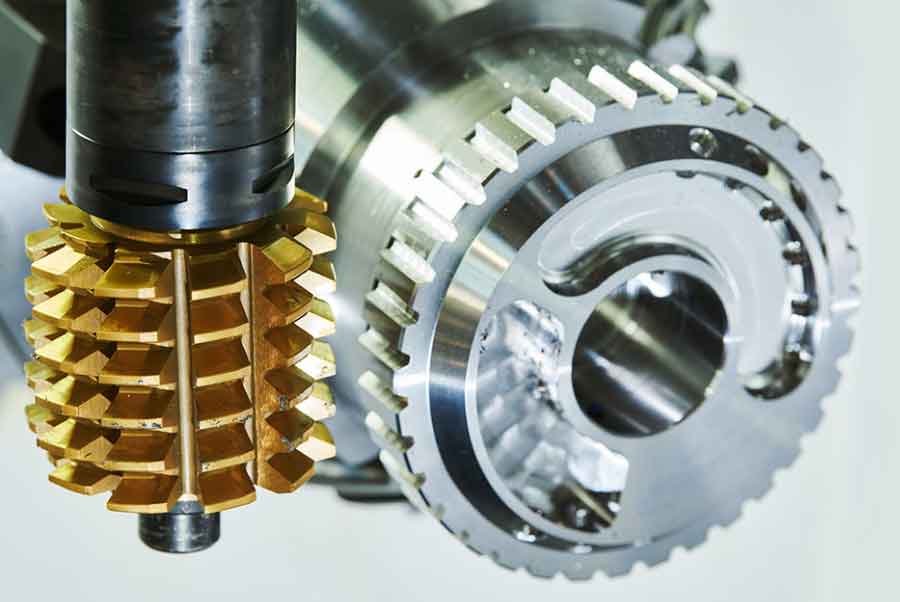
Gear hobbing is a fundamental process in gear production that involves the transformation of design concepts into physical gear components. From the initial concept to the final creation, gear hobbing plays a crucial role in bringing gears to life. This article outlines the key stages involved in the gear hobbing process, highlighting the steps from concept to the actual production of gears.
I. Gear Design and Engineering:
The gear production process begins with gear design and engineering. During this stage, engineers analyze the requirements of the gear application and determine the gear specifications, such as tooth size, profile, pitch, and material. Advanced computer-aided design (CAD) software is used to create a virtual representation of the gear, enabling engineers to visualize and optimize the design before moving forward.
II. Tooling Design and Preparation:
Once the gear design is finalized, the next step is tooling design and preparation. This involves the design and manufacturing of the hob, the specialized cutting tool used in the gear hobbing process. The hob is designed to match the desired tooth profile and specifications of the gear. The selection of appropriate hob materials, coatings, and tool geometries is crucial to ensure accurate and efficient gear cutting.
III. Machine Setup and Calibration:
After the tooling is prepared, the gear hobbing machine is set up and calibrated. The machine settings, such as hob speed, feed rate, and axis movements, are configured based on the gear design and material properties. Proper machine setup and calibration are essential to achieve precise and consistent gear cutting results.
IV. Gear Blank Preparation:
The gear hobbing process requires a gear blank, which is the starting material for creating the gear. Gear blanks are typically cylindrical or disk-shaped pieces of metal that are carefully selected based on material properties and size requirements. The gear blank is mounted securely on the machine’s spindle, ready for the hobbing operation.
V. Gear Hobbing Operation:
The actual gear hobbing operation takes place during this stage. The hob is brought into contact with the gear blank, and the cutting process begins. The hob rotates while simultaneously moving axially, removing material from the gear blank to create the gear teeth. The precise motion and synchronization between the hob and the gear blank result in accurate tooth profiles and proper tooth engagement.
VI. Finishing Operations:
After the gear teeth are generated, additional finishing operations may be performed to refine the gear’s surface finish and ensure optimal performance. These operations may include chamfering, deburring, and heat treatment processes. Chamfering involves cutting beveled edges on the gear teeth to facilitate smooth engagement with mating gears. Deburring removes any rough edges or burrs left from the cutting process. Heat treatment processes, such as carburizing or hardening, may be applied to enhance the gear’s durability and strength.
VII. Quality Control and Inspection:
Throughout the gear hobbing process, quality control and inspection play a crucial role. Regular measurements and inspections are conducted to verify the accuracy of the gear tooth profiles, tooth spacing, and other critical dimensions. This ensures that the final gears meet the required specifications. Advanced inspection tools, such as coordinate measuring machines (CMMs) and gear analyzers, are utilized to validate the gear’s dimensional accuracy and quality.
VIII. Post-Production Processes:
After the gears have undergone quality control inspection, they may undergo additional post-production processes. These processes can include surface treatments, such as grinding or polishing, to further enhance the gear’s surface finish. Gears may also be subjected to final inspections, packaging, and shipment to customers.
Gear hobbing is a comprehensive process that transforms gear design concepts into physical gear components. From the initial gear design and engineering stage to the actual gear hobbing operation and subsequent finishing processes, careful attention is given to every step to ensure the production of high-quality gears. By combining expertise in gear design, engineering, tooling, machine setup, and quality control, manufacturers can successfully bring gear concepts to life and deliver reliable and high-performance gears for various applications.