Compare worm gears and miter gears, two different types of gears, and analyze their characteristics and applications:
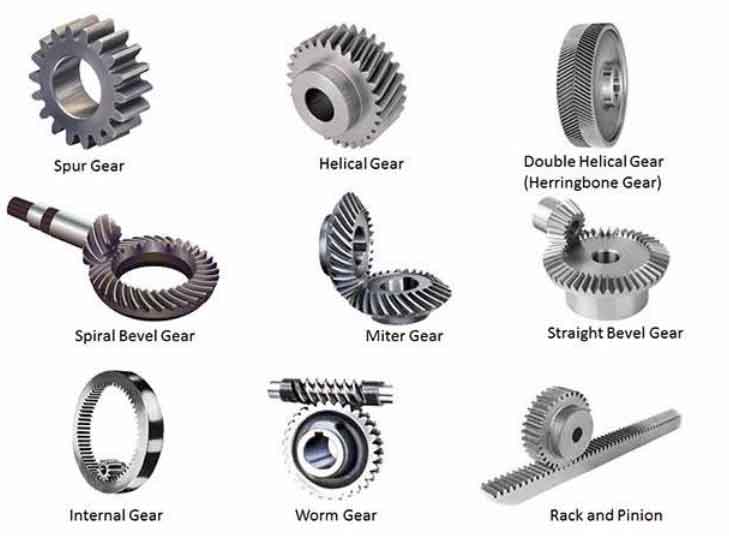
- Design and Operation:
- Worm Gears: Worm gears consist of a cylindrical screw-like gear called the worm and a toothed wheel called the worm wheel. The worm typically has a single-thread helix, and the worm wheel has teeth that mesh with the worm. Worm gears are used to transmit motion between non-parallel shafts and provide high gear reduction ratios.
- Miter Gears: Miter gears, also known as bevel gears, have intersecting axes and transmit motion between intersecting shafts. They have teeth that are cut on conical surfaces. Miter gears can have straight teeth (straight bevel gears) or curved teeth (spiral bevel gears).
- Efficiency:
- Worm Gears: Worm gears are known to have lower efficiency compared to some other gear types. The sliding action between the worm and the worm wheel generates more friction, leading to some power loss. Efficiency can range from 30% to 90%, depending on factors like gear materials, lubrication, and tooth profile.
- Miter Gears: Miter gears can have high efficiency, especially in the case of spiral bevel gears. Proper tooth design and high-quality manufacturing can result in efficient power transmission. Efficiency levels above 95% can be achieved with well-designed miter gears.
- Torque Capacity:
- Worm Gears: Worm gears are capable of handling high torque loads due to their large contact area and substantial gear reduction ratios. They are commonly used in applications requiring high torque transmission, such as heavy machinery, conveyors, and automotive differentials.
- Miter Gears: Miter gears have good torque-carrying capacity, but it is generally lower compared to worm gears. They are suitable for applications with moderate torque requirements, such as power tools, printing presses, and certain automotive systems.
- Compactness and Space Constraints:
- Worm Gears: Worm gears have a compact design and can transmit motion at right angles, making them suitable for applications with limited space. They are often preferred in situations where space constraints are a concern.
- Miter Gears: Miter gears have a larger form factor due to their intersecting axes. They may require more space for installation compared to worm gears. However, their ability to transmit motion between intersecting shafts makes them a suitable choice for applications where space is available in the axial direction.
- Applications:
- Worm Gears: Worm gears find applications in various industries, including automotive, industrial machinery, and material handling systems. They are commonly used in applications requiring high torque transmission, compact design, and the ability to transmit motion at right angles.
- Miter Gears: Miter gears are utilized in a wide range of applications, including machine tools, robotics, marine systems, and automotive differentials. Their ability to transmit motion between intersecting shafts makes them suitable for systems where power needs to be transmitted at an angle.
- Noise and Vibration:
- Worm Gears: Worm gears can generate more noise and vibration due to the sliding action between the worm and the worm wheel. Proper lubrication and gear design can help mitigate these effects to some extent.
- Miter Gears: Miter gears, especially spiral bevel gears, are known for their smooth operation and low noise levels. The teeth engagement in miter gears provides a relatively quieter operation compared to worm gears.
- Lubrication and Maintenance:
- Worm Gears: Effective lubrication is crucial for worm gears due to the sliding contact between gear surfaces. Regular maintenance, such as proper lubricant application, oil changes, and inspection for wear, is necessary
- to ensure the longevity and smooth operation of worm gears.
- Miter Gears: Miter gears also require proper lubrication to minimize friction and wear. Regular maintenance, including lubricant checks and gear inspection, is recommended to maintain optimal performance.
- Cost:
- Worm Gears: Worm gears are generally more cost-effective compared to miter gears. Their simpler design and manufacturing process result in lower production costs.
- Miter Gears: Miter gears, especially spiral bevel gears, can be more expensive to manufacture due to their complex tooth geometry and precision requirements. This can contribute to higher costs compared to worm gears.
- Alignment:
- Worm Gears: Worm gears are less sensitive to alignment issues since they can accommodate some misalignment between the worm and the worm wheel. This feature makes them suitable for applications where perfect alignment is challenging to achieve.
- Miter Gears: Miter gears require precise alignment of the intersecting shafts for smooth and efficient operation. They may require more attention to alignment during installation and maintenance.
Worm gears and miter gears have distinct characteristics that make them suitable for different applications. Worm gears excel in transmitting motion at right angles, providing high gear reduction ratios and accommodating some misalignment. Miter gears, on the other hand, are ideal for transmitting motion between intersecting shafts and can offer efficient power transmission, especially in the case of spiral bevel gears. Consider the specific requirements of your application, such as torque, space constraints, efficiency, and cost, to determine the most appropriate gear type for your needs. Consulting with a mechanical engineer or a gear specialist can provide further guidance based on your specific application.