Forged gears and machined gears are two different manufacturing methods used to produce gears, each with its own set of advantages and considerations. Let’s compare forged gears and machined gears in terms of various factors:
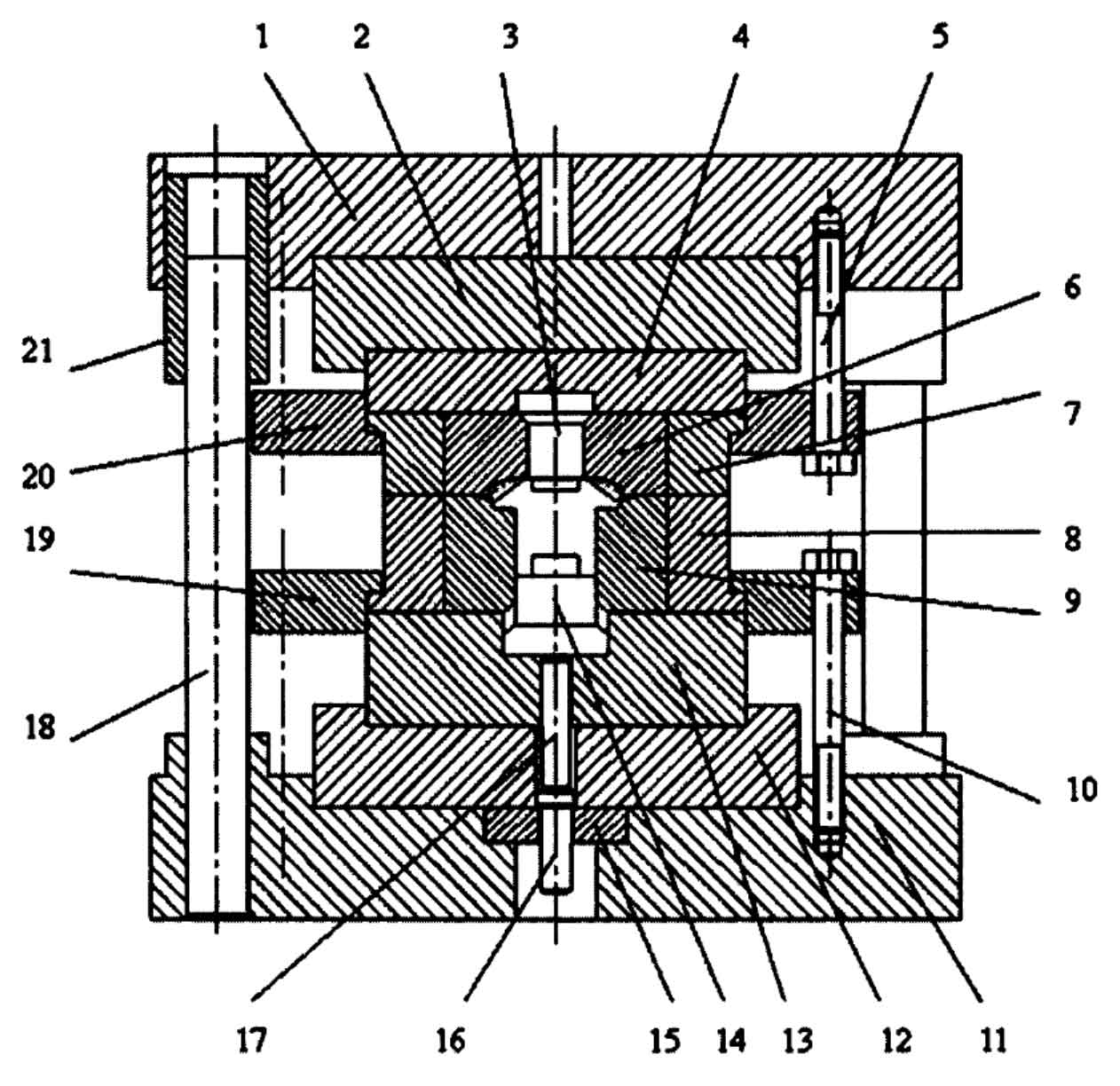
- Strength and Durability:
- Forged Gears: Forged gears are known for their exceptional strength and durability. The forging process aligns and refines the grain structure of the metal, resulting in improved mechanical properties and resistance to wear and fatigue. Forged gears can withstand heavy loads and harsh operating conditions.
- Machined Gears: Machined gears may have slightly lower strength compared to forged gears as they are cut from a solid block of material. The material properties remain relatively unchanged, and any inherent defects or weaknesses may persist.
- Material Integrity:
- Forged Gears: Gear forging preserves the integrity of the base material as no material is removed during the process. The continuous grain flow and structural integrity of the metal are maintained, resulting in gears with excellent mechanical properties and resistance to defects or failures.
- Machined Gears: Machining involves the removal of material, which can potentially introduce stress concentrations and weaken the gear. However, with proper machining techniques and material selection, the impact on material integrity can be minimized.
- Design Flexibility:
- Forged Gears: Forging allows for greater design flexibility and the creation of intricate and complex gear shapes. It offers the ability to produce gears with various tooth profiles, sizes, and shapes to meet specific application requirements.
- Machined Gears: Machining provides good design flexibility, but it may have some limitations when it comes to creating intricate or complex gear shapes. The gear design is constrained by the capabilities of the machining equipment.
- Cost Efficiency:
- Forged Gears: While gear forging may involve higher upfront tooling costs, forged gears offer long-term cost savings. Their enhanced strength and durability result in reduced maintenance, repair, and replacement costs over their operational lifespan.
- Machined Gears: Machining gears generally have lower upfront tooling costs compared to forging. However, they may require more frequent maintenance or replacement due to their potentially lower strength and durability.
- Precision and Tolerances:
- Forged Gears: Forged gears may have slightly lower dimensional precision and tighter tolerances compared to machined gears. The forging process involves some amount of deformation, which can result in minor dimensional variations.
- Machined Gears: Machining allows for high precision and tight tolerances. The cutting process can achieve precise gear tooth profiles and dimensions, ensuring accurate and consistent gear performance.
- Lead Time:
- Forged Gears: Gear forging typically involves multiple steps and may have longer lead times compared to machining. It requires heating, forging, heat treatment, and potentially additional machining operations.
- Machined Gears: Machining gears generally have shorter lead times as they involve cutting the gear from a solid block of material. The process is relatively faster and involves fewer steps.
It’s important to note that the choice between forged gears and machined gears depends on various factors such as the application requirements, desired gear properties, budget constraints, and production volume. In some cases, a combination of forging and machining processes may be used to achieve optimal results, where forging provides the strength and rough shape, followed by precision machining for final dimensions and surface finishes.