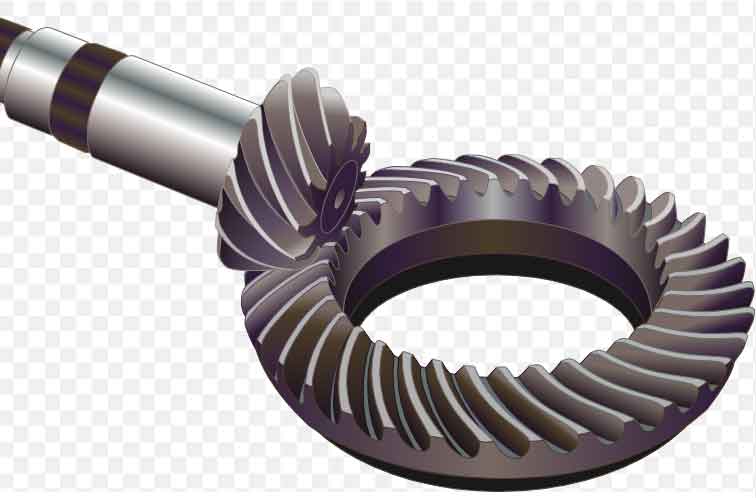
Spiral bevel gears are known for their precision and efficiency in gear systems. They offer several advantages that contribute to their ability to deliver precise motion control and efficient power transmission. Let’s explore how spiral bevel gears provide precision and efficiency in gear systems:
1. Precise Motion Control:
Spiral bevel gears are designed with a curved tooth profile that allows for gradual engagement and disengagement of the gear teeth. This results in smoother and more precise motion control compared to straight bevel gears. The gradual tooth contact minimizes shock and impact during gear meshing, enabling accurate positioning and controlled movement in gear systems.
2. Reduced Backlash:
Backlash refers to the clearance between the mating gear teeth and can negatively affect the precision of motion in gear systems. Spiral bevel gears, with their curved tooth profile, help minimize backlash. The spiral pattern ensures continuous contact between the gear teeth, reducing any free play and providing tighter control over gear positioning.
3. Efficient Power Transmission:
Spiral bevel gears offer efficient power transmission due to their curved tooth profile and increased contact area. The curved teeth allow for smooth rolling contact, reducing friction and power losses. The larger contact area distributes the load more evenly, resulting in improved torque transmission and reduced wear.
4. High Torque Capacity:
The spiral bevel gear design provides a large contact area between the teeth, enabling higher torque transmission capability compared to other gear types. This makes spiral bevel gears suitable for applications that require heavy-duty power transmission, such as in automotive differentials, industrial machinery, and aerospace systems.
5. Quiet Operation:
The gradual tooth engagement and smooth motion of spiral bevel gears contribute to quieter operation. The curved tooth profile reduces noise and vibration by minimizing impact and backlash during gear meshing. This is particularly beneficial in applications where noise reduction is essential, such as in precision machinery or noise-sensitive environments.
6. Versatile Applications:
Spiral bevel gears find applications in a wide range of industries and gear systems. They are commonly used in automotive differentials, machine tools, marine propulsion systems, aerospace systems, and various industrial machinery. Their ability to provide precise motion control, efficient power transmission, and reliable performance makes them suitable for diverse applications.
7. Long Service Life:
Spiral bevel gears, when properly designed, manufactured, and maintained, exhibit excellent durability and longevity. The curved tooth profile and optimized tooth contact pattern reduce wear and extend the gear’s service life. Proper lubrication and periodic maintenance further enhance their reliability and longevity.
These characteristics make spiral bevel gears highly desirable for applications that demand precise motion control, efficient power transmission, and reliable operation. By leveraging their precision and efficiency, gear systems can achieve optimal performance, reduced wear, and increased reliability in various industries.