Forged gear blanks play a crucial role as the foundation of reliable and high-performance gears in various applications. Here are some key aspects to consider when it comes to forged gear blanks:
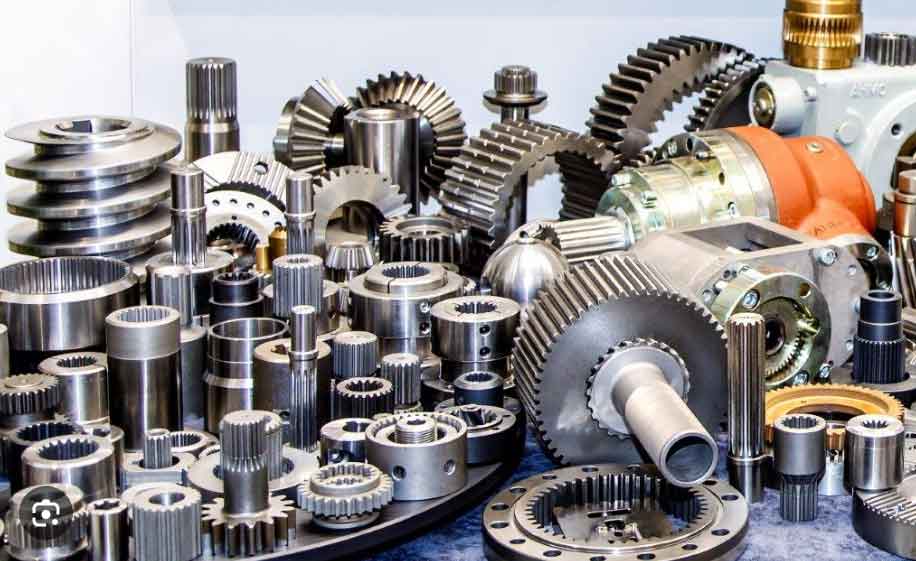
- Material Strength and Durability: Forged gear blanks are typically made from high-strength alloy steels or specialized materials that offer excellent mechanical properties. The forging process enhances the material’s strength, durability, and resistance to fatigue, ensuring the gear can withstand heavy loads and prolonged operation without failure.
- Uniform Grain Structure: During the forging process, the metal undergoes controlled deformation under high pressure and temperature, resulting in a refined and uniform grain structure. This grain structure provides superior mechanical properties, such as improved strength, toughness, and resistance to cracking or deformation. It enhances the overall reliability and performance of the gear.
- Customizable Design: Forged gear blanks can be produced in a wide range of sizes, shapes, and configurations to meet specific application requirements. The flexibility of the forging process allows for the creation of complex gear geometries with precision. Customizable design options ensure that the forged gear blanks can be tailored to fit specific gear systems and optimize their performance.
- Consistency and Quality Control: Forged gear blanks offer excellent consistency and uniformity in terms of material properties and dimensions. The forging process allows for precise control over the manufacturing parameters, resulting in consistent quality across production batches. This consistency ensures the gears can be accurately machined and assembled, leading to reliable and efficient gear systems.
- Reduced Material Waste: Forging is a near-net shape manufacturing process, which means that the gear blank is formed as close to its final shape as possible. This results in minimal material waste compared to other manufacturing methods, such as machining from solid stock. The reduced material waste not only contributes to cost savings but also minimizes the environmental impact of gear production.
- Cost-Effectiveness: While the initial investment for forging equipment and tooling may be higher, the cost-effectiveness of forged gear blanks becomes apparent in the long run. The superior mechanical properties and durability of forged gears lead to extended service life, reduced downtime, and lower maintenance costs compared to gears made from other manufacturing methods.
Forged gear blanks serve as the foundation for reliable and high-performance gears in various industries, including automotive, aerospace, heavy machinery, and more. Their superior strength, durability, and customization options make them an ideal choice for demanding applications where efficiency and reliability are critical.