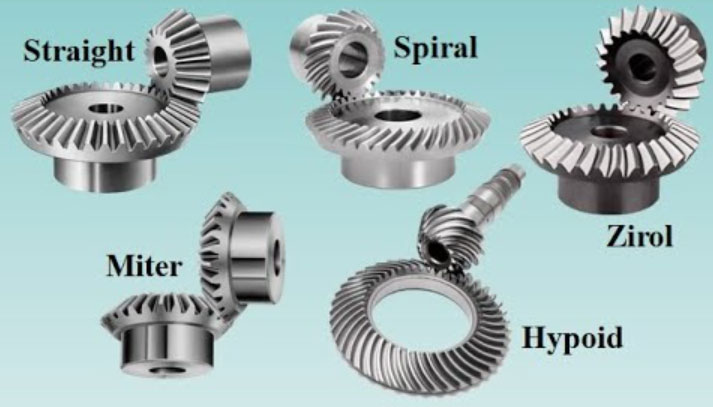
Bevel gears are a type of gear mechanism that transmit power and motion between intersecting or non-parallel shafts. They have conical-shaped teeth and operate on the principle of the meshing of these teeth to transfer torque and rotation. Bevel gears find applications in a wide range of industries, including automotive, aerospace, marine, industrial machinery, and robotics, among others. Let’s delve into the science of bevel gears, including their principles and applications:
1. Tooth Geometry:
Bevel gears have teeth that are cut on conical surfaces. The shape of the tooth is critical for proper functioning and efficient power transmission. The tooth geometry includes parameters such as the pitch angle, helix angle, module or diametral pitch, tooth thickness, and tooth profile. The precise tooth geometry determines the gear’s strength, load-carrying capacity, backlash, and meshing characteristics.
2. Gear Ratio and Speed Reduction/Increase:
Bevel gears provide different gear ratios depending on the number of teeth on the gears. The gear ratio determines the speed reduction or increase between the input and output shafts. Bevel gears can be designed to achieve specific gear ratios, allowing for the optimization of speed and torque in various applications.
3. Intersecting and Non-Parallel Shaft Arrangements:
Bevel gears are suitable for transmitting power between intersecting or non-parallel shafts. They can change the direction of rotation by 90 degrees or any other desired angle. The ability to transmit power at different angles makes bevel gears versatile for various applications where the input and output shafts need to be oriented differently.
4. Types of Bevel Gears:
There are several types of bevel gears, including straight bevel gears, spiral bevel gears, hypoid bevel gears, and zerol bevel gears. Each type has its unique tooth profile and characteristics. For example, spiral bevel gears have helical teeth that gradually engage, resulting in smooth operation and reduced noise compared to straight bevel gears. Hypoid bevel gears have offset axes and can transmit higher torque than other types.
5. Applications of Bevel Gears:
Bevel gears find applications in various industries and systems, including:
- Automotive: Differential systems, steering systems, transmissions, and engine timing systems.
- Aerospace: Helicopter transmissions, landing gear systems, flight control systems, and engine accessories.
- Marine: Propulsion systems, steering systems, winch systems, and gearboxes.
- Industrial Machinery: Gearboxes, material handling systems, pumping systems, and machine tools.
- Robotics: Robotic arms, joint mechanisms, and motion control systems.
The science of bevel gears involves careful design, precision manufacturing, and an understanding of their tooth geometry, gear ratios, load capacity, and operational requirements. By leveraging the principles of bevel gears, engineers can design systems with efficient power transmission, precise motion control, and reliable operation in various applications across industries.