Spiral gears and herringbone gears are both types of gears used in various applications to transmit power and motion between rotating shafts. While they serve similar purposes, there are significant differences between them in terms of design, performance, and application. Let’s delve into a comparative analysis of spiral gears and herringbone gears:
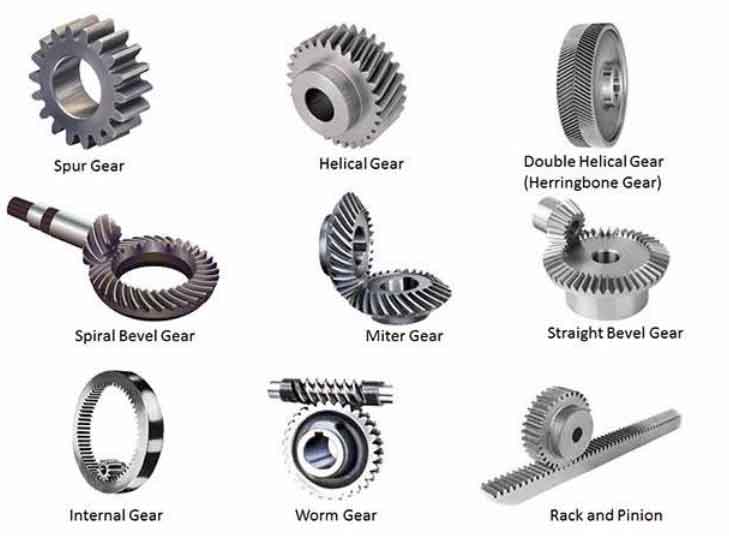
- Design:
- Spiral Gears: Spiral gears have teeth that are cut at an angle to the gear’s face. This angle allows for gradual engagement of the teeth, resulting in smoother and quieter operation compared to other gear types. Spiral gears are typically used for higher-speed applications.
- Herringbone Gears: Herringbone gears, also known as double helical gears, have teeth that are cut in a “V” shape. This design eliminates axial thrust forces that are generated in single helical gears, making herringbone gears ideal for high-load and high-speed applications.
- Load Capacity:
- Spiral Gears: Spiral gears are capable of transmitting high torque loads, making them suitable for applications requiring heavy-duty power transmission. They can handle both radial and axial loads effectively.
- Herringbone Gears: Herringbone gears excel in transmitting heavy loads due to their symmetrical design, which eliminates the axial thrust forces. They are commonly used in applications where high torque and high-speed operation are required.
- Efficiency:
- Spiral Gears: Spiral gears provide excellent meshing contact, resulting in high efficiency. The gradual engagement of teeth reduces noise and vibration, minimizing power losses.
- Herringbone Gears: Herringbone gears also offer high efficiency due to their symmetrical tooth design and absence of axial thrust forces. They provide smooth and uniform power transmission, minimizing energy losses.
- Noise and Vibration:
- Spiral Gears: The spiral angle of the teeth in spiral gears allows for gradual contact and smoother meshing, resulting in reduced noise and vibration compared to other gear types. This makes them well-suited for applications that require quieter operation.
- Herringbone Gears: Herringbone gears are known for their excellent noise-canceling properties. The double helical teeth design cancels out the axial thrust forces, resulting in quieter operation and reduced vibration.
- Manufacturing Complexity:
- Spiral Gears: Spiral gears are relatively easier to manufacture compared to herringbone gears. They can be produced using standard gear-cutting tools and methods.
- Herringbone Gears: Herringbone gears are more complex to manufacture due to their double helical tooth profile. Specialized gear-cutting equipment is required to produce herringbone gears accurately.
- Application:
- Spiral Gears: Spiral gears find application in various industries, including automotive, power generation, and heavy machinery. They are suitable for applications that require high torque, moderate-to-high speeds, and smooth operation.
- Herringbone Gears: Herringbone gears are commonly used in heavy machinery, oil and gas industry, and power transmission systems. They are ideal for applications that involve high loads, high speeds, and require noise reduction.
In summary, while both spiral gears and herringbone gears are effective gear types, they differ in design, load capacity, efficiency, noise and vibration characteristics, manufacturing complexity, and application suitability. Understanding these differences is crucial for selecting the appropriate gear type based on the specific requirements of the intended application.