Hypoid gears have a unique tooth profile that combines elements of both spiral bevel gears and worm gears. The tooth geometry of hypoid gears is characterized by its curvature and asymmetry, which allows for efficient power transmission and torque transfer. Here’s a closer look at the tooth profiles of hypoid gears:
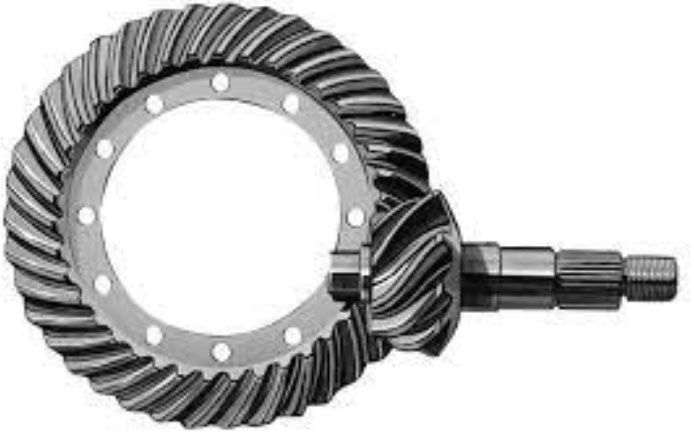
- Hypoid Offset: The most distinctive feature of hypoid gears is the offset between the gear axis and the pinion axis. This offset creates an angled, or hypoid, shape for the gear teeth. The amount of offset is referred to as the hypoid offset or hypoid distance.
- Curved Tooth Profile: The tooth profile of hypoid gears is curved, with a radius that varies along the tooth height. The curvature of the tooth profile enables a gradual transition of contact between the gear teeth, resulting in smoother operation and reduced stress concentration compared to straight-tooth bevel gears.
- Spiral Element: In addition to the curved shape, hypoid gears also incorporate a spiral element into their tooth profile. The spiral angle represents the angle between the tooth trace and a plane perpendicular to the gear axis. The spiral angle can vary along the tooth height, allowing for optimal contact and load distribution.
- Asymmetry: Hypoid gears exhibit an asymmetrical tooth profile. The tooth thickness and shape on one side of the gear are different from the other side. This asymmetry compensates for the hypoid offset and ensures proper meshing and load distribution between the gear and pinion.
The complex tooth geometry of hypoid gears requires precise design and manufacturing techniques. Computer-aided design (CAD) software and specialized gear design tools are used to calculate the tooth profiles, considering factors such as the gear ratio, hypoid offset, spiral angle, and tooth contact patterns. Advanced manufacturing processes, such as CNC machining and grinding, ensure accurate reproduction of the tooth profiles.
The unique tooth profiles of hypoid gears contribute to their high torque capacity, smooth operation, and improved power transmission efficiency. They are particularly well-suited for applications where compact design, high torque, and efficient power transfer are required, such as automotive drivetrains, heavy machinery, and industrial gearboxes.
It’s important to note that the design and manufacturing of hypoid gears require specialized knowledge and expertise. Working with experienced gear engineers and manufacturers is crucial to ensure the proper design, precision manufacturing, and performance of hypoid gears in specific applications.