Precision forging, as a critical manufacturing process, has been subject to continuous innovation and advancements that have driven significant progress in the manufacturing industry. These innovations have led to improved efficiency, enhanced quality, expanded capabilities, and the ability to meet the evolving demands of various industries. Some notable innovations in precision forging include:
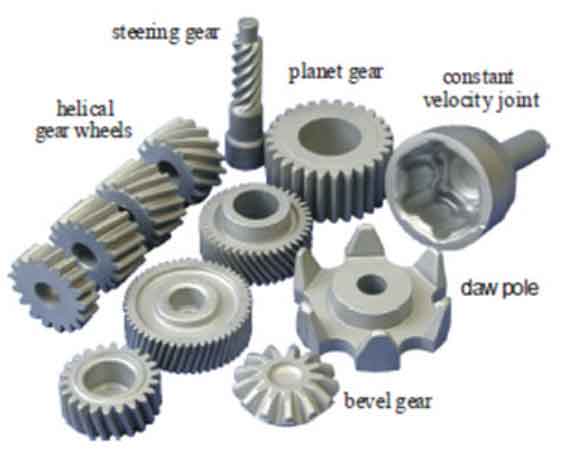
Advanced Materials:
Precision forging has witnessed advancements in the use of advanced materials, such as high-strength alloys, superalloys, and composite materials. These materials offer superior mechanical properties, increased temperature resistance, and reduced weight. Innovations in precision forging techniques have enabled the forging of these materials, opening up new possibilities for high-performance components.
Computational Modeling and Simulation:
The advent of computational modeling and simulation techniques has revolutionized precision forging. Finite element analysis (FEA) and computational fluid dynamics (CFD) simulations allow engineers to virtually simulate the forging process, predict material behavior, optimize die design, and identify potential defects. This saves time and cost by reducing the need for extensive physical trials and experiments.
Process Monitoring and Control:
Advanced sensing technologies and real-time process monitoring have improved the control and consistency of precision forging. Sensors embedded in the dies and tooling provide data on temperature, pressure, and deformation, enabling real-time adjustments to optimize the process and ensure consistent quality. Process control systems facilitate closed-loop feedback, minimizing variations and enhancing productivity.
Additive Manufacturing and Hybrid Processes:
The integration of precision forging with additive manufacturing (AM) has created hybrid processes that combine the strengths of both techniques. By leveraging AM for near-net shape preforms and precision forging for final shaping, manufacturers can achieve complex geometries, reduce material waste, and enhance material properties. This hybrid approach expands the design freedom and capabilities in precision forging.
Intelligent Automation and Robotics:
Automation and robotics have played a significant role in improving the efficiency and productivity of precision forging. Robotic systems are employed for material handling, die changing, and part extraction, reducing manual labor and increasing production rates. Intelligent automation systems incorporate artificial intelligence (AI) and machine learning algorithms to optimize process parameters, detect defects, and make real-time adjustments, enhancing overall process efficiency and quality control.
Energy Efficiency and Sustainability:
Innovations in precision forging have also focused on improving energy efficiency and reducing environmental impact. Advanced heating technologies, such as induction heating and energy recovery systems, minimize energy consumption during the forging process. Additionally, optimization of material usage, reduction of scrap, and implementation of sustainable manufacturing practices contribute to a more eco-friendly manufacturing approach.
Digitalization and Connectivity:
Digitalization and connectivity have transformed precision forging through the implementation of Industry 4.0 concepts. The integration of data analytics, cloud computing, and the Industrial Internet of Things (IIoT) enables real-time data collection, analysis, and remote monitoring of the forging process. This facilitates predictive maintenance, process optimization, and seamless communication across the production ecosystem, leading to improved efficiency, reduced downtime, and enhanced decision-making capabilities.
These innovations in precision forging have revolutionized the manufacturing industry by offering increased efficiency, improved quality, expanded design possibilities, and reduced environmental impact. They have enabled manufacturers to produce high-performance components with higher precision, faster production cycles, and enhanced material properties. As advancements continue, precision forging will continue to drive innovation and shape the future of manufacturing.