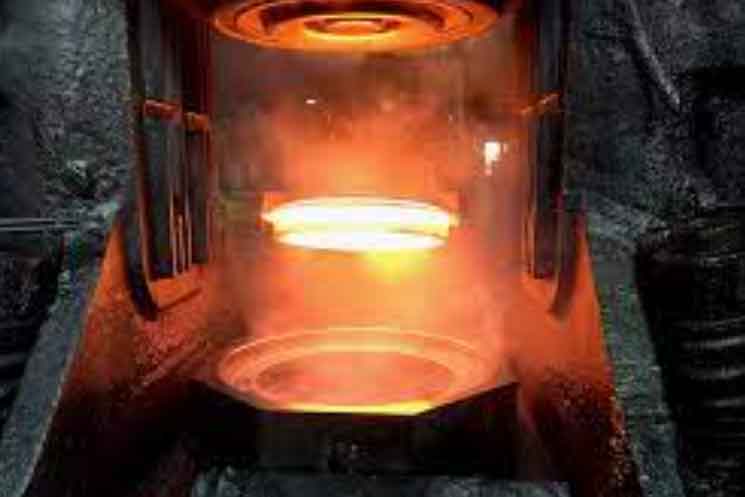
Gear forgings are instrumental in unleashing the potential of high-strength gear solutions, offering a range of benefits that contribute to improved performance and durability in various applications. Let’s delve into how gear forgings unlock the potential of high-strength gear solutions:
Superior Strength and Load-Carrying Capacity:
Gear forgings are renowned for their exceptional strength. The forging process involves subjecting the metal to high compressive forces, which align the grain structure and eliminate defects. This results in gear components with superior strength and load-carrying capacity, allowing them to withstand heavy loads and high torque without failure. The enhanced strength of gear forgings enables the use of smaller, lighter gears that can transmit greater power while reducing weight and space requirements.
Enhanced Fatigue Resistance:
Fatigue failure is a common concern in gear applications due to the cyclic loading they experience. Gear forgings offer enhanced fatigue resistance, thanks to their refined grain structure and optimized material properties. The controlled deformation during forging aligns the grain flow, reducing stress concentrations and enhancing the gear’s ability to resist fatigue-induced cracks and failures. This ensures a longer service life and increased reliability, particularly in applications with high-speed or continuous-duty requirements.
Improved Wear and Abrasion Resistance:
Gears operating in demanding environments often face challenges such as abrasive particles, contaminants, and high contact pressures. Gear forgings exhibit excellent wear and abrasion resistance, allowing them to withstand these harsh conditions. The forging process refines the grain structure, eliminating defects and enhancing the gear’s resistance to wear, pitting, and surface damage. This extends the gear’s lifespan, reduces maintenance needs, and ensures consistent performance over time.
Optimized Metallurgical Properties:
Gear forgings undergo heat treatment processes such as quenching and tempering, which optimize their metallurgical properties. Heat treatment refines the microstructure, increasing hardness and strength while maintaining appropriate toughness. This results in gear components with superior mechanical properties tailored to withstand specific operating conditions. By optimizing the metallurgical properties, gear forgings achieve the desired combination of strength, toughness, and hardness necessary for high-strength gear solutions.
Reduced Size and Weight:
The inherent strength of gear forgings allows for the design and production of gears with reduced size and weight. With higher strength-to-weight ratios, forged gears enable engineers to develop compact and lightweight systems without compromising performance or reliability. This is particularly beneficial in industries such as aerospace, automotive, and robotics, where weight reduction is critical for fuel efficiency, maneuverability, and overall system optimization.
Reliable Performance in Extreme Conditions:
High-strength gear solutions are often required in applications involving extreme operating conditions such as high temperatures, corrosive environments, or intense vibrations. Gear forgings, with their superior strength, enhanced fatigue resistance, and optimized metallurgical properties, offer reliable performance in such challenging conditions. They maintain dimensional stability, tooth profile integrity, and overall gear functionality, ensuring smooth and efficient operation even in the harshest environments.
Gear forgings unleash the potential of high-strength gear solutions by providing superior strength, enhanced fatigue resistance, improved wear and abrasion resistance, and optimized metallurgical properties. The combination of these benefits allows gear manufacturers to develop robust, reliable, and high-performing gear systems for various industries and applications. By leveraging gear forgings, engineers can unlock new possibilities in terms of load capacity, efficiency, and system optimization, ultimately enhancing productivity and reliability in gear-driven machinery.