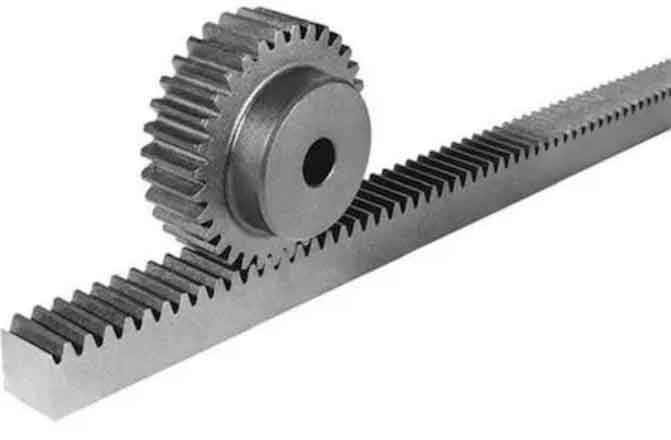
Advancements in rack and pinion gear manufacturing have significantly improved the precision and quality of these gear systems. Manufacturers are continually developing new techniques and technologies to enhance the manufacturing process and ensure superior performance. Here are some key advancements in rack and pinion gear manufacturing:
- CNC Machining: Computer Numerical Control (CNC) machining has revolutionized rack and pinion gear manufacturing. CNC machines offer high precision and accuracy in producing gear components, ensuring consistent quality and dimensional accuracy. Advanced CNC technology allows for complex geometries and tight tolerances, resulting in improved gear performance.
- Gear Shaping and Hobbing: Gear shaping and hobbing are traditional methods for manufacturing rack and pinion gears. Advancements in these techniques, such as improved cutting tools and machining parameters, have led to enhanced gear quality and efficiency. Modern gear shaping and hobbing machines are capable of producing high-precision gears with reduced noise and increased load-carrying capacity.
- Multi-Axis Milling: Multi-axis milling machines enable the production of complex rack and pinion gear geometries. These machines can accurately machine intricate tooth profiles and non-standard gear shapes, expanding the design possibilities for rack and pinion gear systems. Multi-axis milling ensures the precise form and smooth operation of the gears.
- Advanced Materials: The use of advanced materials in rack and pinion gear manufacturing has contributed to improved performance and durability. High-strength alloys, such as alloy steels and specialized gear materials, offer enhanced wear resistance, fatigue strength, and load-carrying capacity. The selection of appropriate materials ensures the gears can withstand demanding operating conditions and provide long-lasting performance.
- Heat Treatment and Surface Treatment: Heat treatment processes, such as carburizing, quenching, and tempering, are critical in enhancing the strength and hardness of rack and pinion gears. Advancements in heat treatment techniques, including precise control of temperature and time parameters, result in optimized gear properties. Surface treatments like nitriding or coating can further improve wear resistance and reduce friction, enhancing gear performance and extending their service life.
- Quality Control and Inspection: The implementation of advanced quality control and inspection methods ensures the precision and quality of rack and pinion gears. Advanced coordinate measuring machines (CMMs), gear inspection machines, and non-destructive testing techniques enable thorough dimensional and quality checks. These technologies help identify and rectify any manufacturing defects, ensuring that only gears meeting the highest standards are delivered to customers.
- Simulation and Design Optimization: Computer-aided design (CAD) and computer-aided engineering (CAE) software tools enable detailed simulation and optimization of rack and pinion gear designs. Virtual modeling and analysis help manufacturers refine gear designs, predict performance characteristics, optimize tooth profiles, and ensure efficient load distribution. These tools save time and resources by minimizing the need for physical prototypes and iterations.
Advancements in manufacturing processes, materials, quality control, and simulation techniques have collectively improved the precision, quality, and performance of rack and pinion gears. These advancements enable manufacturers to produce gears that offer enhanced reliability, durability, and efficiency in a wide range of applications.