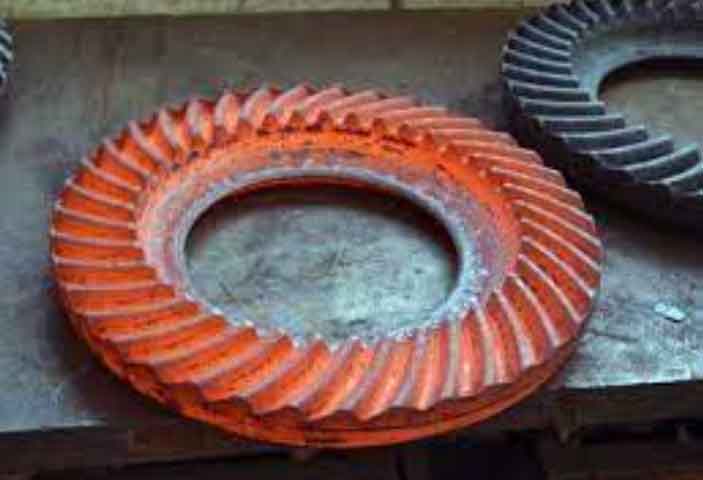
Gear forgings offer several advantages in industrial applications. Here are some of the key benefits:
- Strength and Durability: Gear forgings are known for their exceptional strength and durability. The forging process involves shaping metal under high pressure, which aligns the grain structure and eliminates defects, resulting in a more robust and reliable gear. This makes gear forgings capable of handling high loads, shock, and vibration, ensuring long-lasting performance even in demanding industrial environments.
- Enhanced Fatigue Resistance: Gears often experience cyclic loading, which can lead to fatigue failure over time. Gear forgings have superior fatigue resistance compared to other manufacturing methods like casting or machining. The controlled grain structure obtained through forging helps distribute the stresses more evenly, reducing the risk of fatigue cracks and extending the gear’s operational life.
- Improved Mechanical Properties: The forging process improves the mechanical properties of gears. It refines the grain structure, increases the material density, and enhances the uniformity of the mechanical properties throughout the gear. As a result, gear forgings exhibit improved tensile strength, impact resistance, and wear resistance, ensuring reliable performance under challenging operating conditions.
- Design Flexibility: Gear forgings offer design flexibility, allowing manufacturers to create complex gear shapes and incorporate specific features tailored to the application requirements. With forging, it is possible to produce near-net or net-shaped gears, minimizing the need for additional machining operations. This not only reduces material waste but also saves time and cost in the manufacturing process.
- Cost-Effectiveness: While gear forgings may have higher upfront costs compared to alternative methods such as casting, their long-term cost-effectiveness is often superior. The durability and extended lifespan of gear forgings result in reduced maintenance, repair, and replacement expenses over time. Moreover, the improved mechanical properties of forgings can lead to better efficiency, lower energy consumption, and increased productivity in industrial systems.
- Consistency and Reliability: Gear forgings offer excellent dimensional accuracy and consistency. The forging process ensures precise control over the shape, size, and tolerances of the gears, resulting in uniform products with reliable performance characteristics. This consistency is crucial in industrial applications where gears must fit and operate seamlessly within complex machinery and systems.
- Material Choices: Gear forgings can be produced using a wide range of materials, including various steels and alloys. This enables manufacturers to select the most suitable material based on factors such as strength requirements, wear resistance, heat resistance, and corrosion resistance. The ability to choose from different materials expands the applicability of gear forgings in diverse industrial sectors.
Gear forgings provide superior strength, durability, fatigue resistance, and mechanical properties compared to alternative manufacturing methods. Their design flexibility, cost-effectiveness, consistency, and choice of materials make them an excellent choice for industrial applications where reliable and high-performance gears are essential.