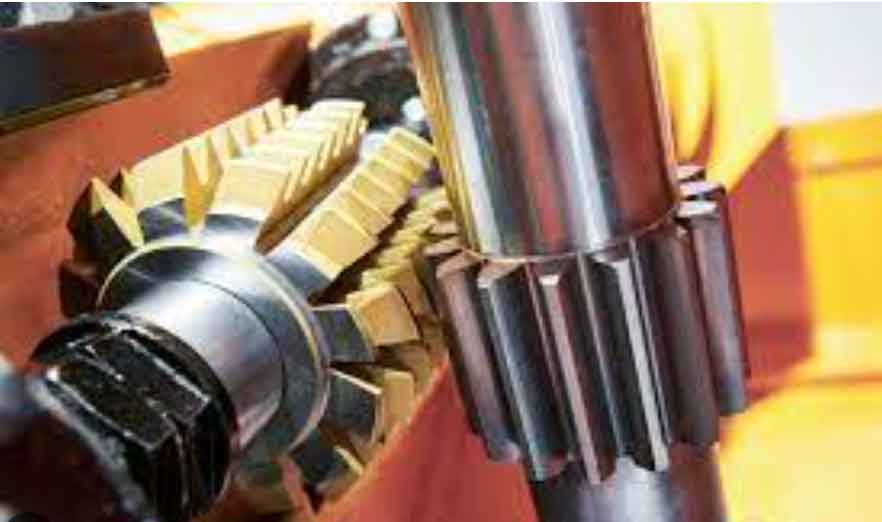
Gear hobbing is a precision machining process used for the manufacturing of gears. It is a highly efficient and accurate method for producing a wide range of gear types, including spur gears, helical gears, worm gears, and more. Gear hobbing is widely used in the gear manufacturing industry due to its ability to produce gears with excellent accuracy, surface finish, and dimensional consistency. Let’s explore the gear hobbing process and its key aspects:
Gear Hobbing Process:
Gear hobbing involves the use of a specialized cutting tool called a hob to generate the gear teeth. The hob is a cylindrical-shaped tool with helical cutting edges that match the desired gear’s tooth profile. During the hobbing process, the hob is fed into the workpiece blank (gear blank) while it rotates. The relative motion between the rotating hob and the gear blank creates the gear teeth through a process of continuous cutting.
Key Aspects of Gear Hobbing:
- Hob Design: The design of the hob is crucial to produce the desired gear profile accurately. The hob must match the gear’s tooth geometry, helix angle, pressure angle, and number of teeth.
- Feed and Speed Rates: The feed rate and rotational speed of the hobbing machine are carefully controlled to achieve the required gear tooth dimensions and surface finish. High-speed hobbing is common in modern gear manufacturing for increased productivity.
- Gear Blank Material: The choice of material for the gear blank is essential for gear hobbing. Common materials include various grades of steel, stainless steel, brass, and other alloys, depending on the application requirements.
- Gear Hobbing Machines: Gear hobbing machines are specialized equipment designed for the hobbing process. They come in different sizes and configurations, ranging from manual to fully automated CNC machines.
- Cutting Sequence: In multiple-cut gear hobbing, the gear teeth are generated in several passes, with each pass removing a portion of material to form the gear teeth gradually.
- Finishing Operations: After hobbing, the gears may undergo additional finishing operations, such as grinding, shaving, or honing, to achieve even higher precision and surface quality.
Advantages of Gear Hobbing:
- High Precision: Gear hobbing allows for precise and consistent tooth profiles, pressure angles, and tooth spacing, resulting in gears with excellent meshing characteristics.
- Efficiency: Gear hobbing is a highly efficient process, especially for mass production of gears, making it cost-effective for large quantities.
- Versatility: Gear hobbing can produce various types of gears, including spur gears, helical gears, and worm gears, with minimal tooling changes.
- Surface Finish: The gear hobbing process typically produces gears with a smooth and uniform surface finish.
- Consistency: Gear hobbing ensures consistency and repeatability in gear production, reducing the risk of dimensional variations.
In conclusion, gear hobbing is a precise and efficient machining technique widely used for the production of gears. It offers a cost-effective solution for manufacturing high-quality gears used in various industries, ranging from automotive and aerospace to industrial machinery and beyond.