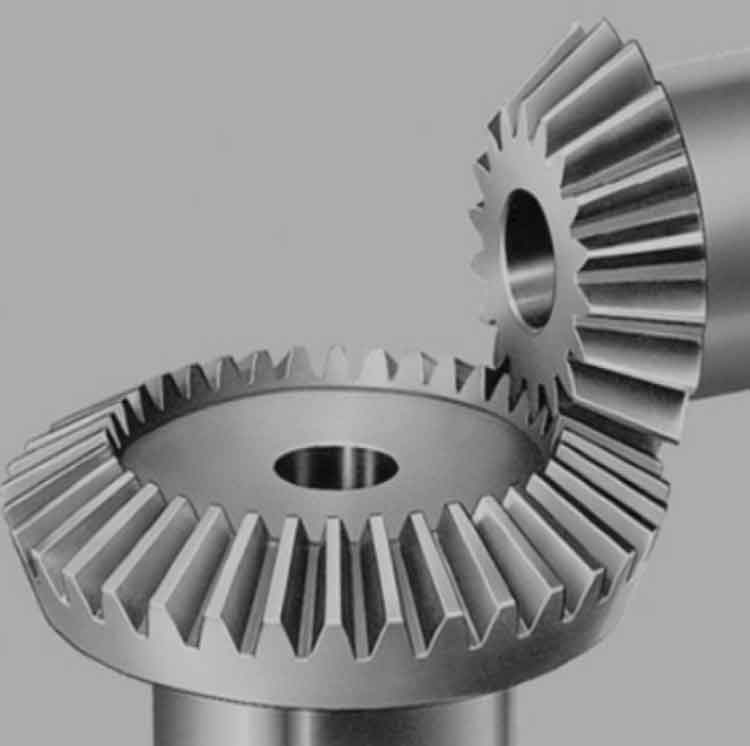
Designing and manufacturing straight bevel gears can present various challenges, but with careful consideration and appropriate techniques, these challenges can be overcome. Here are some common challenges in the design and manufacturing of straight bevel gears and potential solutions:
- Complex Tooth Geometry: The tooth profile of straight bevel gears is more complex compared to other gear types. It requires precise calculations and design considerations to ensure proper tooth engagement and load distribution. Computer-aided design (CAD) software and advanced simulation tools can help in accurately designing the tooth geometry and optimizing the gear performance.
- Precision Machining: Achieving the required tooth profile and surface finish on straight bevel gears requires high-precision machining processes. CNC (Computer Numerical Control) machining, gear hobbing, or gear shaping techniques can be employed to achieve the desired accuracy and surface quality. Maintaining tight tolerances and using advanced machining tools and techniques can help overcome precision challenges.
- Gear Alignment and Assembly: Proper alignment and assembly of straight bevel gears are critical for ensuring smooth and efficient gear operation. The accurate positioning and alignment of gears during assembly are essential to minimize misalignment and ensure proper tooth engagement. Utilizing specialized alignment tools and fixtures, as well as following precise assembly procedures, can help overcome alignment challenges.
- Heat Treatment and Material Selection: Straight bevel gears often require heat treatment to enhance their hardness, strength, and durability. However, the heat treatment process can introduce dimensional changes and distortions, affecting the gear’s performance. Proper material selection and careful control of the heat treatment process can help mitigate these challenges and ensure consistent gear quality.
- Backlash Control: Controlling backlash, which is the clearance between the meshing teeth, is crucial in straight bevel gears. Excessive backlash can lead to noise, vibration, and reduced efficiency. Employing proper gear design techniques, such as appropriate tooth profile modifications and optimized manufacturing processes, can help minimize backlash and ensure smooth gear operation.
- Surface Finish and Tooth Quality: Achieving the required surface finish and tooth quality on straight bevel gears is important for reducing friction, wear, and noise. Careful selection of cutting tools, grinding processes, and post-machining operations can help achieve the desired surface finish and tooth quality. Quality control measures, such as inspection and testing methods, should be employed to ensure compliance with specified gear requirements.
- Efficient Gear Inspection: Straight bevel gears require thorough inspection to ensure their dimensional accuracy, tooth profile, and overall quality. Utilizing advanced gear inspection equipment, such as coordinate measuring machines (CMMs) and gear analyzers, can facilitate accurate and efficient gear inspection, reducing manufacturing challenges and ensuring gear conformance.
By addressing these challenges through advanced design techniques, precise manufacturing processes, and quality control measures, the design and production of straight bevel gears can be successfully accomplished, resulting in reliable and high-performance gear systems.