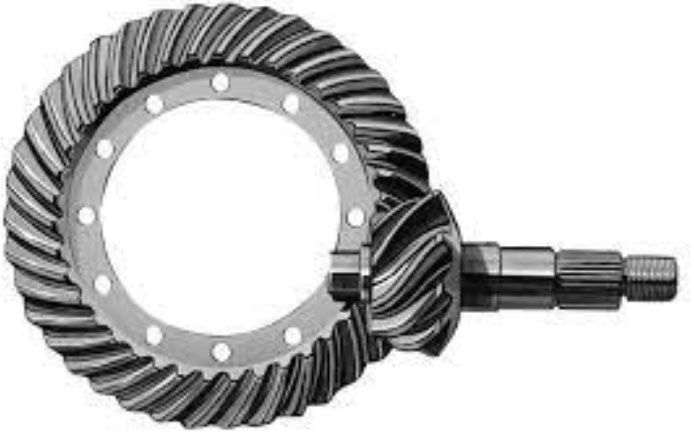
Manufacturing hypoid gears involves specific techniques, challenges, and solutions to ensure their precise and efficient production. Here are some key aspects of manufacturing hypoid gears:
- Gear Design and Engineering: Hypoid gears require careful design and engineering to determine the appropriate tooth geometry, gear ratio, backlash, and contact pattern. Computer-aided design (CAD) and computer-aided manufacturing (CAM) software are often used to create 3D models and simulate the gear meshing process.
- Gear Cutting Methods: Hypoid gears are typically manufactured using specialized gear cutting methods such as face milling, face hobbing, or face grinding. These methods involve precise cutting or grinding of the gear teeth to achieve the desired tooth geometry and surface finish. Gear cutting machines with multi-axis capabilities are commonly employed to accurately produce the complex hypoid gear shapes.
- Gear Tooth Surface Treatment: After the gear teeth are cut, additional surface treatment processes may be applied to improve their durability, such as case hardening, shot peening, or surface coating. These treatments enhance the wear resistance, strength, and performance of the gear teeth under load.
- Gear Inspection and Quality Control: Hypoid gears undergo rigorous inspection and quality control measures to ensure their dimensional accuracy, tooth profile integrity, and overall quality. Various inspection techniques such as coordinate measuring machines (CMM), gear analyzers, and inspection gauges are utilized to verify the gear’s dimensional and functional characteristics.
- Tooling and Fixture Design: Specialized tooling and fixtures are required to accurately position and support the gear during the manufacturing process. These fixtures are designed to accommodate the unique shape and orientation of hypoid gears, ensuring precise alignment and minimizing errors.
- Precision Machining and Assembly: The machining and assembly processes for hypoid gears demand high precision to maintain the desired tooth contact pattern and gear performance. Advanced machining techniques, such as high-speed machining and multi-axis CNC machining, are employed to achieve tight tolerances and surface finish requirements.
Challenges that arise during the manufacturing of hypoid gears include:
- Complex Tooth Geometry: The complex tooth geometry of hypoid gears presents challenges in terms of accurate manufacturing and alignment. Precise control of gear tooth profiles, pitch angles, and tooth contact patterns is essential to ensure optimal performance.
- Tight Tolerances: Hypoid gears often require tight manufacturing tolerances to maintain the desired tooth contact and backlash characteristics. Achieving these tight tolerances requires careful control of the machining processes and accurate measurement techniques.
- Specialized Equipment and Expertise: Manufacturing hypoid gears requires specialized equipment and expertise due to their unique geometry and manufacturing requirements. The availability of skilled technicians, advanced gear cutting machines, and inspection tools is crucial to achieve high-quality hypoid gears.
Solutions to these challenges involve advanced manufacturing technologies, improved cutting tools, precision machining techniques, and rigorous quality control processes. Additionally, ongoing research and development efforts focus on optimizing manufacturing processes, enhancing gear design software, and improving the accuracy and efficiency of gear cutting machines.
Manufacturers of hypoid gears collaborate closely with automotive and industrial customers to understand their specific requirements, ensuring that the gears meet the desired performance, durability, and reliability standards.