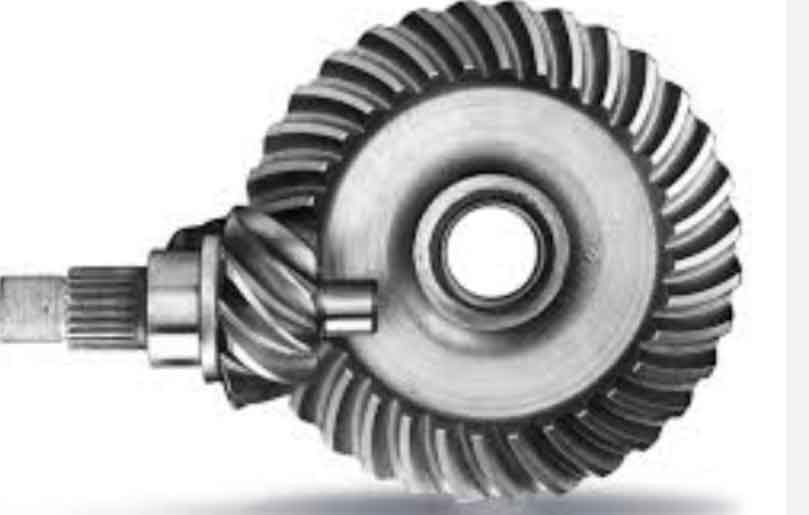
Case Study 1: Automotive Differential Gearbox
Objective: To design and optimize a hypoid gear-based differential gearbox for a high-performance sports car.
Challenges: The gearbox needed to handle high torque loads, provide smooth power delivery, and minimize noise and vibration. Space constraints were also a consideration due to the compact design of the sports car.
Solution: A hypoid gear differential was chosen for its ability to handle high torque and offset shaft design, allowing for a more compact gearbox layout. Advanced computer-aided design (CAD) software was used to optimize the gear tooth profiles and contact patterns, ensuring efficient power transmission and minimal noise generation.
Results: The optimized hypoid gear differential gearbox provided exceptional torque transfer, contributing to improved acceleration and handling. The offset shaft design allowed for a more efficient power flow, enhancing the car’s overall performance. The carefully designed tooth profiles and contact patterns reduced gear noise, providing a quieter and smoother driving experience for the sports car.
Case Study 2: Industrial Gearbox for Heavy Machinery
Objective: To design a robust and reliable gearbox for a large industrial machine used in mining operations.
Challenges: The gearbox needed to withstand heavy-duty applications, such as hauling and lifting heavy loads, while ensuring minimal downtime for maintenance and repairs.
Solution: Hypoid gears were selected for their high torque capacity and durability. The gearbox housing was designed with reinforced materials to handle the demanding conditions of the mining environment. Additionally, advanced lubrication and cooling systems were integrated to ensure optimal performance and extend the gearbox’s service life.
Results: The hypoid gear-based gearbox provided excellent torque transmission, enabling the industrial machine to efficiently handle heavy loads. The reinforced housing and advanced cooling systems minimized the risk of overheating and extended the gearbox’s operational life. As a result, the downtime for maintenance and repairs was significantly reduced, leading to increased productivity and cost savings for the mining operation.
Case Study 3: Robotics Joint Mechanism
Objective: To design a high-precision robotic joint mechanism for a surgical robot.
Challenges: The robotic joint required smooth and precise motion control, low backlash, and compact design to fit within the limited space of the surgical robot.
Solution: Hypoid gears were chosen for their low backlash and ability to provide smooth motion control. The compact design of hypoid gears allowed for the integration of a precise motion transmission system within the robotic joint.
Results: The hypoid gear-based robotic joint mechanism delivered precise and smooth motion control, enabling the surgical robot to perform delicate procedures with exceptional accuracy. The low backlash in the gear system ensured that the robot responded accurately to the surgeon’s commands, providing greater control and enhancing the overall performance of the surgical robot.
These case studies demonstrate the versatility and efficiency of hypoid gears in various gearbox applications. Whether in automotive differentials, heavy machinery, or robotics, the design and optimization of hypoid gear systems can lead to improved performance, enhanced durability, and a better overall user experience. The unique characteristics of hypoid gears make them a valuable choice in diverse industrial and automotive applications.