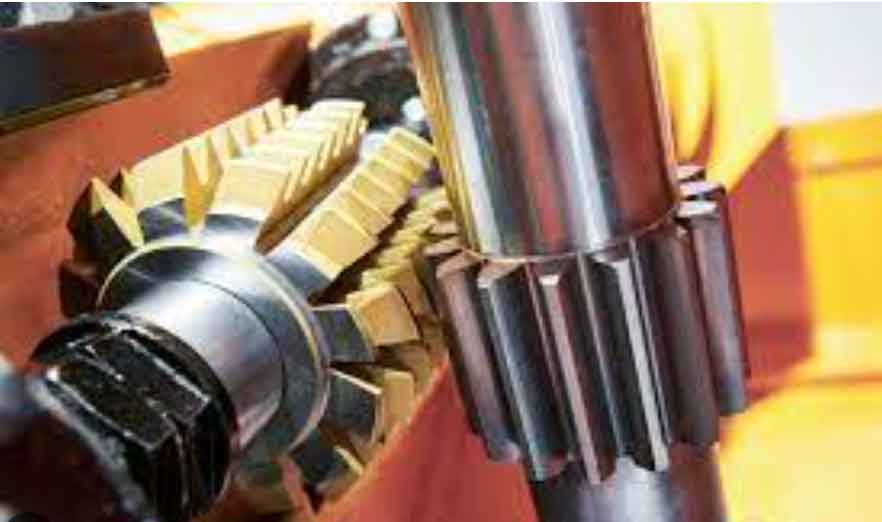
Gear hobbing is a widely used gear manufacturing process that involves cutting teeth on cylindrical workpieces using a specialized tool called a hob. This comprehensive guide will take you through the various steps involved in gear hobbing, including the setup, cutting process, and post-processing.
- Gear Hobbing Setup:
- Selection of the Workpiece: Choose a suitable cylindrical workpiece with the required dimensions and material properties for the gear.
- Selection of the Hob: Select a hob with the desired tooth profile and dimensions suitable for the gear being produced.
- Machine Setup: Mount the workpiece and hob on the gear hobbing machine, ensuring proper alignment and clamping.
- Gear Hobbing Process:
- Gear Blank Preparation: Prior to hobbing, the gear blank is typically pre-machined to remove any excess material and provide an appropriate starting shape.
- Gear Hobbing Operation: The gear hobbing machine rotates the workpiece while the hob is fed into it, resulting in the cutting of the gear teeth. The hob’s teeth progressively engage the workpiece, generating the desired tooth profile.
- Feed and Speed Control: Proper control of the hob’s feed rate and rotational speed of the workpiece ensures accurate tooth cutting and minimizes tool wear.
- Indexing: After each revolution of the workpiece, it is indexed by a precise amount to align the next tooth space with the hob, allowing the cutting process to continue.
- Gear Hobbing Parameters:
- Feed Rate: The rate at which the hob advances into the workpiece, determining the depth of cut per revolution.
- Cutting Speed: The speed at which the workpiece rotates during the hobbing process, usually expressed in surface feet per minute (SFM) or meters per minute (m/min).
- Hob Pressure Angle: The angle between the hob’s teeth and a line perpendicular to the hob’s axis. It determines the shape of the gear teeth.
- Hob Shift: The axial movement of the hob relative to the workpiece, enabling the cutting of gears with different numbers of teeth.
- Depth of Cut: The distance the hob travels into the workpiece, determining the tooth thickness and gear accuracy.
- Gear Hobbing Machine Types:
- Vertical Gear Hobbing Machines: Suitable for small to medium-sized gears and are commonly used in job shops and small-scale manufacturing.
- Horizontal Gear Hobbing Machines: Ideal for large gears and high-volume production, often found in automotive and heavy machinery industries.
- CNC Gear Hobbing Machines: Computer-controlled machines offering enhanced precision, flexibility, and automation in gear hobbing operations.
- Gear Hobbing Advantages:
- High Efficiency: Gear hobbing can produce gears with high accuracy and productivity, making it suitable for mass production.
- Versatility: It can manufacture a wide range of gear types, including spur, helical, worm, and spline gears.
- Cost-Effectiveness: Gear hobbing is a cost-effective method for producing gears compared to other manufacturing processes.
- Design Flexibility: Gear hobbing allows for customization of gear tooth profiles and various gear parameters.
- Gear Hobbing Post-Processing:
- Deburring: After hobbing, gears often require deburring to remove any sharp edges or burrs resulting from the cutting process.
- Heat Treatment: Depending on the application, gears may undergo heat treatment processes such as quenching and tempering to enhance their hardness and strength.
- Finishing Operations: Gear teeth may undergo additional operations like grinding, honing, or lapping to improve surface finish and tooth profile accuracy.
It’s important to note that gear hobbing is a complex manufacturing process that requires expertise and specialized equipment. The specific details and parameters may vary depending on the gear type,
Pages: 1 2