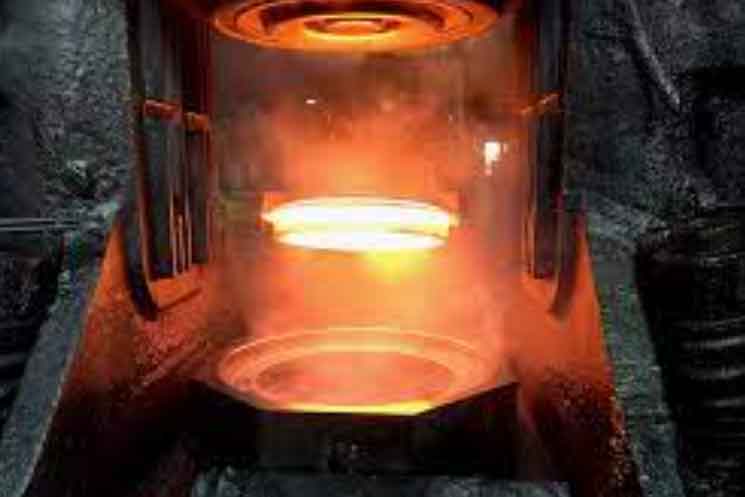
The production of gear forgings involves a series of steps that transform raw materials into high-performance gears. Let’s explore the typical process of manufacturing gear forgings and the key stages involved.
- Material Selection: The first step is selecting the appropriate material for the gear forging. The choice of material depends on factors such as the application requirements, operating conditions, load capacity, and desired properties like strength, wear resistance, and heat resistance. Common materials used for gear forgings include alloy steels, carbon steels, stainless steels, and specialty alloys.
- Billet Preparation: Once the material is selected, the next step is preparing the billet, which is a cylindrical or rectangular piece of raw material. Billets are typically obtained through processes like casting or hot rolling. The billet’s size and shape depend on the final gear’s design and dimensions.
- Heating: The billet is heated to a specific temperature to make it malleable for forging. The heating process, known as heat treatment, is crucial for achieving the desired material properties. The temperature and time at which the billet is heated depend on the material type and the desired properties of the final gear.
- Forging: After heating, the billet is placed in a forging press or hammer. The forging process involves applying pressure to the heated billet to shape it into the desired gear form. This is typically done in multiple steps, with intermediate heat treatments if necessary, to achieve the desired shape and mechanical properties. The forging process refines the grain structure of the material, aligns the grain flow, and eliminates any defects present in the initial billet.
- Heat Treatment: Once the forging process is complete, the forged gear undergoes heat treatment to further enhance its material properties. Common heat treatment techniques include quenching and tempering. Quenching involves rapidly cooling the gear to increase its hardness, while tempering is performed to reduce brittleness and improve toughness. The specific heat treatment process depends on the material and the desired properties of the gear.
- Machining: After heat treatment, the forged gear may undergo machining operations to achieve the final dimensions and surface finish. Machining processes such as turning, milling, drilling, and grinding are used to remove excess material, create gear teeth, and achieve the required tolerances and surface quality.
- Finishing Operations: Once the gear is machined, it may undergo additional finishing operations to enhance its performance. These operations can include shot peening to increase fatigue strength, surface coating or plating for improved wear resistance or corrosion protection, and deburring to remove any sharp edges or burrs.
- Quality Control: Throughout the manufacturing process, quality control checks are performed to ensure that the gears meet the required specifications. These checks can include dimensional measurements, non-destructive testing, and inspection of material properties. Quality control ensures that the final gear forging meets the desired standards for strength, dimensional accuracy, surface finish, and other critical parameters.
By following these steps, gear manufacturers can produce high-performance gear forgings that offer exceptional strength, durability, and reliability. Each stage of the process, from material selection to quality control, is crucial in ensuring the final product meets the demanding requirements of various industries, such as automotive, aerospace, and heavy machinery.