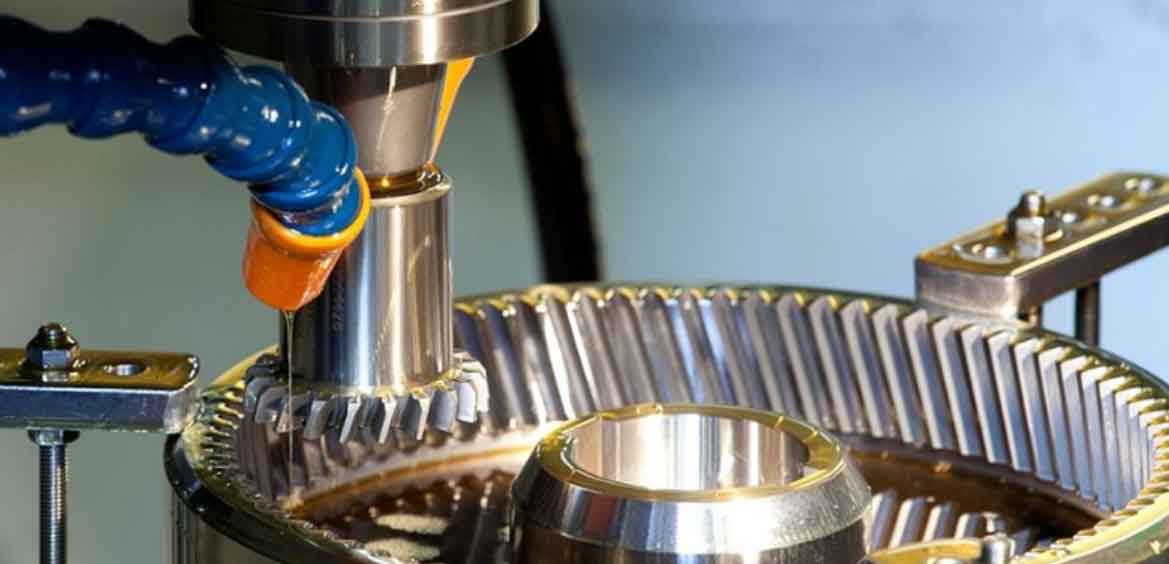
Gear shaping is a widely used gear cutting method that offers precise control over tooth geometry and delivers high-quality gears. However, like any manufacturing process, gear shaping also presents certain challenges. By understanding these challenges and implementing appropriate measures, it is possible to tackle them effectively and ensure the quality of gear production. Here are some key challenges in gear shaping and strategies to overcome them:
- Tool Wear: During the gear shaping process, the shaper cutter undergoes continuous contact with the workpiece, resulting in tool wear over time. This wear can affect the accuracy of tooth profile and surface finish. To address this challenge:
- Regularly inspect and measure the tool to monitor wear and maintain its sharpness.
- Implement preventive maintenance schedules to recondition or replace worn tools.
- Optimize cutting parameters, such as cutting speed and feed rate, to minimize tool wear.
- Chatter and Vibration: Chatter and vibration can occur during gear shaping, leading to poor surface finish, inaccuracies in tooth geometry, and increased tool wear. To minimize chatter and vibration:
- Ensure the gear shaping machine is properly maintained, with good alignment and rigidity.
- Optimize cutting parameters, such as feed rate and depth of cut, to minimize vibrations.
- Use appropriate cutting fluids or lubricants to reduce friction and dissipate heat.
- Tooling and Fixture Design: Designing and manufacturing the shaper cutter and workpiece fixture are critical for achieving accurate gear shaping. Consider the following:
- Collaborate with tooling suppliers or manufacturers with expertise in gear shaping to develop suitable shaper cutters.
- Design and fabricate workpiece fixtures that securely hold the gear blank and provide proper support during the shaping process.
- Verify the dimensional and geometric accuracy of the tooling and fixtures before production.
- Material Selection: The choice of material for the gear blank can impact the gear shaping process and the resulting gear quality. Factors to consider include material hardness, machinability, and heat treatment requirements. Ensure:
- Select materials that are suitable for gear shaping and can achieve the desired gear performance.
- Optimize heat treatment processes to achieve the desired material properties and minimize distortion or residual stresses.
- Gear Design and Tolerance Considerations: Gear shaping is influenced by factors such as tooth profile, module, pressure angle, and tolerances. To ensure quality:
- Ensure the gear design is suitable for gear shaping, considering factors such as cutter geometry and machine capabilities.
- Establish appropriate tolerance specifications for tooth profile, runout, and other critical dimensions.
- Perform regular inspections and measurements during the production process to verify compliance with design specifications.
- Quality Control and Inspection: Implementing effective quality control measures is crucial to ensuring the accuracy and reliability of the produced gears. Consider:
- Conducting in-process inspections to monitor gear dimensions and surface finish during shaping.
- Performing post-process inspections using coordinate measuring machines (CMMs), gear checkers, or other appropriate metrology equipment.
- Establishing quality control plans and protocols to identify and address any non-conformities or deviations promptly.
- Operator Training and Expertise: Gear shaping requires skilled operators who understand the process, equipment, and quality requirements. Ensure:
- Provide comprehensive training programs for gear shaping operators to develop their skills and knowledge.
- Encourage continuous learning and knowledge sharing among the production team.
- Foster a culture of quality and attention to detail to ensure consistent and reliable gear production.
By addressing these challenges, implementing appropriate measures, and continually improving processes, gear shaping can deliver high-quality gears with precise tooth profiles and excellent surface finish. Collaboration between gear manufacturers, tooling suppliers, and equipment manufacturers is crucial to overcoming challenges and achieving optimal gear shaping results.