Spiral bevel gears are designed based on a complex set of principles and considerations to achieve their unique functionality and performance. Let’s explore the science behind the design and functionality of spiral bevel gears:
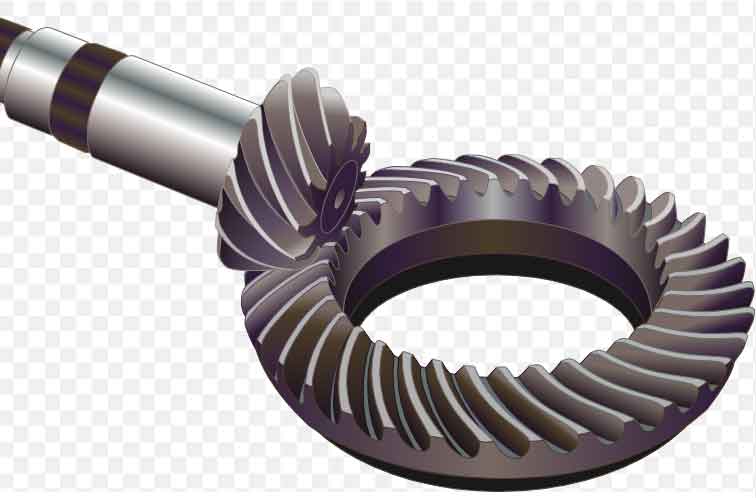
1. Tooth Geometry:
The teeth of spiral bevel gears are designed with a curved shape that gradually engages and disengages during rotation. This curved tooth profile allows for smoother motion, reducing impact and minimizing noise and vibration. The tooth geometry is typically derived using mathematical calculations, such as the Gleason or Klingelnberg method, to ensure proper tooth contact and load distribution.
2. Tooth Contact Pattern:
Achieving proper tooth contact is crucial for the smooth and efficient operation of spiral bevel gears. The goal is to have a uniform contact pattern along the tooth surfaces to distribute the load evenly. Computer-aided design (CAD) software and simulation tools, such as finite element analysis (FEA), are used to optimize the tooth contact pattern and minimize stresses and surface contact abnormalities.
3. Gear Ratio and Angle:
The gear ratio of spiral bevel gears determines the speed and torque relationship between the input and output shafts. The gear ratio is determined by the number of teeth on the gears and their relative sizes. The gear angle, also known as the spiral angle or helix angle, influences the smoothness of the gear operation and the load distribution. It is typically specified based on design considerations, such as torque requirements and space constraints.
4. Axial Thrust and Offset:
Spiral bevel gears generate an axial thrust force due to the helical nature of their teeth. This thrust force needs to be properly managed to prevent excessive axial loading on the gear shafts and bearings. Gear designs may incorporate features such as thrust bearings, preloading mechanisms, or offset pinions to counteract the axial thrust and ensure stable operation.
5. Manufacturing Processes:
The manufacturing of spiral bevel gears involves precision machining techniques. Computer numerical control (CNC) machines, gear hobbing, gear shaping, and grinding are commonly used to achieve the required gear tooth geometry and surface finish. Advanced manufacturing technologies and quality control processes ensure the accuracy, dimensional stability, and surface quality of the gears.
6. Lubrication and Maintenance:
Proper lubrication is essential for the smooth operation and longevity of spiral bevel gears. Lubricants help reduce friction, wear, and heat generation, extending the gear’s service life. It is important to select the appropriate lubricant based on the operating conditions and to establish regular maintenance practices, including lubricant monitoring and inspection of gear tooth condition.
The design and functionality of spiral bevel gears require a deep understanding of the principles of gear geometry, tooth contact patterns, and load distribution. The use of advanced design and simulation tools, along with precision manufacturing techniques and proper maintenance, ensures the efficient and reliable operation of spiral bevel gears in various applications.