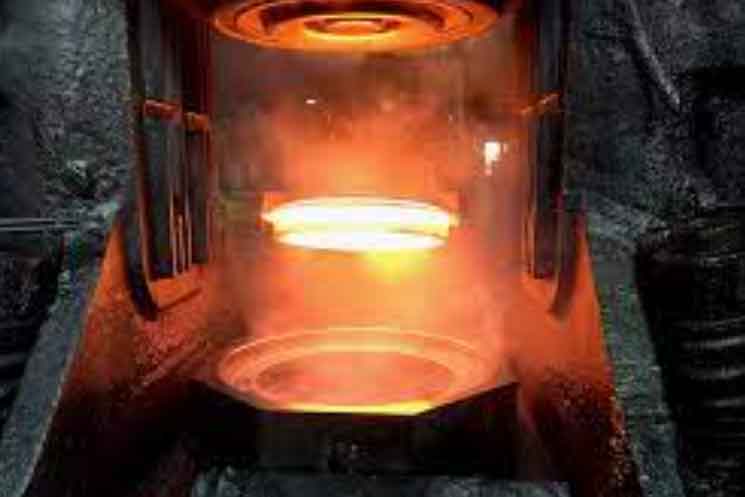
Gear forgings are an essential part of the manufacturing process for high-performance gear solutions. They involve the transformation of raw materials into strong, durable, and precisely engineered gears that can withstand heavy loads, high speeds, and demanding operating conditions. Let’s explore the journey of gear forgings from raw material to the final product.
- Raw Material Selection: The first step in gear forging is the careful selection of raw materials. Common materials used for gear forgings include alloy steels, stainless steels, carbon steels, and other specialized alloys. The choice of material depends on the specific application, considering factors such as strength, wear resistance, and heat resistance.
- Heating and Billet Preparation: The selected raw material, typically in the form of billets or ingots, is heated to a specific temperature in a furnace. Heating is crucial to improve the material’s plasticity and facilitate the forging process. The billets are then prepared by cutting or cropping them to the desired size and shape, ensuring they are suitable for subsequent forging operations.
- Preforming: In the preforming stage, the billets are subjected to preliminary shaping through various processes such as rolling, upsetting, or extrusion. This step helps create a starting point for the subsequent forging operations and reduces the overall material volume.
- Die Preparation: Forging dies, also known as tooling, are prepared to shape the billets accurately. Dies are typically made of high-strength tool steels and are precision machined to the required gear profile. The die design takes into account factors such as tooth geometry, tolerances, and allowances for subsequent machining.
- Hot Forging: Hot forging is the primary forging process used for gear manufacturing. The preheated billets are placed between the prepared dies, and high-pressure forces are applied to shape the material into the desired gear profile. The forging process typically involves multiple steps, with intermediate annealing if necessary, to optimize material properties and control grain structure.
- Heat Treatment: After the hot forging process, the gears undergo heat treatment to enhance their mechanical properties. Common heat treatment methods include quenching, tempering, carburizing, and nitriding. Heat treatment helps improve the gear’s strength, hardness, and wear resistance, ensuring it can withstand the expected loads and operating conditions.
- Machining: Although gear forgings provide a near-net shape, they often require machining operations for final finishing. Machining processes such as turning, milling, grinding, and hobbing are employed to achieve precise dimensions, gear tooth profiles, and surface finishes. CNC (Computer Numerical Control) machines are commonly used to ensure accuracy and repeatability.
- Quality Control and Testing: Throughout the forging and machining processes, various quality control measures are implemented to ensure the gears meet the required specifications. Non-destructive testing methods such as ultrasonic testing and magnetic particle inspection are used to detect any internal or surface defects. Dimensional inspections, hardness testing, and metallurgical analysis are also conducted to verify the gear’s quality and performance.
- Surface Treatment and Finishing: To enhance the gear’s surface properties and protect against corrosion, additional surface treatments may be applied. This can include processes such as shot peening, coating, plating, or polishing, depending on the specific requirements of the gear application.
- Final Inspection and Packaging: Once the gear forgings have passed all quality control checks and finishing processes, they undergo a final inspection to ensure compliance with customer specifications. The gears are then carefully packaged to protect them during transportation and storage, ready to be delivered to the customers.
Gear forgings undergo a series of precise and controlled manufacturing steps, from raw material selection to final inspection and packaging. This meticulous process ensures the production of high-performance gear solutions that can meet the demanding requirements of various industries, including automotive, aerospace, power generation, and heavy machinery.