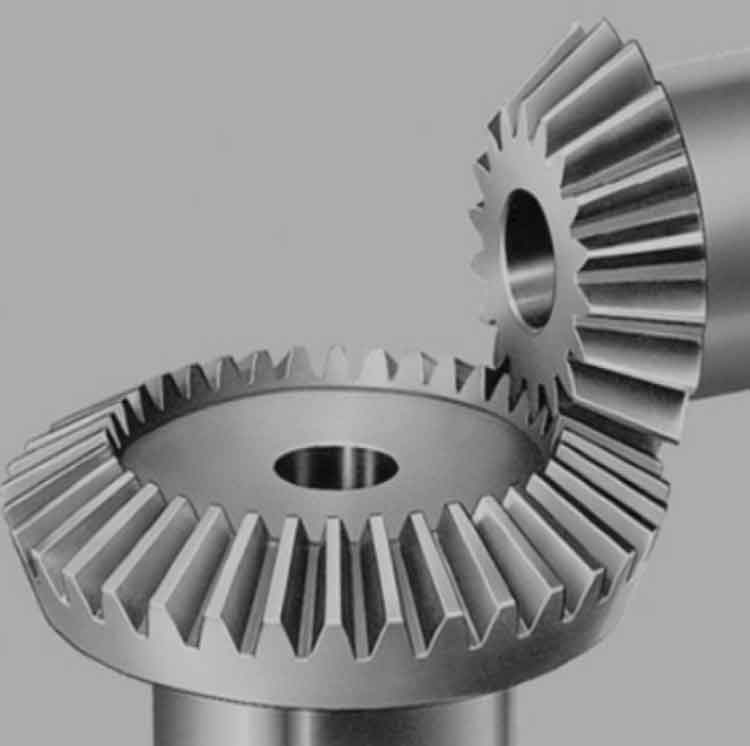
Straight bevel gears play a significant role in automotive engineering, contributing to the overall performance, efficiency, and reliability of vehicles. These gears are an essential component of the drivetrain system, transferring power from the engine to the wheels while enabling speed reduction or increase, torque multiplication, and direction changes. Let’s explore the role of straight bevel gears in driving innovation within the automotive industry.
- Power Transmission and Torque Distribution: Straight bevel gears are commonly used in the differential system of rear-wheel drive vehicles. The differential allows the wheels to rotate at different speeds while transmitting torque from the engine to the wheels. By utilizing straight bevel gears, the differential can efficiently distribute torque between the two wheels, ensuring optimal traction and stability during acceleration, deceleration, and cornering.
- Compact Design and Space Optimization: Straight bevel gears offer a compact and space-saving design, making them ideal for applications where space is limited, such as within the drivetrain. Their compactness allows automotive engineers to optimize the layout of the drivetrain system, achieving better weight distribution and improving overall vehicle handling and performance.
- Noise and Vibration Reduction: Straight bevel gears are known for their smooth and quiet operation, especially when compared to other gear types like spiral bevel gears. The teeth of straight bevel gears have a relatively simple geometry, resulting in less meshing noise and vibration. Noise reduction is crucial for enhancing the driving experience and minimizing noise pollution both inside and outside the vehicle.
- Efficiency and Power Transfer: Straight bevel gears have high mechanical efficiency, which is essential for minimizing power losses in the drivetrain system. Efficient power transfer leads to improved fuel economy, reduced emissions, and enhanced overall vehicle performance. By employing straight bevel gears, automotive engineers can optimize the gear tooth geometry, lubrication systems, and material selection to further enhance efficiency.
- Reliability and Durability: Straight bevel gears are known for their robustness and durability. They can withstand high loads and torque levels, making them suitable for demanding automotive applications. The materials used for manufacturing these gears, such as hardened steel alloys, ensure longevity and resistance to wear and fatigue. The reliability and durability of straight bevel gears contribute to the overall reliability of the vehicle, reducing maintenance costs and improving customer satisfaction.
- Advancements in Manufacturing Technology: The development of advanced manufacturing technologies, such as CNC machining, computer-aided design (CAD), and simulation software, has further driven innovation in straight bevel gear manufacturing. These technologies allow for precise and accurate production, optimizing the gear tooth profiles, reducing manufacturing variability, and improving gear performance. Additionally, the use of lightweight materials and innovative manufacturing techniques, such as 3D printing, has the potential to enhance the performance and efficiency of straight bevel gears.
In conclusion, straight bevel gears play a vital role in automotive engineering by enabling power transmission, torque distribution, compact design, noise reduction, efficiency, and reliability. Automotive engineers continue to innovate in the design, manufacturing, and optimization of straight bevel gears to further enhance vehicle performance, fuel efficiency, and overall driving experience.