Precision forging techniques play a crucial role in achieving unparalleled accuracy in the production of metal components. With the advancement of manufacturing technology, various precision forging methods have emerged, each offering unique advantages in terms of accuracy, repeatability, and dimensional precision. This article explores some of the key precision forging techniques used to achieve exceptional accuracy in component production.
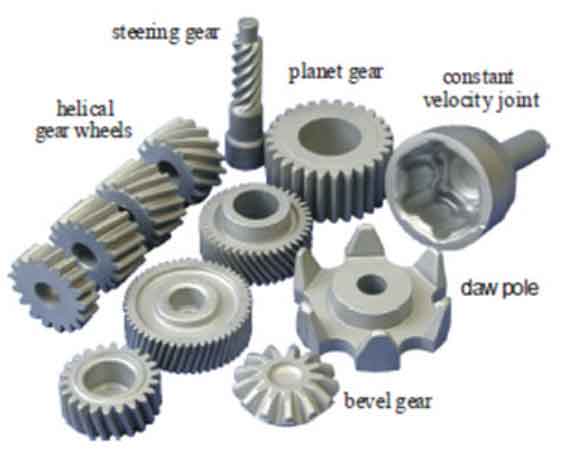
I. Closed-Die Forging:
Closed-die forging, also known as impression-die forging, is a widely used precision forging technique that involves the use of two or more dies to shape the metal into the desired form. The dies contain impressions or cavities that determine the final shape of the component. Closed-die forging offers precise control over dimensional accuracy, as the metal is completely enclosed within the dies, ensuring accurate shaping and consistency in every produced component. The closed-die forging process is suitable for manufacturing complex parts with high accuracy, such as gears, crankshafts, and connecting rods.
II. Precision Net Shape Forging:
Precision net shape forging is a technique that aims to achieve the final component shape with minimal or no machining requirements. In this process, the dies are carefully designed to eliminate or minimize the need for subsequent machining operations. By incorporating intricate details, undercuts, and close tolerances into the die design, precision net shape forging can produce components with exceptional accuracy directly from the forging process. This technique reduces material waste, manufacturing time, and costs associated with additional machining, while ensuring precise and repeatable component dimensions.
III. Near-Net Shape Forging:
Near-net shape forging is a technique that aims to forge the component as close to its final shape as possible, with minimal machining required. The dies used in near-net shape forging are designed to achieve the approximate dimensions and geometry of the final component, leaving only minimal excess material for machining. This technique offers improved accuracy and reduces the material and machining costs associated with achieving the final component shape. Near-net shape forging is commonly used in the production of complex components, such as turbine blades, where precision and dimensional accuracy are critical.
IV. Closed-Die Cold Forging:
Closed-die cold forging is a precision forging technique that involves shaping the metal at or near room temperature, as opposed to traditional hot forging. This process offers enhanced dimensional accuracy, as the metal experiences less thermal expansion and contraction during forging. Cold forging also provides better surface finish and closer tolerances due to reduced oxidation and scale formation. This technique is commonly used for small, intricate parts that require high precision, such as fasteners, electrical connectors, and precision components for the electronics industry.
V. Isothermal Forging:
Isothermal forging is a precision forging technique that involves forging the metal at a constant temperature, typically close to its recrystallization temperature. By maintaining a consistent temperature throughout the forging process, isothermal forging minimizes temperature-related variations and provides exceptional dimensional accuracy. The isothermal forging process is particularly advantageous for difficult-to-forge materials, such as titanium alloys and nickel-based superalloys, where precise control over temperature is crucial to avoid material defects and achieve accurate component dimensions.
Precision forging techniques offer the means to achieve unparalleled accuracy in component production. Whether through closed-die forging, precision net shape forging, near-net shape forging, closed-die cold forging, or isothermal forging, manufacturers can produce metal components with exceptional dimensional accuracy, repeatability, and surface finish. These techniques play a vital role in industries where precision and accuracy are paramount, such as aerospace, automotive, and medical sectors. By leveraging these precision forging techniques, manufacturers can meet the demanding requirements of modern applications and deliver high-quality components with unmatched accuracy.