Gear forging offers several environmental benefits, making it a sustainable choice for gear production. Here are some of the key environmental advantages of gear forging:
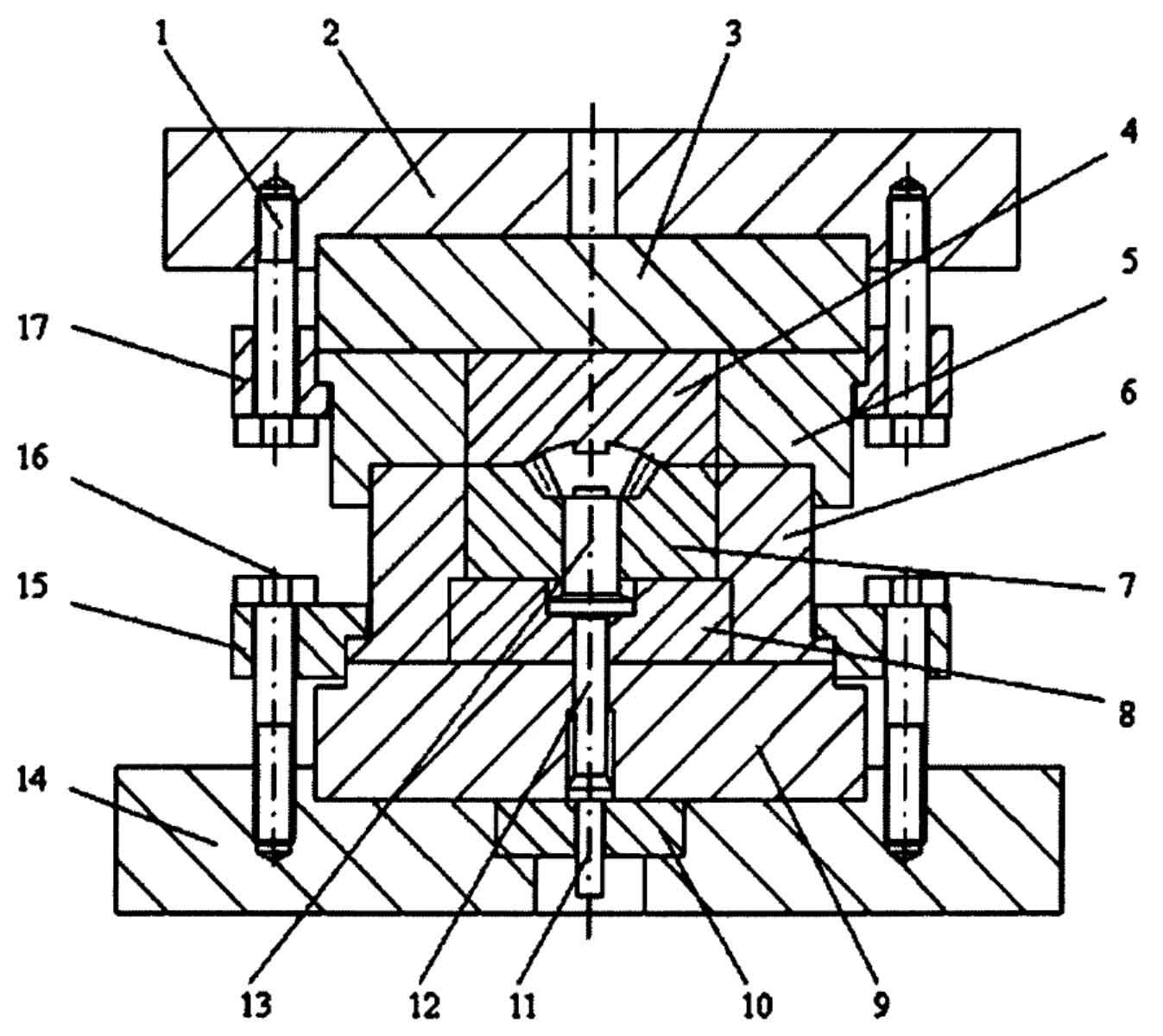
- Material Efficiency: Gear forging is a highly material-efficient manufacturing process. It minimizes material waste by using precise shaping techniques to form gears near their final shape. Compared to other manufacturing methods, such as machining, forging reduces the amount of material that needs to be removed, resulting in significant material savings. This efficiency helps conserve natural resources and reduces the environmental impact associated with raw material extraction and processing.
- Energy Efficiency: Gear forging is known for its energy efficiency compared to alternative gear manufacturing processes. Forging relies on the application of high pressure to shape the metal, requiring less energy than other methods that involve extensive material removal. The lower energy consumption during gear forging reduces greenhouse gas emissions and contributes to a more sustainable manufacturing process.
- Reduced Scrap and Waste Generation: The precise shaping of gears during the forging process minimizes scrap and waste generation. The near-net shape capabilities of forging enable the production of gears with close-to-final dimensions, resulting in minimal material trimming and machining requirements. This reduction in waste not only conserves resources but also reduces the need for disposal or recycling, thereby lowering environmental impact.
- Extended Product Lifespan: Forged gears are known for their exceptional strength, durability, and resistance to wear and fatigue. These characteristics contribute to longer gear lifespans, reducing the need for frequent gear replacements. By extending the operational life of gears, forging helps reduce the demand for new gear production, which in turn reduces resource consumption and waste generation associated with gear manufacturing.
- Recyclability: Forged gears are typically made from recyclable materials, such as steel alloys. At the end of their lifecycle, these gears can be recycled and reused to produce new gears or other metal components. The recyclability of forged gears promotes a circular economy by minimizing the need for new material extraction and reducing the environmental impact associated with mining and processing of raw materials.
- Reduced Environmental Footprint: The combination of material efficiency, energy efficiency, reduced waste generation, extended product lifespan, and recyclability makes gear forging an environmentally friendly choice. By reducing resource consumption, energy usage, and waste generation throughout the gear manufacturing process, forging helps lower the overall environmental footprint associated with gear production.
- Environmental Regulations Compliance: Gear forging processes typically adhere to environmental regulations and standards. Manufacturers follow guidelines for waste management, emissions control, and responsible disposal of process by-products. Compliance with these regulations ensures that gear forging operations minimize their environmental impact and operate in an environmentally responsible manner.
By choosing gear forging as a manufacturing method, companies can align their production processes with sustainability goals, reduce their environmental impact, and contribute to a more sustainable future. The environmental benefits of gear forging make it an attractive option for industries seeking to minimize their carbon footprint and promote sustainable practices.