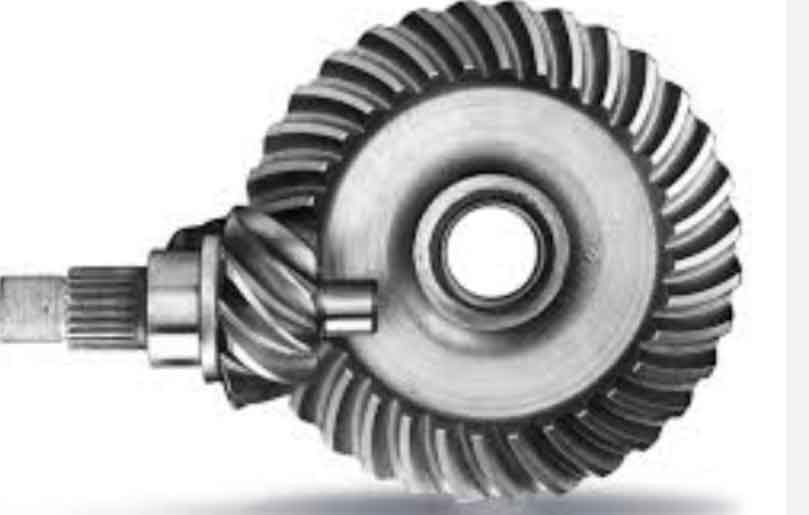
The automotive industry has seen significant advancements in recent years, and one area that has undergone a “quiet revolution” is noise reduction in vehicle components. Among these components, hypoid gears have played a crucial role in minimizing noise and improving overall driving experience. In this article, we’ll explore the concept of hypoid gears, their advantages over traditional bevel gears, and their application in noise reduction within automotive systems.
Hypoid Gears Explained:
Hypoid gears are a specific type of spiral bevel gears that have their axis of rotation offset from the axis of the gear. Unlike traditional bevel gears, which have intersecting axes, hypoid gears have axes that do not intersect. This unique design allows for smoother engagement between the gears, reducing noise and vibration during operation.
Advantages of Hypoid Gears in Noise Reduction:
- Improved Contact Ratio: The offset design of hypoid gears provides a larger contact ratio compared to traditional bevel gears. A larger contact ratio means that more teeth are engaged at any given moment, resulting in a smoother transfer of power and reduced noise.
- Surface Area Contact: Hypoid gears offer a greater contact area between the gear teeth, which distributes the load more evenly and reduces the intensity of pressure on individual teeth. This even distribution results in reduced wear and noise.
- Axial Offset: The offset axis of hypoid gears allows the pinion to be larger in diameter, leading to more significant teeth overlap during meshing. This results in a more gradual and smoother transition between gear teeth, which further contributes to noise reduction.
- Enhanced Lubrication: The larger gear surface area and smoother contact help maintain a continuous and efficient lubrication film between the gear teeth. Adequate lubrication significantly reduces friction and wear, leading to quieter gear operation.
Application in Automotive Systems:
Hypoid gears find extensive application in various automotive systems where noise reduction is a priority. Some notable areas include:
- Rear Axles: Rear axles in vehicles often utilize hypoid gears to transmit power from the driveshaft to the wheels. By incorporating hypoid gears in rear axle assemblies, manufacturers can achieve quieter and smoother performance, enhancing driving comfort.
- Transmissions: In modern automotive transmissions, hypoid gears can be used in differentials and final drives to reduce noise and improve power transfer efficiency. This is especially relevant for vehicles with front-wheel-drive layouts.
- Transfer Cases: For all-wheel-drive and four-wheel-drive vehicles, transfer cases can benefit from the use of hypoid gears. The reduction in noise and improved durability contributes to the overall performance of these vehicles, especially in off-road conditions.
The introduction of hypoid gears in automotive applications has brought about a “quiet revolution” in noise reduction. Their offset axis design, larger contact ratio, and enhanced lubrication capabilities make them superior to traditional bevel gears in terms of reducing noise and vibration. By incorporating hypoid gears in critical areas such as rear axles, transmissions, and transfer cases, automotive manufacturers can enhance the driving experience and improve customer satisfaction. As technology continues to evolve, we can expect further innovations in gear design, paving the way for quieter and more efficient vehicles in the future.