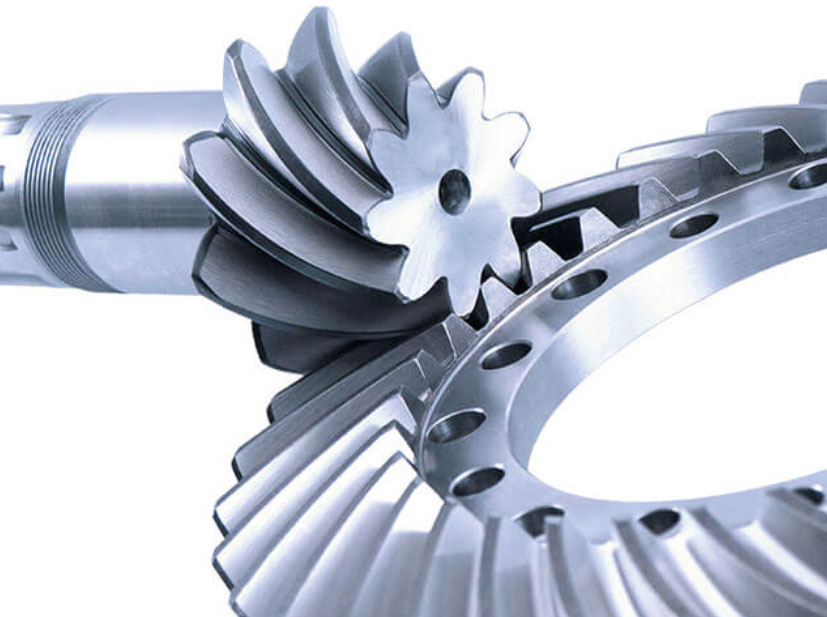
Spiral bevel gears are a type of bevel gear used in various mechanical systems to transmit power and motion between non-parallel intersecting shafts. Unlike straight bevel gears, which have teeth cut straight across the gear’s face, spiral bevel gears have teeth that are curved in a spiral manner. This design provides several advantages, including smoother operation, increased load-carrying capacity, and reduced noise and vibration.
Here’s a closer look at the design and functionality of spiral bevel gears:
- Tooth Profile: Spiral bevel gears have teeth with a curved profile that forms a spiral along the gear’s face. The tooth profile is carefully designed to ensure smooth contact between the mating gears, reducing wear and noise. The spiral angle is the angle between the tooth trace and an element of the pitch cone.
- Intersecting Shafts: Spiral bevel gears are used when the shafts they connect are not parallel but intersect at some point. This configuration allows power to be transmitted between intersecting shafts at a specific angle.
- Meshing Action: When two spiral bevel gears rotate, their teeth mesh in a rolling/sliding action. The contact between the gear teeth starts at one end of the tooth and gradually progresses along the tooth’s width, resulting in a smoother and more gradual transfer of force compared to straight bevel gears.
- Manufacturing: The manufacturing process of spiral bevel gears involves specialized cutting tools, such as Gleason or Klingelnberg machines. These machines use the concept of “generating” to produce the gears by moving the cutting tool along the gear tooth while the gear blank is simultaneously rotated.
- Applications: Spiral bevel gears are commonly used in applications where intersecting shafts are required, such as automotive differentials, helicopters, marine propulsion systems, power tools, and industrial machinery.
- Advantages:
- Smooth operation: The rolling/sliding meshing action reduces noise and vibration, leading to quieter and more efficient gear systems.
- High load-carrying capacity: The spiral tooth design allows for more contact between teeth, distributing the load over a larger area and increasing the gear’s ability to handle higher loads.
- Better efficiency: The rolling action and improved tooth contact result in reduced friction, leading to higher overall gear efficiency.
- Improved reliability: The gradual transfer of force and reduced wear contribute to longer gear life and increased reliability.
- Disadvantages:
- Complex design and manufacturing process: The design and manufacturing of spiral bevel gears are more intricate and require specialized equipment, making them relatively more expensive to produce.
- Limited interchangeability: Spiral bevel gears are usually designed for specific applications, limiting their interchangeability with other gear types.
In summary, spiral bevel gears are a critical component in various mechanical systems, providing smooth and efficient power transmission between intersecting shafts. Their unique tooth design and manufacturing process make them suitable for applications that demand high load-carrying capacity, reduced noise, and improved reliability.