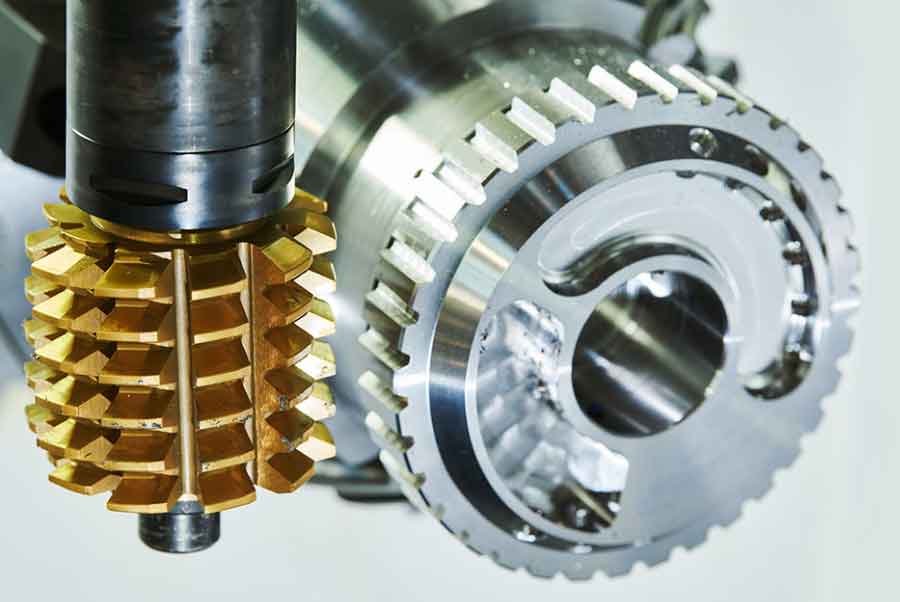
The gear hobbing process is a highly efficient method for manufacturing gears with precise tooth profiles and accurate dimensions. It involves the use of a specially designed cutting tool called a hob to cut the gear teeth into a workpiece. The gear hobbing process typically consists of the following steps:
1. Gear Design and Setup:
The gear hobbing process begins with the design of the gear profile. This includes determining the number of teeth, pitch, pressure angle, and other geometrical features of the gear. Once the gear design is finalized, the gear blank (workpiece) is prepared for the hobbing operation.
2. Mounting the Gear Blank:
The gear blank is mounted on the hobbing machine. The machine consists of a spindle that holds the workpiece and a hob that is positioned to cut the gear teeth. The gear blank is securely clamped to ensure precise positioning during the cutting process.
3. Selection of the Hob:
The hob is a cylindrical cutting tool with helical teeth that match the desired gear profile. The selection of the hob depends on the gear specifications, such as the module, pitch, number of teeth, and other design parameters. The hob must be chosen to precisely match the gear’s desired tooth profile.
4. Gear Hobbing Operation:
During the gear hobbing process, the hob and the gear blank rotate at specific speeds and ratios. The hob is fed into the gear blank, which rotates to create the relative motion between the hob and the workpiece. As the hob moves along the gear blank, it cuts the gear teeth into the workpiece.
5. Continuous Cutting:
Gear hobbing is a continuous cutting process, meaning that multiple gear teeth are cut in a single rotation of the workpiece. This results in high productivity and efficiency. The hobbing process continues until all the gear teeth have been cut into the workpiece.
6. Finishing and Deburring:
After the gear hobbing operation, the gear may undergo additional finishing processes to ensure the accuracy and quality of the gear teeth. Finishing operations may include gear shaving, grinding, or honing to achieve the desired surface finish and improve gear performance. Deburring is also done to remove any burrs or sharp edges that may have formed during the cutting process.
7. Quality Inspection:
Once the gear hobbing process and finishing operations are complete, the gear undergoes a thorough inspection to verify its accuracy and quality. Quality control measures may include checking the gear dimensions, tooth profile, surface finish, and hardness.
8. Surface Coatings (Optional):
In some cases, the gear may receive surface coatings or treatments to enhance wear resistance and reduce friction. Coatings like nitriding or carburizing are applied to improve the gear’s performance and longevity.
The gear hobbing process is a crucial technique for producing a wide range of gears used in various industries, including automotive, aerospace, robotics, and industrial machinery. Its ability to create precise gear profiles with high efficiency makes it a preferred method for mass production of gears. Skilled operators and advanced gear hobbing machines ensure the success of this precision manufacturing process.