Gear forging plays a vital role in the oil and gas industry, where gears are subjected to extreme operating conditions. Here’s how gear forging enables the production of gears that can meet the demanding requirements of the oil and gas sector:
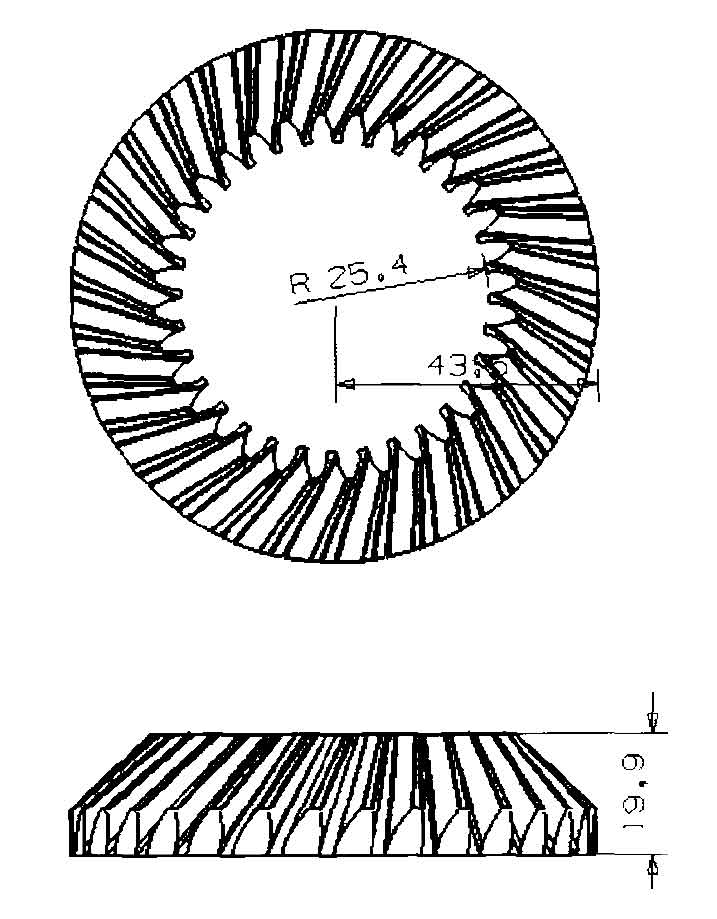
- Strength and Durability: Gears used in the oil and gas industry must withstand high torque, heavy loads, and harsh operating environments. Gear forging produces gears with exceptional strength, toughness, and resistance to wear and fatigue. Forged gears exhibit superior mechanical properties, including high tensile and impact strength, making them well-suited for heavy-duty applications in oil rigs, drilling equipment, and pumping systems.
- Corrosion Resistance: The oil and gas industry often involves exposure to corrosive environments, such as saltwater, drilling fluids, and sour gas. Forged gears can be manufactured from corrosion-resistant materials, such as stainless steels or alloys with specific anti-corrosion properties. These materials, combined with proper heat treatment, provide excellent resistance to corrosion, ensuring the gears can withstand prolonged exposure to corrosive substances.
- High Temperature and Pressure Resistance: Gears used in the oil and gas industry are exposed to high temperatures and pressures. Gear forging allows for the selection of materials with excellent high-temperature strength and creep resistance, enabling gears to perform reliably in extreme conditions. Specialized forging processes, such as isothermal forging or hot-die forging, may be employed to maintain material properties and dimensional stability under high-temperature conditions.
- Precision and Reliability: Gears used in critical oil and gas applications, such as drilling and pumping systems, require precise tooth profiles and tight dimensional tolerances. Gear forging enables the production of gears with accurate tooth geometry and excellent surface finish. The precise manufacturing process ensures proper tooth meshing, reduces gear misalignment, and enhances gear reliability and efficiency in demanding oil and gas operations.
- Customization for Application-Specific Requirements: The oil and gas industry encompasses various applications with unique gear requirements. Gear forging allows for customization to meet specific application needs. For example, gears used in downhole drilling tools may require special designs to handle extreme drilling forces and vibrations, while gears in pipeline compressors may require high-efficiency designs to optimize energy usage. Gear forging enables the production of gears tailored to the specific demands of each application, supporting innovation and continuous improvement in the oil and gas sector.
- Large Gear Production: The oil and gas industry often requires large gears for equipment such as gearboxes, turbines, and offshore platform machinery. Gear forging is well-suited for producing large gears due to its ability to handle heavy forgings and accommodate complex shapes. The scalability of gear forging processes allows for the production of large gears with consistent mechanical properties and dimensional accuracy, ensuring reliable performance in critical oil and gas applications.
- Resistance to Shock and Vibration: Oil and gas equipment is subjected to significant shock and vibration loads during operation. Forged gears exhibit excellent resistance to shock and vibration due to their inherent strength and toughness. The superior fatigue resistance of forged gears helps prevent premature gear failures, ensuring reliable performance and minimizing downtime in oil and gas operations.
Gear forging’s ability to produce gears with exceptional strength, durability, corrosion resistance, high-temperature capability, and precise tooth profiles makes it a crucial technology for meeting the extreme conditions encountered in the oil and gas industry. By providing reliable and robust gear solutions, gear forging contributes to the safe and efficient operation of oil and gas equipment in challenging environments.