Forging precision is a critical aspect of producing gear blanks with tight tolerances. While forging offers several advantages in terms of strength and material properties, achieving tight tolerances requires careful consideration of various factors throughout the forging process. Here are some key points to consider when aiming for tight tolerances with forged gear blanks:
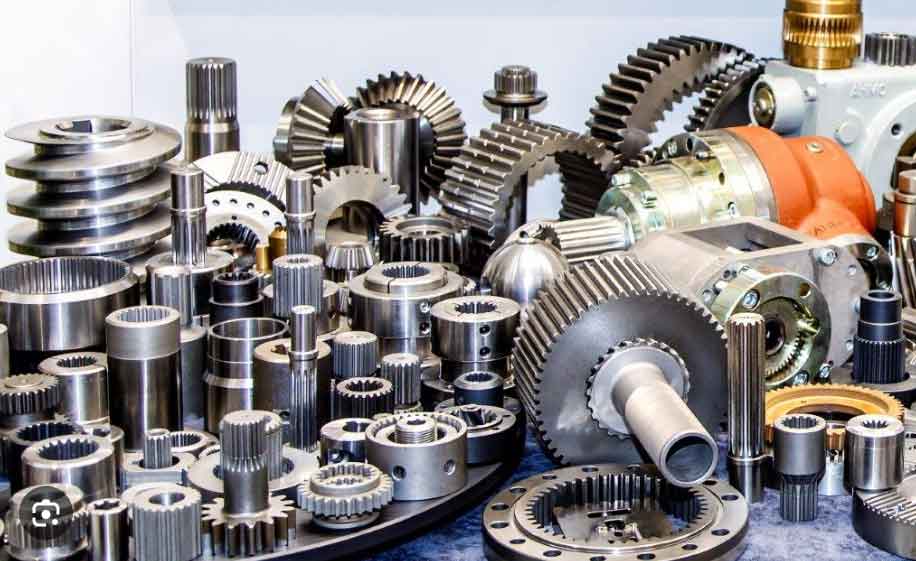
- Material Selection: Choosing the right material is crucial for achieving tight tolerances. Select a material that exhibits good forgeability and dimensional stability. Material properties such as low carbon content, uniform grain structure, and minimal alloy segregation can contribute to tighter tolerances.
- Die Design and Maintenance: Well-designed forging dies are essential for maintaining precision. The dies should be accurately machined to match the desired gear blank dimensions. Regular maintenance and inspection of the dies help prevent wear and deformation, ensuring consistent dimensional accuracy.
- Billet Preparation: The initial billet preparation is critical. The billet should be carefully machined to provide a precise starting point for the forging process. Accurate dimensions and surface finish of the billet contribute to achieving tight tolerances in the final gear blank.
- Process Control: Maintaining tight process controls during forging is essential. Factors such as temperature, strain rate, and forging pressure must be closely monitored and controlled. Consistent process parameters ensure uniform deformation and help minimize dimensional variations.
- Heat Treatment: Proper heat treatment can enhance the dimensional stability of forged gear blanks. Controlled heating and cooling processes, such as quenching and tempering, can minimize distortion and maintain tight tolerances. Heat treatment should be optimized based on the material properties and the desired final hardness of the gears.
- Machining Allowances: Consider the machining allowances required to achieve the final gear dimensions. Forging can help reduce the amount of material that needs to be removed during machining, minimizing dimensional variations and improving cost-effectiveness.
- Inspection and Quality Control: Implement a robust inspection and quality control process throughout the forging operation. Utilize techniques such as dimensional measurement, non-destructive testing, and visual inspection to identify any deviations from the desired tolerances. Feedback from inspections can help optimize the forging process and improve future productions.
- Continuous Improvement: Strive for continuous improvement in the forging process. Analyze any deviations or non-conformities and implement corrective actions to address them. Regularly review and update process parameters, tooling, and material selection based on lessons learned from previous productions.
By focusing on these key considerations and implementing stringent quality control measures, it is possible to achieve tight tolerances with forged gear blanks. Precise forging processes result in gear blanks that meet the required dimensional specifications, ensuring high-quality finished gears for various applications.