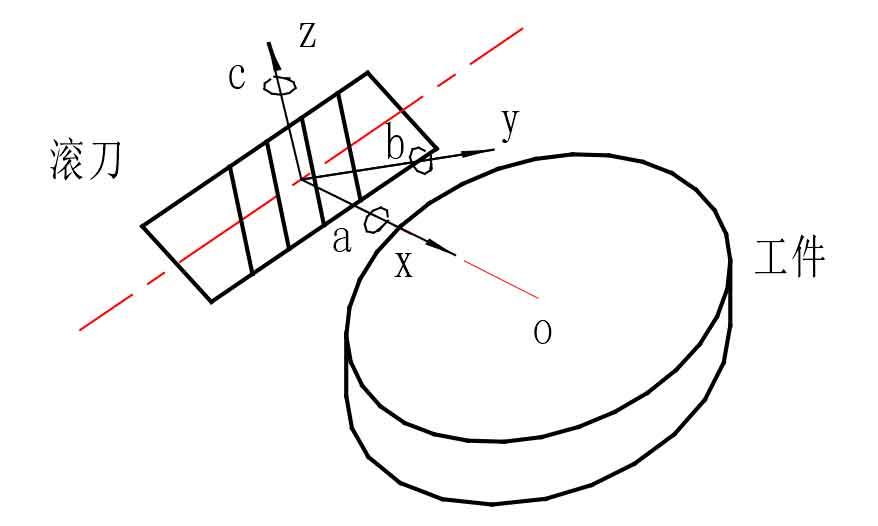
1.Powertrain Efficiency and Performance:
Powertrain systems in automobiles require gears that deliver optimal efficiency and performance. Gear hobbing enables the precise production of gear teeth with accurate profiles, tooth spacing, and surface finish. This ensures smooth gear meshing, reduced power losses, and improved energy transfer, ultimately enhancing powertrain efficiency and performance.
2.Gear Ratios and Power Distribution:
Automotive powertrains often consist of multiple gears with varying gear ratios to optimize torque delivery and engine performance. Gear hobbing allows for the production of custom gear ratios to suit specific powertrain requirements. Precise gear tooth profiles and controlled tolerances ensure accurate power distribution and reliable operation of the powertrain system.
3.Noise and Vibration Reduction:
Gear hobbing techniques contribute to noise and vibration reduction in automotive powertrains. Careful design considerations, such as optimizing tooth profiles, chamfering, and crowning, help minimize gear noise and vibrations during gear meshing. This enhances the overall driving experience by reducing unwanted noise and improving comfort.
4.Material Selection and Heat Treatment:
The automotive industry demands gears that can withstand high loads, shock, and fatigue. Gear hobbing enables manufacturers to work with a variety of materials suitable for automotive powertrain applications, including alloy steels and advanced materials like composites. Furthermore, precise heat treatment processes, such as carburizing and induction hardening, enhance gear hardness, wear resistance, and durability, ensuring the gears can handle demanding operating conditions.
5.Manufacturing Efficiency and Scalability:
Automotive manufacturers require gear production processes that are efficient and scalable to meet high production volumes. Gear hobbing machines are designed for mass production, allowing for the simultaneous cutting of multiple gear teeth. This reduces cycle times, increases productivity, and ensures consistent gear quality throughout large-scale production runs.
6.Continual Technological Advancements:
Gear hobbing techniques continue to evolve in response to the evolving automotive industry. Advancements in CNC control, automation, and simulation technology have improved gear hobbing precision, reduced setup times, and enabled virtual prototyping for optimized gear designs. These advancements contribute to faster development cycles, increased manufacturing efficiency, and improved gear performance.
Gear hobbing plays a crucial role in the automotive industry by meeting the demands of modern powertrain systems. Precise gear tooth profiles, customized gear ratios, and optimized designs ensure efficient power transmission, reduced noise and vibrations, and improved overall powertrain performance. Material selection, heat treatment, and advanced manufacturing processes further enhance gear durability and reliability. With continual technological advancements, gear hobbing techniques are evolving to meet the evolving needs of the automotive industry, supporting the production of powertrains that deliver enhanced efficiency, performance, and driving experience.