When it comes to gear cutting, two commonly used methods are gear hobbing and gear shaping. Both processes have their advantages and considerations, and the choice between them depends on several factors. Let’s compare gear hobbing and gear shaping to help you make an informed decision:
Gear Hobbing:
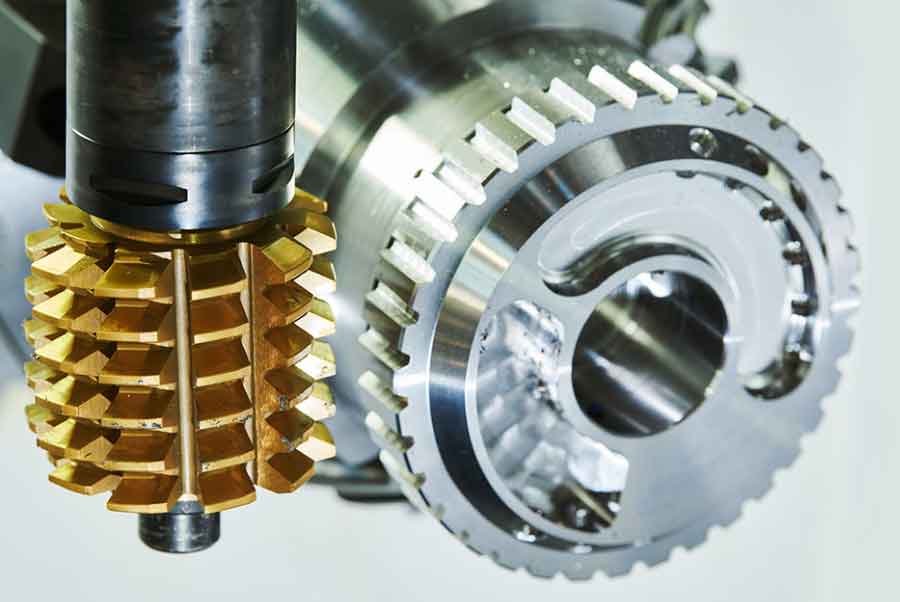
- Process Overview: Gear hobbing involves using a cutting tool called a hob that features multiple cutting edges. The hob rotates and cuts into the workpiece to generate the gear teeth. This process is suitable for producing a wide range of gear types, including spur gears, helical gears, worm gears, and bevel gears.
- Tooth Profile Accuracy: Gear hobbing provides excellent tooth profile accuracy. The hob’s design ensures precise tooth geometry, resulting in accurate tooth profiles and consistent tooth spacing. The gear teeth produced by gear hobbing exhibit high precision, ensuring smooth and efficient gear meshing.
- Surface Finish: Gear hobbing typically produces gears with a good surface finish. The continuous cutting action of the hob creates a smooth gear surface, reducing friction and wear. However, the surface finish achieved in gear hobbing may not be as fine as that achieved in gear shaping.
- Efficiency and Productivity: Gear hobbing is generally a faster process compared to gear shaping. The continuous rotary motion of the hob and synchronized rotation of the workpiece allow for efficient material removal, resulting in higher productivity for large production runs.
- Flexibility: Gear hobbing offers more versatility in terms of gear types and sizes. It can produce a wide range of gear configurations and accommodate various gear sizes, making it suitable for different applications.
Gear Shaping:
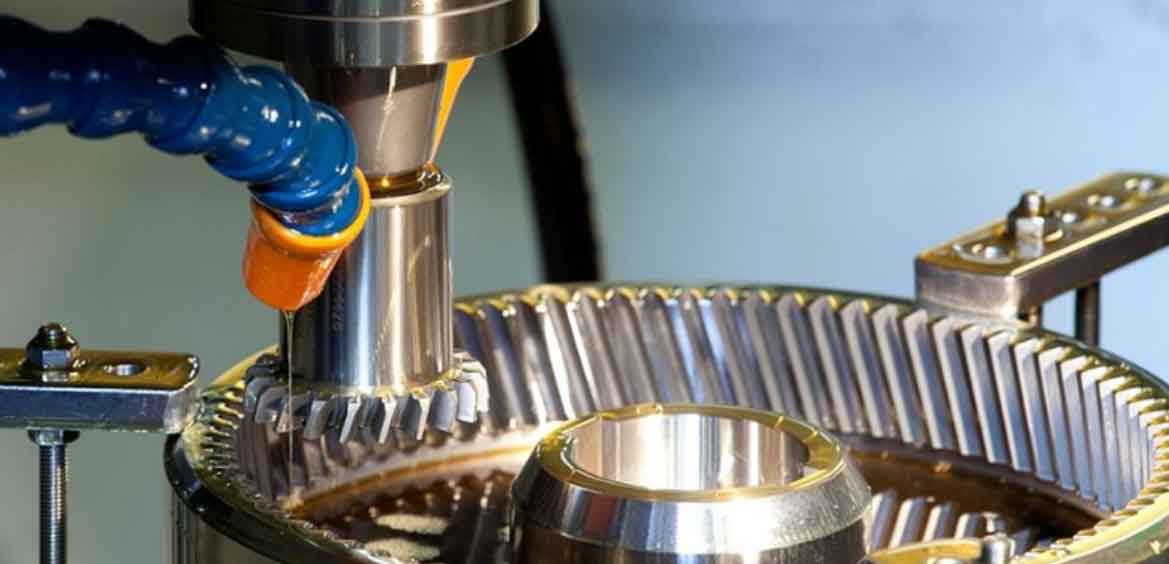
- Process Overview: Gear shaping involves using a cutting tool called a shaper cutter that moves in a reciprocating motion to cut the gear teeth. The workpiece rotates while the shaper cutter generates the tooth profiles. Gear shaping is primarily used for producing spur gears and internal gears.
- Tooth Profile Accuracy: Gear shaping provides excellent tooth profile accuracy, often surpassing the accuracy achieved in gear hobbing. The reciprocating motion of the shaper cutter allows for more controlled tooth formation, resulting in precise tooth profiles and consistent tooth spacing.
- Surface Finish: Gear shaping typically produces gears with a finer surface finish compared to gear hobbing. The back-and-forth motion of the shaper cutter creates smoother gear surfaces with reduced surface roughness.
- Flexibility: Gear shaping is generally more limited in terms of gear types and sizes. It is primarily used for producing spur gears and internal gears. While it can accommodate different gear sizes, gear shaping may have some limitations when it comes to gear configurations compared to gear hobbing.
- Process Complexity: Gear shaping is considered a more complex process than gear hobbing. It requires precise setup and alignment of the workpiece and cutter, which may require additional expertise and setup time.
Factors to Consider when Choosing between Gear Hobbing and Gear Shaping:
- Gear type and complexity: Consider the specific gear type and configuration required for your application. Gear hobbing is more versatile in producing various gear types, while gear shaping is more suitable for spur gears and internal gears.
- Accuracy requirements: Evaluate the desired tooth profile accuracy and surface finish for your gears. Gear shaping generally offers higher precision and surface finish.
- Production volume: Consider the production volume needed. Gear hobbing is typically faster and more suitable for large production runs, while gear shaping can be more time-consuming for high volumes.
- Equipment availability and expertise: Assess the availability of gear hobbing and gear shaping machines and the expertise of your team in operating and maintaining them.
In summary, gear hobbing is a versatile process suitable for a wide range of gear types and sizes, providing good tooth profile accuracy and efficiency. Gear shaping excels in achieving high tooth profile accuracy, fine surface finish, and is well-suited for spur gears and internal gears. Consider the specific requirements of your gear design, production volume, and available equipment to make the right choice between gear hobbing and gear shaping.