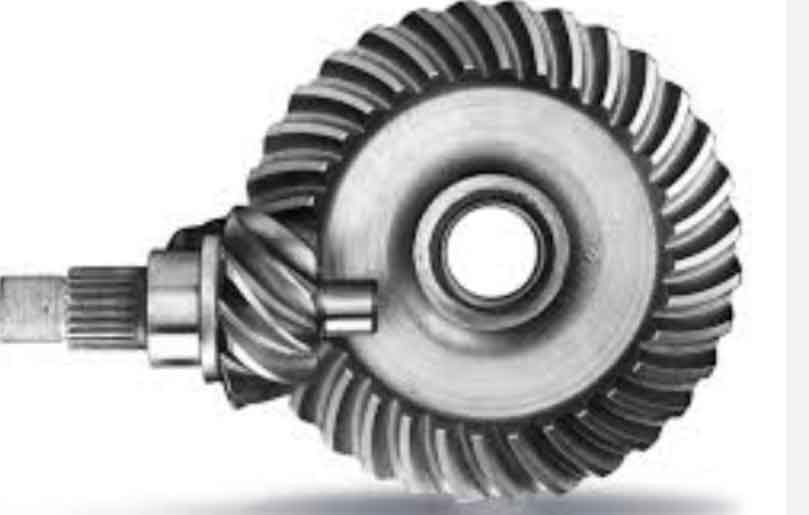
The future of hypoid gear technology is promising, with ongoing innovations and emerging trends that aim to enhance their performance, expand applications, and address industry challenges. Some of the key innovations and trends shaping the future of hypoid gears include:
1. Advanced Materials:
Manufacturers are exploring new materials and heat treatment processes to improve the strength, durability, and wear resistance of hypoid gears. The use of advanced materials, such as high-performance alloys and composites, can enhance the gear’s ability to withstand higher torque loads and harsh operating conditions.
2. Gear Geometry Optimization:
Advancements in computer-aided design (CAD) and simulation tools enable engineers to optimize the gear tooth profiles, contact patterns, and meshing characteristics of hypoid gears. This optimization can lead to better load distribution, reduced noise, and improved efficiency in power transmission.
3. Surface Finishing and Coatings:
Innovative surface finishing techniques and coatings are being explored to reduce friction and wear on hypoid gear surfaces. This can result in lower energy losses and extended gear life, making them more energy-efficient and cost-effective in various applications.
4. Automation and Industry 4.0 Integration:
Hypoid gear manufacturing processes are increasingly incorporating automation and robotics, leading to higher precision, repeatability, and efficiency. The integration of Industry 4.0 technologies, such as IoT sensors and data analytics, allows for real-time monitoring and predictive maintenance, optimizing gear performance and reducing downtime.
5. Noise and Vibration Reduction:
Research is ongoing to further minimize gear noise and vibration in hypoid gear systems. Advanced tooth modifications, improved gear mesh alignment, and innovative gear housing designs contribute to quieter and smoother gear operation.
6. Lightweight and Compact Designs:
As industries seek to reduce weight and space requirements, there is a trend toward designing lightweight and compact hypoid gear systems. This is particularly crucial in automotive, aerospace, and robotics applications, where weight and space constraints are critical factors.
7. Green Gear Technology:
With increasing emphasis on sustainability and energy conservation, the development of “green” gear technologies is gaining traction. Efforts to reduce energy losses and improve overall gear system efficiency align with global sustainability goals.
8. Application Diversification:
Hypoid gears are finding new applications in various industries beyond traditional automotive and industrial sectors. Advancements in gear design, manufacturing, and material technologies open doors for hypoid gears in areas such as renewable energy systems, medical devices, and advanced robotics.
9. Virtual Prototyping and Testing:
Simulation tools are becoming more sophisticated, allowing engineers to virtually prototype and test hypoid gear systems before physical manufacturing. This accelerates the design process, reduces costs, and leads to more reliable and optimized gear solutions.
10. Customization and Personalization:
The increasing demand for tailor-made solutions in specific industries drives a trend toward customization and personalization of hypoid gears. Manufacturers are offering gear designs optimized for specific applications and customer requirements.
The future of hypoid gear technology is marked by continuous innovations, advancing materials, and a growing range of applications. As engineers and researchers push the boundaries of gear design and manufacturing, hypoid gears are expected to play an integral role in addressing the evolving needs of industries for efficient, reliable, and high-performance power transmission systems.