Advancements in helical gear technology have significantly pushed the boundaries of gear design, leading to improved performance, reduced noise, and increased efficiency. Some of the key advancements include:
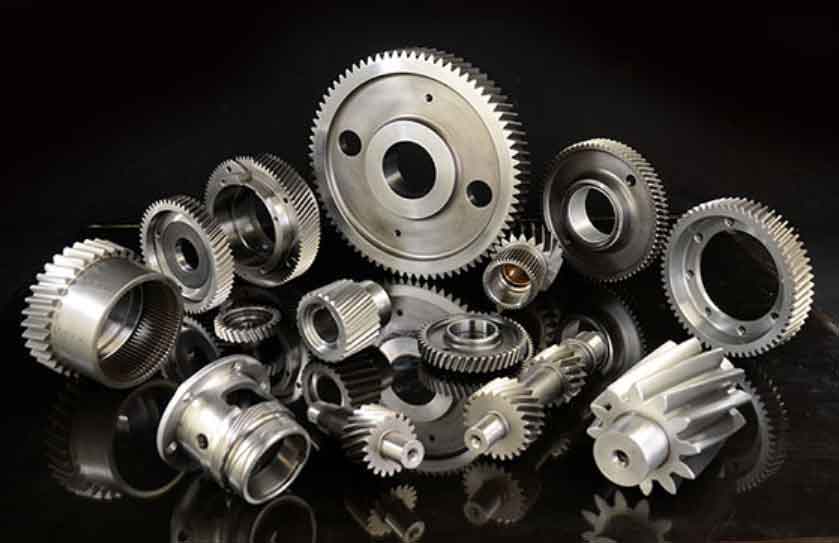
- Advanced Materials: The use of high-performance materials, such as advanced steels and alloys, allows for stronger and more durable helical gears. These materials can withstand higher loads and temperatures, increasing gear life and reliability.
- Computer-Aided Design (CAD): CAD software has revolutionized gear design by enabling precise modeling and simulation. Engineers can optimize gear profiles and tooth geometries for specific applications, resulting in more efficient and quieter gear sets.
- Finite Element Analysis (FEA): FEA techniques allow engineers to analyze stress distribution and deformation within helical gears under various loads. This helps identify potential failure points and optimize gear designs for enhanced performance.
- Multi-Axis CNC Machining: Advanced manufacturing technologies, such as multi-axis CNC machining, have improved the precision and consistency of helical gear production. This results in smoother gear surfaces and reduced noise during operation.
- Tooth Surface Modification: Tooth surface modification techniques, such as profile and lead crowning, are used to minimize edge contact and increase contact ratios. This reduces noise and improves load distribution across the gear teeth.
- Gear Grinding and Finishing: Gear grinding processes have become more advanced, allowing for tighter tolerances and smoother gear surfaces. Fine finishing techniques result in reduced friction and wear, enhancing gear efficiency.
- Additive Manufacturing: 3D printing or additive manufacturing is being explored for prototyping complex gear designs. This technology enables rapid iterations and the creation of customized helical gears for specific applications.
- Noise Reduction Features: Helical gears are designed with features like helix angles, lead angles, and modified tooth profiles to minimize noise and vibration during operation. These improvements lead to quieter gear systems.
- Improved Lubrication: Advanced lubricants and lubrication systems have been developed to reduce friction and wear between helical gear teeth. This results in better gear efficiency and extended gear life.
- Virtual Testing and Simulation: Virtual testing and simulation tools have become more sophisticated, allowing engineers to evaluate gear performance under various conditions without physical prototyping. This saves time and resources during the design process.
- Industry 4.0 Integration: The integration of IoT (Internet of Things) sensors and data analytics in gear systems enables real-time monitoring of gear performance. This data can be used for predictive maintenance, ensuring optimal gear operation.
These advancements in helical gear technology have contributed to more reliable and efficient gear systems across various industries, including automotive, aerospace, industrial machinery, and robotics. As technology continues to evolve, we can expect further innovations in helical gear design, manufacturing, and performance optimization.