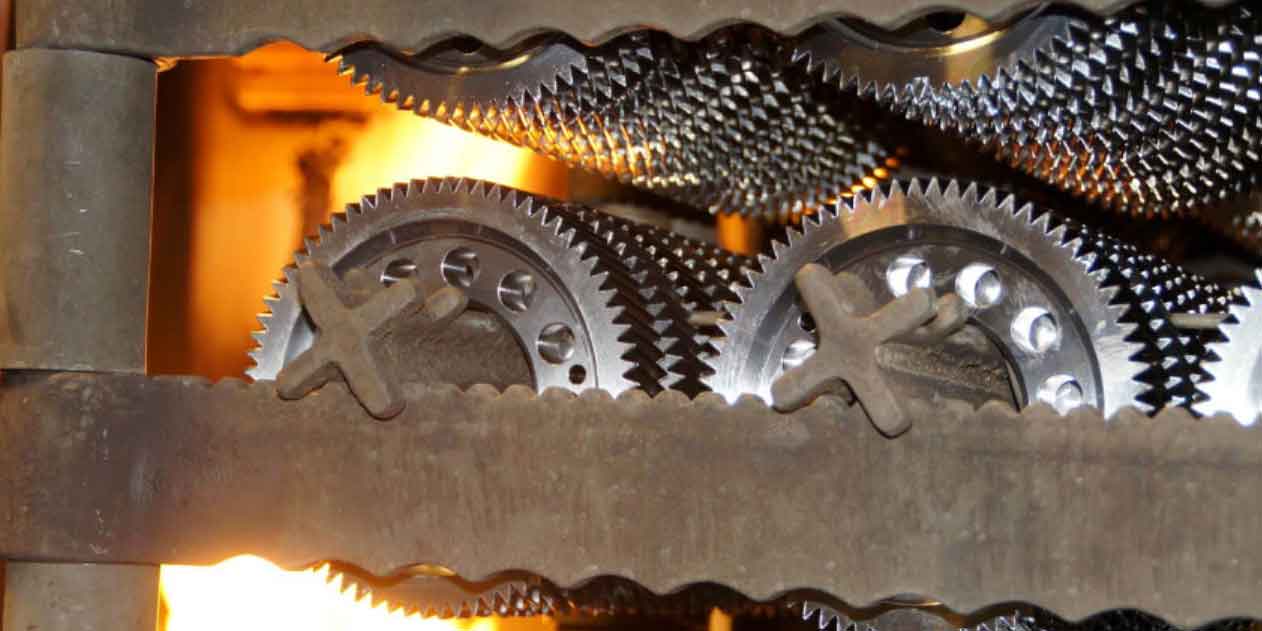
Forged gears are known for their exceptional strength and durability, making them a popular choice in various industries, including automotive, aerospace, and heavy machinery. The process of gear forging involves shaping metal under extreme pressure and heat, resulting in a final product that offers superior mechanical properties compared to gears produced by other manufacturing methods, such as casting or machining. Let’s delve into the key aspects that contribute to the strength and durability of forged gears.
1.Material Selection:
Forged gears are commonly made from alloy steels that exhibit high strength, toughness, and wear resistance. The choice of material depends on the specific application, load requirements, and environmental factors. Some popular materials for forged gears include carbon steels, alloy steels (such as chromium-molybdenum and nickel-chromium-molybdenum steels), and stainless steels.
2.Metallurgical Integrity:
During the forging process, the metal undergoes controlled deformation, resulting in a refined grain structure. This grain refinement enhances the mechanical properties of the gears, including increased strength, improved fatigue resistance, and reduced susceptibility to cracking or failure. The metallurgical integrity achieved through forging ensures uniform material properties throughout the gear, providing consistent performance.
3.Impact Resistance:
Forged gears exhibit excellent impact resistance, which is vital in applications where sudden loads or shocks can occur. The forging process aligns the grain structure in the direction of anticipated stress, enhancing the gear’s ability to withstand impact loads without deformation or fracture. This makes forged gears particularly suitable for heavy-duty applications where reliability is crucial.
4.Fatigue Strength:
Gears often experience cyclic loads, leading to fatigue failure if not properly designed or manufactured. Forged gears have superior fatigue strength due to their refined grain structure and absence of internal defects commonly found in other manufacturing processes. The controlled deformation during forging ensures a uniform distribution of stress, reducing the likelihood of fatigue cracks and extending the gear’s service life.
5.Surface Integrity:
The forging process produces gears with a superior surface finish, eliminating the need for additional machining operations. The absence of parting lines, shrinkage cavities, or porosity commonly associated with casting processes enhances the overall integrity of forged gears. Additionally, the precise dimensional control achieved through forging minimizes the risk of stress concentrations, which can lead to premature failure.
6.Design Flexibility:
Forging offers greater design flexibility compared to other manufacturing methods. Complex gear geometries can be achieved through various forging techniques, such as open-die forging or closed-die forging. This flexibility allows for the production of gears with custom profiles, optimized tooth forms, and tailored features to meet specific application requirements.
Forged gears are renowned for their strength and durability due to the metallurgical integrity achieved during the forging process. The combination of material selection, controlled grain refinement, impact resistance, fatigue strength, excellent surface integrity, and design flexibility makes forged gears a reliable choice for demanding applications that require high-performance and long-lasting gear components.