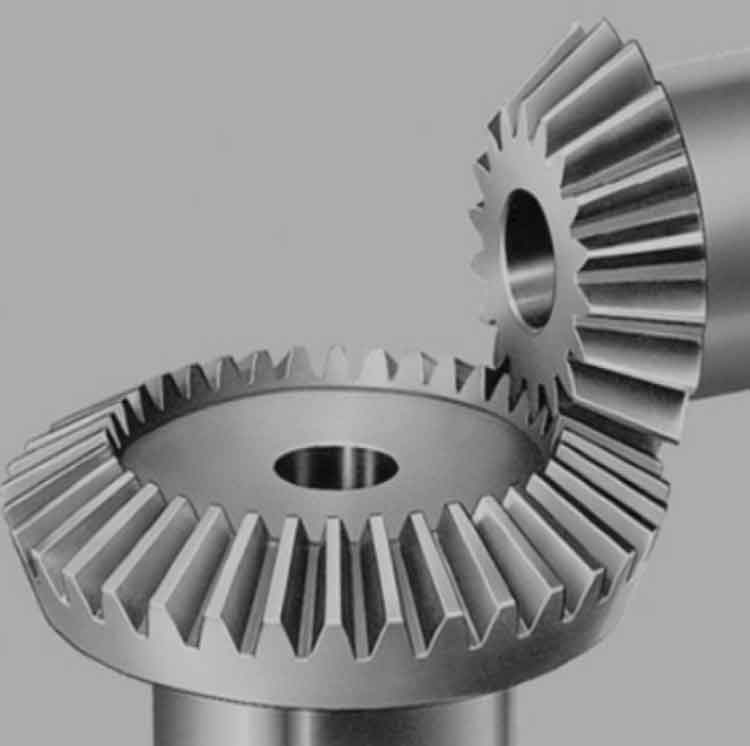
Straight bevel gears are a type of gears used in power transmission systems to transmit motion and power between two shafts that intersect at a specific angle. They have conical-shaped teeth and are commonly used in applications where the input and output shafts are at 90 degrees to each other.
Here are some basics of power transmission using straight bevel gears:
- Gear Design: Straight bevel gears have conical-shaped teeth that are cut on a conical surface. The gear teeth have straight and tapered profiles. The angle between the shafts, known as the pitch angle, determines the shape and size of the gears. The gear ratio is determined by the number of teeth on each gear.
- Tooth Engagement: The gear teeth of straight bevel gears mesh at a point of contact as they rotate. The point of contact moves along the tooth surface as the gears rotate. Proper alignment and engagement of the gears are crucial for efficient power transmission.
- Efficiency: Straight bevel gears have higher efficiency compared to other types of bevel gears due to their straight tooth profile. However, they may not be as efficient as parallel shaft gears like spur gears because of the sliding action that occurs during gear engagement.
- Applications: Straight bevel gears find applications in various industries and machinery. Some common uses include power tools, automotive differentials, marine drives, printing presses, and industrial machinery.
- Lubrication: Like any other gear system, straight bevel gears require proper lubrication to reduce friction and wear. Lubrication helps in reducing heat generation and extending the life of the gears.
- Noise and Vibration: Straight bevel gears can produce noise and vibrations during operation due to the sliding contact between the teeth. Proper design and maintenance can help minimize these issues.
- Load Capacity: The load capacity of straight bevel gears depends on factors such as the gear material, tooth design, and the applied load. It is important to consider the maximum torque and load requirements of the system to ensure the gears can handle the transmitted power.
- Maintenance: Regular inspection and maintenance are essential for the smooth operation of straight bevel gears. This includes checking for wear, proper alignment, lubrication, and replacing damaged or worn gears when necessary.
It’s important to note that while straight bevel gears are widely used, there are other types of bevel gears available, such as spiral bevel gears and hypoid gears, each with its own advantages and applications.