Helical gears can generate noise due to various factors such as gear meshing, vibration, and resonance. Implementing noise reduction strategies can help mitigate these issues. Here are some engineering solutions for reducing noise in helical gear systems:
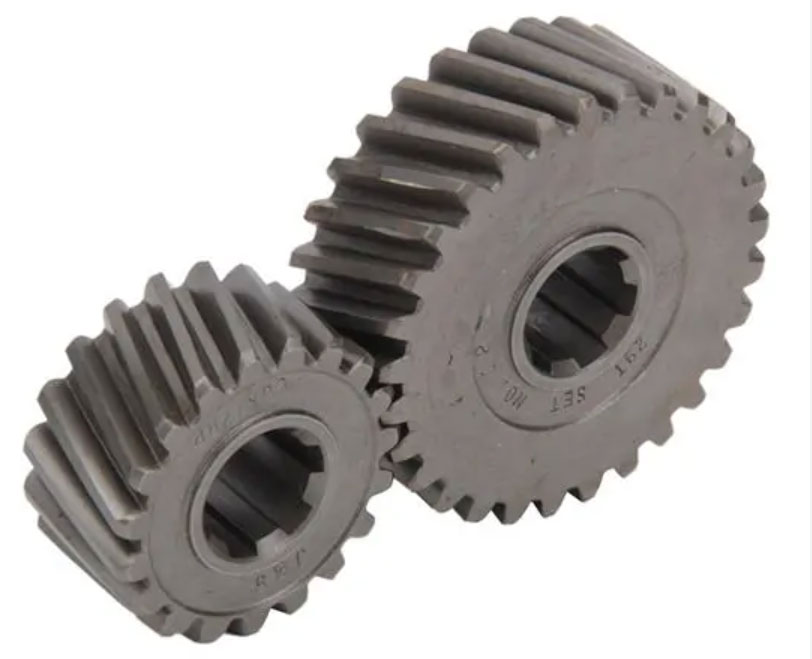
- Profile Modification: Modifying the gear tooth profile can help reduce noise by minimizing tooth-to-tooth impact during meshing. Profile modifications like lead crowning, tip relief, and tip chamfering can help distribute the load more evenly, reducing noise generation.
- Tooth Surface Finishing: Improving the surface finish of gear teeth can reduce friction and noise. Processes like grinding, honing, or superfinishing can help achieve smoother gear surfaces, reducing noise caused by surface roughness and irregularities.
- Helix Angle Optimization: Proper selection of the helix angle can significantly reduce gear noise. Increasing the helix angle can improve load distribution and minimize edge contact, resulting in quieter operation. However, excessively high helix angles may reduce efficiency, so a balance must be struck.
- Material Selection and Heat Treatment: Choosing high-quality gear materials and applying appropriate heat treatments can help reduce noise. Materials with good strength, hardness, and fatigue resistance can withstand higher loads and reduce gear deformation and noise. Heat treatments like carburizing or nitriding can improve the surface hardness and reduce friction, resulting in quieter operation.
- Lubrication: Proper lubrication is essential for noise reduction in gear systems. Selecting a high-quality lubricant with suitable viscosity, additives, and compatibility with gear materials can help minimize friction and noise. Maintaining the correct lubricant level and ensuring proper lubricant distribution within the gear meshing area are also important.
- Gear Housing and Mounting: Designing a robust gear housing and mounting system can help dampen noise and vibration. Properly designed housings with adequate stiffness and damping properties can reduce the transmission of noise to the surrounding environment.
- Vibration Damping: Applying vibration-damping materials or coatings to the gear housing and other components can help absorb noise and vibration. Rubber or elastomeric coatings can effectively reduce noise transmission and dampen vibrations.
- Dynamic Analysis and Optimization: Conducting dynamic analysis using computer-aided engineering (CAE) tools can help identify critical resonances and vibration modes. By optimizing the gear design, such as modifying gear tooth profiles or adjusting gear parameters, resonance-related noise issues can be mitigated.
- Noise Testing and Validation: Performing noise testing and validation on gear systems can help identify specific noise sources and validate the effectiveness of noise reduction measures. This can involve using sound level meters, accelerometers, or other specialized testing equipment.
It’s important to note that the specific noise reduction strategies employed may depend on the application requirements and constraints. Working with experienced gear designers and consulting relevant industry standards can help identify the most suitable engineering solutions for a given helical gear system.