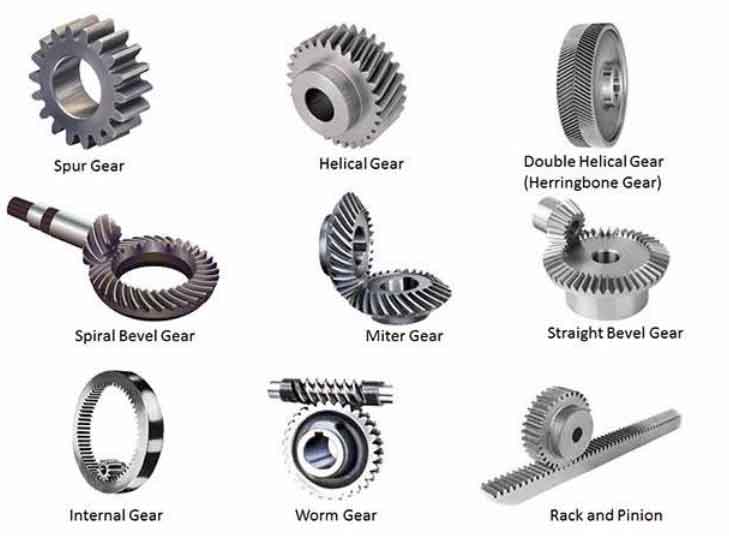
When considering the choice between hypoid gears and helical gears, it’s important to assess the specific requirements and characteristics of each gear type. Here’s a comparison to help you select the right gear type for your application:
Hypoid Gears:
- Advantages:
- High torque capacity: Hypoid gears can handle higher torque levels compared to helical gears.
- Compact design: Hypoid gears feature offset axes, allowing for more flexibility in space-constrained applications.
- Smooth and quiet operation: The sliding action of hypoid gears reduces noise and vibration.
- Versatile shaft configurations: Hypoid gears can accommodate non-parallel and non-intersecting shaft orientations.
- Considerations:
- Complex design: Hypoid gears have a more intricate tooth profile and manufacturing process compared to helical gears.
- Higher cost: The complexity of hypoid gears can result in higher production costs.
Helical Gears:
- Advantages:
- High torque capacity: Helical gears have good torque-carrying capability.
- Smooth operation: The helical tooth profile provides gradual tooth engagement, resulting in reduced noise and vibration compared to spur gears.
- Overlapping teeth: The overlapping contact between helical gears allows for improved load distribution and higher contact ratios.
- Considerations:
- Axial thrust: Helical gears produce an axial thrust force that must be considered and properly managed.
- More complex manufacturing: The helical gear manufacturing process is more involved than spur gears but less complex than hypoid gears.
- Limited shaft configurations: Helical gears are primarily suitable for parallel and intersecting shaft configurations.
Choosing the right gear type depends on various factors, including torque requirements, space constraints, noise limitations, and the specific application environment. If you require high torque capacity, smooth operation, and versatility in shaft configurations, hypoid gears may be the better choice. However, if you prioritize smooth operation, good torque capacity, and overlapping tooth contact, helical gears can be a suitable option.
It is recommended to consult with a mechanical engineer or gear specialist who can analyze your specific application requirements and provide guidance on the most appropriate gear type. They can consider factors such as torque, speed, noise considerations, and spatial constraints to ensure optimal gear performance and reliability.