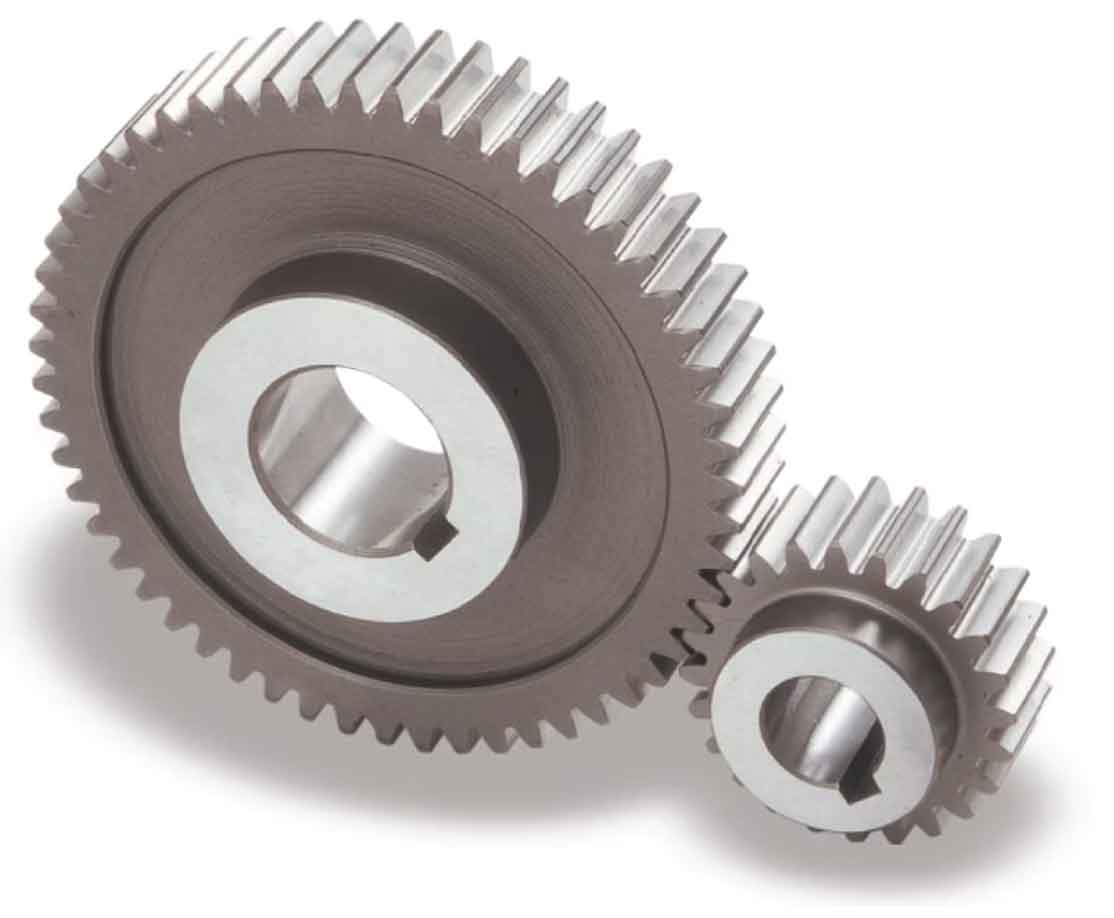
Proper installation and maintenance are essential for the optimal performance and longevity of spur gears. Here are some practical tips to consider:
Installation:
- Preparation: Before installation, thoroughly clean the gear system components, ensuring that they are free from dirt, debris, and residual lubricants. Inspect the gears for any signs of damage or wear.
- Alignment: Ensure proper alignment of the gears by accurately positioning them both axially and radially. Misalignment can result in increased noise, vibration, and premature wear. Follow manufacturer guidelines for alignment tolerances.
- Shaft Alignment: Proper alignment of the shafts that support the gears is crucial. Use alignment tools, such as dial indicators or laser alignment systems, to achieve accurate shaft alignment and minimize angular and parallel misalignment.
- Bearing Installation: Install the bearings properly, following manufacturer instructions. Ensure correct bearing type, size, and lubrication. Pay attention to bearing clearance, preload, and proper seating on the shafts or housings.
- Lubrication: Apply the recommended lubricant to the gears and bearings according to manufacturer specifications. Ensure even and adequate lubrication throughout the gear system. Avoid over-lubrication, as it can cause overheating and drag.
- Torque Application: Follow the specified torque values when tightening bolts, fasteners, or couplings in the gear system. Over-tightening can lead to deformation or damage, while under-tightening may result in loose components and misalignment.
- Run-In Period: After installation, allow a run-in period for the gear system to settle and adjust. This period helps the gears and bearings adapt to their operating conditions, minimizing the risk of premature wear or failure.
Maintenance:
- Regular Inspections: Perform routine visual inspections of the gear system to detect any signs of wear, damage, or misalignment. Check for abnormal noise, vibration, or leakage. Inspect gears, bearings, seals, and lubrication conditions.
- Lubricant Monitoring: Monitor the condition of the lubricant regularly. Check for contamination, degradation, or insufficient levels. Perform oil analysis to assess viscosity, particle contamination, and lubricant condition. Change the lubricant as recommended by the manufacturer.
- Gear Meshing Inspection: Periodically inspect the gear meshing to ensure proper tooth engagement and alignment. Check for abnormal wear patterns, scoring, pitting, or tooth damage. Address any issues promptly to prevent further damage.
- Bearing Maintenance: Pay attention to bearing performance and conditions. Monitor for excessive noise, vibration, or temperature. Regularly lubricate bearings as per manufacturer recommendations. Replace bearings when signs of wear or damage are observed.
- Sealing and Protection: Ensure proper sealing and protection of the gear system against contaminants, moisture, and environmental factors. Replace damaged or worn seals and gaskets. Keep the gear housing clean and free from debris.
- Temperature Monitoring: Monitor the operating temperature of the gear system. Abnormal temperature increases can indicate issues such as overloading, insufficient lubrication, or misalignment. Address temperature abnormalities promptly to avoid gear system failure.
- Maintenance Records: Maintain comprehensive records of maintenance activities, inspections, and repairs performed on the gear system. This information helps track the gear system’s history, identify recurring issues, and plan maintenance tasks effectively.
- Professional Assistance: If you encounter complex issues or challenges during installation or maintenance, consider seeking assistance from qualified gear engineers or technicians. Their expertise can help diagnose and address problems effectively.
By following these practical tips for installation and maintenance, you can ensure the proper functioning, reliability, and longevity of your spur gear system. Regular inspections and timely maintenance are crucial for identifying and addressing issues before they escalate and lead to more significant problems.