Spiral gears and miter gears are two common types of gears used in various mechanical systems. While they both serve the purpose of transmitting rotational motion and power between shafts, there are some key differences between them in terms of design, application, and performance. Let’s compare spiral gears and miter gears in more detail.
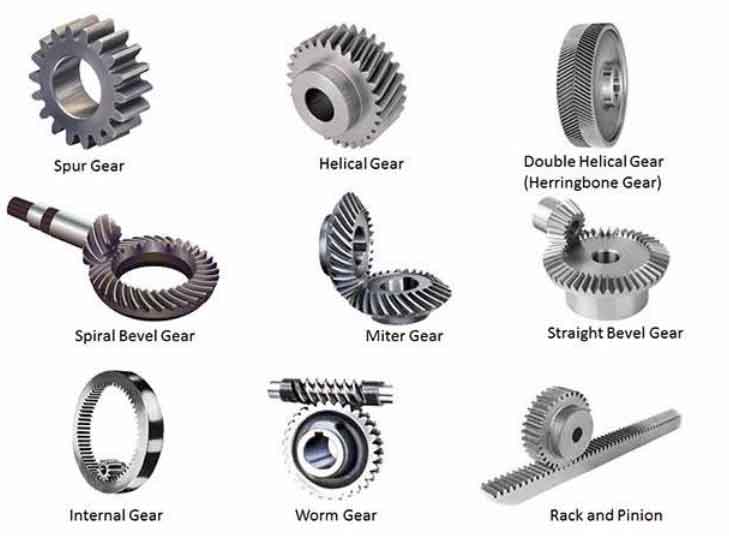
- Design:
- Spiral Gears: Spiral gears have teeth that are cut in a helical pattern around the gear’s circumference. The helix angle creates a gradual engagement between the teeth, resulting in smoother and quieter operation compared to straight-cut gears. They are usually made with a 90-degree shaft angle but can be designed for other angles as well.
- Miter Gears: Miter gears, also known as bevel gears, have teeth cut in a conical shape. The teeth of miter gears are cut at an angle of 45 degrees, allowing them to transmit power and motion between two intersecting shafts that are positioned at a 90-degree angle to each other.
- Power Transmission:
- Spiral Gears: Spiral gears are well-suited for transmitting high power and torque loads. The gradual engagement of the helical teeth allows for smooth and efficient power transmission, reducing noise and vibration. They are commonly used in applications such as heavy machinery, automotive transmissions, and gearboxes.
- Miter Gears: Miter gears are typically used for transmitting lower power and torque loads. Due to the 45-degree angle of the teeth, miter gears are not as efficient in power transmission as spiral gears. They find applications in areas like hand tools, household appliances, and some machinery where a 90-degree shaft angle is required.
- Efficiency:
- Spiral Gears: The helical tooth design of spiral gears offers better load distribution and contact ratio, resulting in higher efficiency compared to miter gears. The gradual tooth engagement also reduces the risk of tooth breakage, making them more durable in high-load applications.
- Miter Gears: Miter gears have a lower efficiency compared to spiral gears due to the 45-degree tooth angle, which creates a less favorable contact ratio. They may experience more noise, vibration, and higher wear under heavy loads.
- Noise and Vibration:
- Spiral Gears: Spiral gears are known for their smooth and quiet operation due to the helical tooth design, which minimizes sudden impacts between gear teeth. The gradual engagement helps reduce noise and vibration, making them suitable for applications where noise control is important.
- Miter Gears: Miter gears, particularly straight-cut bevel gears, can generate more noise and vibration compared to spiral gears. The contact between the teeth can be more abrupt, resulting in higher impact forces and noise levels.
- Lubrication and Maintenance:
- Spiral Gears: Spiral gears typically require proper lubrication due to the sliding contact between the helical teeth. Adequate lubrication is crucial to minimize wear and ensure smooth operation. Regular maintenance and lubricant checks are important to maintain their performance.
- Miter Gears: Miter gears have rolling contact between their teeth, which reduces the need for lubrication. However, lubrication may still be required in certain applications to minimize friction and wear. Maintenance requirements are generally lower compared to spiral gears.
Spiral gears are preferred for high-power applications that require smooth operation, high efficiency, and durability. Miter gears, on the other hand, are suitable for lower-power applications where a 90-degree shaft angle is required but are less efficient and produce more noise and vibration. The choice between spiral gears and miter gears depends on the specific requirements of the application, including power transmission needs, operating conditions, noise considerations, and maintenance preferences.